10-K
UNITED STATES
SECURITIES AND EXCHANGE COMMISSION
WASHINGTON, D.C. 20549
FORM 10-K
|
| |
ý | ANNUAL REPORT PURSUANT TO SECTION 13 OR 15(d) OF THE SECURITIES EXCHANGE ACT OF 1934 |
| For the fiscal year ended December 31, 2015 |
OR
|
| |
¨ | TRANSITION REPORT PURSUANT TO SECTION 13 OR 15(d) OF THE SECURITIES EXCHANGE ACT OF 1934 |
| For the transition period from to |
Commission file number: 000-30939
ACTIVE POWER, INC.
(Exact name of registrant as specified in its charter)
|
| | |
Delaware | | 74-2961657 |
(State or other jurisdiction of incorporation or organization) | | (I.R.S. Employer Identification No.) |
| | |
2128 W. Braker Lane, BK 12, Austin, Texas | | 78758 |
(Address of principal executive offices) | | (Zip Code) |
(512) 836-6464
(Registrant’s telephone number, including area code)
Securities registered pursuant to Section 12(b) of the Act:
|
| | |
Title of Class | | Name of Exchange on Which Registered |
Common Stock, $0.001 per share | | The Nasdaq Stock Market LLC |
Securities registered pursuant to Section 12(g) of the Act:
(Title of Class)
Indicate by check mark if the registrant is a well-known seasoned issuer, as defined in Rule 405 of the Securities Act. o Yes ý No
Indicate by check mark if the registrant is not required to file reports pursuant to Section 13 or Section 15(d) of the Exchange Act. o Yes ý No
Indicate by check mark whether the registrant (1) has filed all reports required to be filed by Section 13 or 15(d) of the Securities Exchange Act of 1934 during the preceding 12 months (or for such shorter period that the registrant was required to file such reports), and (2) has been subject to such filing requirements for the past 90 days.ý Yes o No
Indicate by check mark whether the registrant has submitted electronically and posted on its corporate Web site, if any, every Interactive Data File required to be submitted and posted pursuant to Rule 405 of Regulation S-T (§ 232.405 of this chapter) during the preceding 12 months (or for such shorter period that the registrant was required to submit and post such files). ý Yes o No
Indicate by check mark if disclosure of delinquent filers pursuant to Item 405 of Regulation S-K is not contained herein, and will not be contained, to the best of registrant’s knowledge, in definitive proxy or information statements incorporated by reference in Part III of this Form 10-K or any amendment to this Form 10-K. ý
Indicate by check mark whether the registrant is a large accelerated filer, an accelerated filer, a non-accelerated filer, or a smaller reporting company. See the definitions of “large accelerated filer,” “accelerated filer,” and “smaller reporting company” in Rule 12b-2 of the Exchange Act. (Check one)
|
| | | |
Large accelerated filer ☐ | Accelerated filer ☐ | Non-accelerated filer ☐ | Smaller reporting company ý |
| | (Do not check if a smaller reporting company) |
Indicate by check mark whether the registrant is a shell company (as defined in Rule 12b-2 of the Exchange Act) o Yes ý No
The aggregate market value of the voting and non-voting common equity held by non-affiliates of the registrant, based upon the closing sale price of its common stock on the last day of registrant’s most recently completed second fiscal quarter, June 30, 2015, as reported on The Nasdaq Stock Market, was approximately $38.9 million (affiliates being, for these purposes only, directors and executive officers and holders of 10% or more of the registrant’s outstanding shares).
As of February 16, 2016, the registrant had 23,109,207 shares of common stock outstanding.
Documents Incorporated by Reference
Certain information required by Part III of Form 10-K is incorporated by reference to the registrant’s proxy statement for its 2016 Annual Meeting of Stockholders, which will be filed with the Securities and Exchange Commission within 120 days after the close of the registrant’s fiscal year ended December 31, 2015.
Active Power, Inc.
Unless otherwise indicated, “we,” “us,” “our,” and “Active Power” mean Active Power, Inc., including our predecessor Texas corporation and our subsidiary companies. References in this report to “$” or “dollars” are to United States of America currency.
Table of Contents
|
| | |
PART I | | |
| | |
| | |
| | |
| | |
| | |
| | |
| | |
| | |
| | |
| | |
| | |
| | |
| | |
PART II | | |
| | |
| | |
| | |
| | |
| | |
| | |
| | |
| | |
| | |
| | |
| | |
| | |
| | |
| | |
| | |
PART III | | |
| | |
| | |
| | |
| | |
| | |
| | |
| | |
| | |
| | |
| | |
| | |
PART IV | | |
| | |
| | |
Special Note Regarding Forward-Looking Statements
This report on Form 10-K contains forward-looking statements within the meaning of Section 27A of the Securities Act of 1933, as amended (the “Securities Act”), and Section 21E of the Securities Exchange Act of 1934, as amended (the “Exchange Act”). All statements other than statements about historical or current facts, including, without limitation, statements about our business strategy, plans, and objectives of management and our future prospects, are forward-looking statements. These include, among other things, statements regarding:
| |
• | our expectations that we can increase bookings and backlog; |
| |
• | our belief that we can improve operational efficiencies; |
| |
• | our ability to control our future expenses; |
| |
• | our ability to expand our sales distribution network; |
| |
• | our ability to diversify our revenue stream through sales to healthcare and industrial applications; |
| |
• | our future anticipated working capital needs; |
| |
• | our ability to raise additional cash if needed to fund our operations; |
| |
• | anticipated levels of bookings and revenue; |
| |
• | our ability to improve inventory turns and factory utilization; |
| |
• | expected fluctuations in currency exchange rates; and |
| |
• | our expectation that seasonal trends will continue in fiscal 2016. |
You can identify forward-looking statements by words such as “may,” “will,” “expect,” “intend,” “anticipate,” “believe,” “estimate,” “seek,” “continue,” and other similar words. You should read statements that contain these words carefully because they discuss our future expectations, make projections of our future results of operations or financial condition, or state other “forward-looking” information.
We claim the protection of the safe harbor for forward-looking statements contained in the Private Securities Litigation Reform Act of 1995 for all forward-looking statements. We have based these forward-looking statements on our current expectations and projections about future events. These forward-looking statements are subject to risks, uncertainties and assumptions about our business that could affect our future results and could cause those results or other outcomes to differ materially from those expressed or implied in the forward-looking statements. Factors that might cause or contribute to such differences include, but are not limited to, those discussed in “Risk Factors” included in Item 1A of this report and as may be updated in filings we make from time to time with the U.S. Securities and Exchange Commission (the “SEC”), including the Quarterly Reports on Form 10-Q to be filed by us in our fiscal year 2016.
We have no obligation to publicly update or revise any forward-looking statements, whether as a result of new information, future events or risks, except to the extent required by applicable securities laws. If we do update one or more forward-looking statements, no inference should be drawn that we will make additional updates with respect to those or other forward-looking statements. New information, future events or risks could cause the forward-looking events we discuss in this report not to occur. You should not place undue reliance on these forward-looking statements, which reflect our expectations only as of the date of this report.
PART I.
Overview
Active Power designs, manufactures, sells, and services flywheel-based uninterruptible power supply (“UPS”) products that use kinetic energy to provide short-term power as a cleaner alternative to electro-chemical battery-based energy storage. We also design, manufacture, sell, and service modular infrastructure solutions (“MIS”) that integrate critical power components into a pre-packaged, purpose built enclosure that may include our UPS products as a component. Our products and solutions are based on our patented flywheel and power electronics technology and are designed to ensure continuity for data centers and other mission critical operations in the event of power disturbances.
Our UPS products and solutions are designed to deliver continuous conditioned power during short-term power disturbances and outages, such as voltage sags and surges, and to provide ride-through power in the event of a utility failure, supporting operations until utility power is restored or a longer term alternative power source, such as a diesel generator, is started. We believe our products offer an advantage over those of our competitors in the areas of total cost of ownership, system reliability, and sustainability.
We have sold our flywheel-based UPS products which we call CleanSource® UPS since 1999. As of December 31, 2015, we have shipped more than 4,500 flywheels in UPS systems, delivering more than 1,000 megawatts of power to customers in more than 50 countries around the world, and providing more than 200 million runtime hours of operation.
In addition to selling stand-alone UPS products, our MIS products integrate critical power components into a pre-packaged, purpose built enclosure that can be deployed by customers indoors or outdoors. These solutions can provide the customer benefits of our UPS systems along with the advantages of lower capital expense, speed to deployment, and system management controls as compared to a conventional brick-and-mortar building. Our MIS products, for example, can include our UPS products with other related equipment including switchboards and automatic transfer switch; monitoring and control systems; fire detection; lighting; security; and air conditioning. Our CleanSource PowerHouse® is a complete stand-alone power solution integrating a diesel generator and our UPS.
We also integrate and build modular IT infrastructure solutions to specification based on customer designs. These solutions are typically enclosures that have a fully built out interior including electrical, cooling, monitoring, and other elements ready for the customer to add its IT racks and servers. These solutions typically do not include our UPS products. These modular IT solutions serve as the physical infrastructure for modular data center products which are self-contained, fully functioning data centers once the customer adds its IT equipment. These products can be deployed rapidly and at a lower cost than traditional brick-and-mortar solutions, and are optimally suited for hyperscale IT and cloud applications.
To date, we have deployed more than 200 infrastructure modules worldwide, which include both CleanSource PowerHouse and our modular IT solutions.
We offer worldwide customer support services, including hardware and software maintenance, on all Active Power products, and other professional services such as assessment, implementation and lifecycle support for our customers’ infrastructure projects.
We are headquartered in Austin, Texas, with international offices in the United Kingdom, Germany, and China.
In 2015, 72% of our product revenue came from the sale of UPS products and 28% from the sale of MIS products.
Customers and Target Markets
UPS products can be classified into single phase and three phase systems. We compete in the higher power, three phase range. Demand for three phase systems is typically segmented by kVA (kilo-Volt-Amps or power level) and by geography. We focus on customers desiring more than 250 kVA in all parts of the globe.
In 2015, IHS Research, a provider of global market, industry, and technical expertise, estimated this segment to be approximately $1.3 billion globally, and forecasted it to grow to be approximately $1.7 billion in 2019. IHS Research forecasts even more growth in the 500 kVA and higher segment, with a compound annual growth rate projected of approximately 7% from 2015 to 2019.
451 Research, an IT research and advisory company, estimated the market for prefabricated modular data center products in 2015 at approximately $1.2 billion, and forecasted growth to approximately $1.5 billion by 2016. We serve the modular data center market with our CleanSource PowerHouse and modular IT products.
We deliver products and solutions that support and enable mission critical applications that cannot tolerate downtime due to a power disturbance. Although data center deployments represent a large portion of our installed base, we also have had success in selling into non-IT environments. We are focusing on healthcare and industrial/manufacturing applications. Below are examples of the types of mission critical loads we protect with our products and solutions:
| |
• | Data Center – IT equipment in extreme/hyperscale, enterprise, and colocation facilities |
| |
• | Industrial/Manufacturing – precision machining, plastic extrusion equipment, and bottling equipment |
| |
• | Healthcare – imaging equipment (i.e. CAT, MRI, PET, etc.) and hospital data centers |
| |
• | Transportation – runway and taxiway lighting at airports |
| |
• | Broadcast – master control rooms and transmitter sites |
| |
• | Entertainment facilities - casino gaming machines and data centers as well as sports complex lighting |
The following list provides a representative sample of end user customers that use our products and solutions to support and enable their operations. The list includes customers to whom such products and solutions have been sold directly by us or via our Original Equipment Manufacturer (“OEM”) partners, manufacturer’s representatives, distributors, or strategic IT partners:
|
| |
Representative Customers | Industry |
Oracle | Data Center |
Verizon | Data Center |
Heineken | Industrial/Manufacturing |
Pemex | Industrial/Manufacturing |
Parkland Health and Hospital System | Healthcare |
Merck | Healthcare |
Cherokee Casinos | Entertainment |
Osage Casino | Entertainment |
Bangkok International Airport | Transportation |
Mexico City International Airport | Transportation |
WCBD-TV | Broadcast |
WFFF-TV / WVNY-TV | Broadcast |
Distribution
We continue to develop client relationships by selling directly and through our network of partners. Specifically, we use the following distribution methods:
| |
• | manufacturer’s representatives; |
Direct Sales. Our direct sales teams are located in The Americas, Europe, and Asia, and are supported by our four regional offices located in the U.S., United Kingdom, Germany, and China. Our direct sales teams are focused on establishing and expanding local presence and brand awareness, winning large customer orders, and developing the foundation for long-term client relationships in their local markets.
Manufacturer’s Representatives. We have relationships with a group of manufacturer’s representatives primarily in North America. Representatives have been granted rights to sell Active Power products in specific geographic territories. This channel remains integral to the distribution of our products in North America and increases our geographic sales coverage without adding fixed costs. Products are marketed and sold under the Active Power brand through this channel.
Distributors. In certain markets outside of the United States, we recruit and retain specific distributors to market our products and services. The distributor buys products from us and resells them to the end user, often with other products or services. Distributors may also perform service and warranty work for end users. This strategy has been successful for us in markets where we choose not to deploy direct sales or service resources.
OEM Partners. OEM partners remain critical to our overall business strategy. Our primary OEM partner and one of our largest customers is Caterpillar, Inc. (“Caterpillar”). Caterpillar markets Active Power’s UPS products under the Caterpillar brand name “CAT UPS” and as a complement to its electric power product lines of diesel engines and switchgear. By offering the CAT UPS with a standby generator and switchgear, Caterpillar can transform a standby power system into a continuous power system. We believe this total solution gives Caterpillar and us significant competitive advantages in the power quality market. In 2011, we signed a five-year distribution agreement with Caterpillar, continuing this important relationship that started in 1999. Unless terminated, this contract automatically renews for successive one-year periods. Our sales to Caterpillar represented 25%, 18%, and 14% of our total revenue for the years ended December 31, 2015, 2014, and 2013, respectively.
Strategic IT Partners. We have entered into agreements with leading global organizations in the data center market who have the ability to collaborate with us on new sales opportunities. These relationships help us expand potential opportunities to market our products and services through all of our distribution channels. Our primary IT partner is Hewlett Packard Enterprise Company (“HPE”). HPE accounted for 18%, 1%, and 22% of our total revenue during 2015, 2014, and 2013, respectively.
For risks related to our dependence with Caterpillar and HPE, see Part I - Item 1A. Risk Factors, "We are significantly dependent on our relationships with Caterpillar and Hewlett Packard Enterprise Company. If these relationships are unsuccessful, for whatever reason, our business and financial prospects would likely suffer."
Geography
We focus our marketing and customer identification efforts globally, supported by our four regional offices. Located in Austin, Texas; Osterode, Germany; Evesham, United Kingdom; and Beijing, China, our regional offices provide local sales and service, applications engineering, project management, and system integration for UPS and MIS products. Sales outside of North America accounted for approximately 30%, 42%, and 20% of our total revenues in 2015, 2014, and 2013, respectively. We expect a significant portion of our total revenue will continue to be through international sales. For additional detail on revenue from external customers attributed to foreign operations, see Footnote 9 to the consolidated financial statements in this Form 10-K. For risks related to revenue from external customers attributed to foreign operations, see Part I – Item 1A. Risk Factors, “We derive a substantial portion of our revenues from international markets and plan to continue to expand such efforts, which subjects us to additional business risks including increased logistical and financial complexity, managing internal controls and processes, political instability, and currency fluctuations.”
Products: UPS and MIS
UPS
Our UPS products serve two primary functions. First, during normal operations they are continuously conditioning (“cleaning”) the incoming power from the utility and delivering “conditioned” power to the client’s mission critical load. In this mode, the UPS regulates incoming utility power fluctuations in voltage and frequency. Second, if there is any interruption in the utility source, the UPS will provide temporary, or bridging power, until either the utility power is restored or an alternative generating source, such as a diesel generator, begins to provide power. This role of the UPS in the context of a continuous power application is illustrated below:
CleanSource 300/250 Series UPS
Active Power introduced the world’s first integrated flywheel UPS product in 1999, integrating proprietary UPS power electronics with flywheel energy storage technology. The flywheel stores kinetic energy – energy produced by motion – by constantly spinning a compact rotor in a low friction environment. When short-term backup power is required due to utility power fluctuations or losses, the UPS draws upon the stored kinetic energy of the spinning flywheel to generate electricity for the load until utility power returns. The flywheel immediately supports the critical load upon loss of utility power. Combining CleanSource UPS with a generator provides customers with complete short- and long-term protection in the event of a power disturbance. Within seconds of an extended outage occurring, the UPS signals the generator to start via the automatic transfer switch. The generator then carries the load until utility power is restored. The following is an illustration of our typical flywheel-based UPS system:
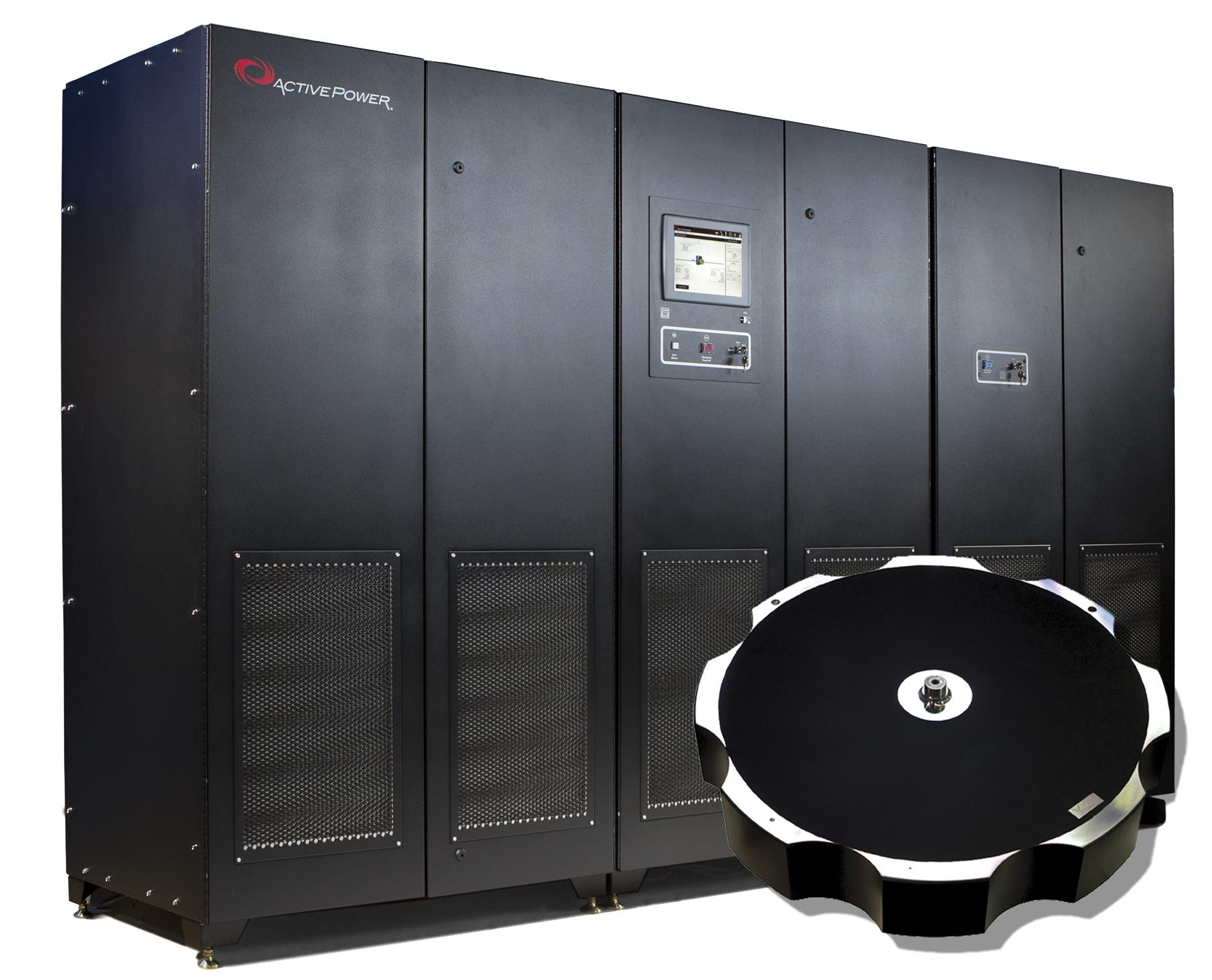
We market our flywheel-based UPS systems under the brand name CleanSource UPS rated at 300 kVA and 250 kVA for 480V and 400V applications, respectively. We currently offer CleanSource UPS products in power configurations ranging up to 1.5 MVA (million volt ampere) with the ability to parallel these products to provide even more protected power.
CleanSource HD UPS Series
In November 2012, we introduced our CleanSource 750/625HD UPS (see illustration below) which is available in standalone modules rated at 750 kVA and 625 kVA for 480V and 400V applications, respectively. This system is scalable and can be paralleled together to provide even more protected power. We believe CleanSource 750/625HD provides the reliability, power density, and total cost of ownership benefits that will make it a favorable complement to our existing products for large data center and other mission critical applications.
We also offer an Extended Runtime option on CleanSource HD UPS that can provide customers up to 30 minutes of additional UPS runtime. A secondary energy storage system, such as batteries or additional flywheel modules, supplements the primary flywheel and is available to those customers that require longer UPS autonomy.
Our UPS products represented 54%, 57%, and 37% of total revenue in 2015, 2014, and 2013, respectively.
Modular Infrastructure Solutions (MIS)
CleanSource PowerHouse
For customers looking for a complete, integrated continuous power system, we can package our CleanSource UPS along with switchboards and automatic transfer switch; monitoring and control systems; fire detection; lighting; security; and air conditioning into a fully integrated system. Due to the space efficiencies of our UPS products, we are able to offer all of these components in a pre-packaged containerized solution that we market under the brand name CleanSource PowerHouse (see illustration below).
CleanSource PowerHouse is packaged in a purpose-built enclosure that can be deployed by customers indoors or outdoors, with size and features customized depending upon the customer’s power load requirements and local and national regulatory requirements. These systems are specifically designed to handle the demands of data centers and other mission critical applications, providing lower acquisition cost, faster time to deployment, and improved management and control versus a conventional data center electrical room. Our systems are offered in ten standard modular power configurations that enable sizing for power (and cooling) infrastructure. CleanSource PowerHouse delivers significant value to customers as the entire system is integrated and tested prior to delivery for a repeatable and simple solution.
CleanSource PowerHouse is used to support a variety of applications including facility expansion, temporary critical power needs such as event support, disaster recovery, or to support a containerized data center.
Modular IT
We use our expertise in integration, containerization, and power distribution to manufacture containerized infrastructure solutions designed to specification for select business partners on a contract basis. Modular IT infrastructure solutions refer to the components of a containerized data center. These modular IT products can include an outer shell and outfitting the interior of the enclosure with electrical, cooling, and monitoring components. Our clients then add IT equipment including servers and racks, resulting in a self-contained modular data center that our partners deliver to end users. Modular IT systems may be rapidly deployed with CleanSource PowerHouse as a cost-effective alternative to traditional data center construction for a complete modular solution.
Our MIS products (CleanSource PowerHouse and modular IT) represented 21%, 17%, and 35% of total revenue in 2015, 2014, and 2013, respectively.
Service
We deliver worldwide customer support that offers clients assessment, implementation, and lifecycle support services for all Active Power products. Building a portfolio of services to work with clients through the lifecycle of their power assessment design and implementation process is a key element of our service growth strategy. We offer the following services to our clients:
| |
• | Deployment. Our experienced group of project managers will work with a client to develop a timely deployment schedule that avoids disrupting day-to-day business activity. We ensure expectations are clearly defined through the deployment phase; |
| |
• | Start-Up and Commissioning. Once the system is deployed, our team takes the system through a rigorous commissioning process to help ensure the system is working to specification. Our engineers work closely with the client’s team to make certain they are educated and trained on the successful operation of the system; |
| |
• | Service, Support and Monitoring. Clients can choose from a variety of comprehensive service and support offerings, tiered to match an organization’s internal capabilities and requirements. We also offer remote monitoring service through our headquarters in Austin, Texas, locally at the client’s facility, or as a combination offering; |
| |
• | Infrastructure Needs Assessment. We work locally through our global network of mission critical infrastructure engineers and project managers to assess the power and cooling needs of a client’s facility; |
| |
• | Vetting and Validation. Our teams of experienced application engineers use comprehensive assessments to vet and validate the optimal solution that complements a client’s business continuity plan; |
| |
• | Alignment with Business Objectives. Through continuous communication, our teams help ensure the solution accurately aligns with the original needs assessment and a client’s short-term and projected future business objectives; and |
| |
• | System Design. We design client solutions to ensure all components are optimized with a particular focus on reliability, efficiency, and cost effectiveness in determining the correct match and interoperability between components. |
Service revenues represented 25%, 26%, and 28% of our total revenue in 2015, 2014, and 2013, respectively.
UPS and MIS Market Drivers
We believe there are several market dynamics fueling the growth of the UPS and MIS markets and the need for reliable and sustainable low cost backup power. These include:
Increase in data usage and storage and in data center density:
| |
• | Growth of enterprise data, social networking sites, web-based applications, cloud computing, and other similar technologies requires data centers to invest in more IT and physical infrastructure equipment to support growth in use and storage requirements; |
| |
• | Additional IT and infrastructure requires more floor space; and |
| |
• | Enterprises’ need for more power density to accommodate IT equipment more efficiently within a given space. |
More awareness of energy efficiency from both a corporate social responsibility and financial perspective:
| |
• | More investment in highly efficient, sustainable technologies to keep electricity costs down and to stay competitive in the marketplace; |
| |
• | Customer preferences for clean, green technologies that do not contain toxic, harmful chemicals and avoid disposal costs associated with electro-chemical battery-based energy storage; |
| |
• | Government legislation and other cap and trade programs are becoming more prominent to help control carbon emissions; |
| |
• | Electricity costs are the single highest operating costs for many organizations due to the substantial amount of power needed to support data center facilities; and |
| |
• | Additional privacy legislation in Europe that resulted in data center operators maintaining data centers in multiple countries in Europe. |
Modular data centers are becoming more commonplace, not only for specific niche applications like military and high density computing environments:
| |
• | Colocation sites that house modular data centers are becoming more prevalent due to performance and tangible economic benefits; |
| |
• | Short lead times and rapid deployment capability are expected to increase demand for modular data center products, particularly for those organizations that do not have capital readily available to commit to building a brick and mortar facility; and |
| |
• | A modular design-build approach is a more capital efficient model that enables organizations to deploy IT and infrastructure as business and IT needs evolve, reducing underutilization. |
Customers focused on convenience and improving margins:
| |
• | Operators continue to focus on minimizing cost, cooling, and maintenance which in turn is driving down UPS runtime specifications; |
| |
• | More mission critical organizations are moving towards innovatively designed, turnkey data center and infrastructure solutions that involve less risk, cost, and complexity and more automation; and |
| |
• | Organizations want the ability to rapidly deploy IT and associated power and cooling infrastructure. |
Increase in global energy consumption:
| |
• | Rapid industrialization of highly populated world regions is increasing global energy demand and placing a premium on reliability of energy supply and sensitivity to loss of power; and |
| |
• | There is an increasing cost to produce and consume electricity due to depletion of finite fossil fuel sources, instability in oil-producing regions, and a preference for green energy sources. |
Increasing economic impact of a power interruption to users:
| |
• | The financial cost of a power interruption through loss of products, manufacturing down time, and computer processing interruptions; |
| |
• | Manufacturing and industrial environments are becoming more automated and digitized, particularly in the areas of process and machine control and material flow, making these applications prone to power quality issues and at risk for downtime; |
| |
• | Power quality is becoming more important to healthcare organizations with the increasing use of diagnostic imaging equipment and electronic medical records where a disturbance can lead to negative consequences including comprised patient safety and lost revenue; and |
| |
• | Reputational cost of a power interruption to businesses. |
Value Proposition
We believe our offerings deliver an unmatched combination of low total cost of ownership, reliability, and sustainability. The core differentiators for our products and solutions are the following:
Total Cost of Ownership
| |
• | Lower operating expenses through superior energy efficiency, reduced cooling needs, lower maintenance costs, and no required battery changes |
| |
• | Delivers up to 40% in total cost of ownership savings over 15 years |
Reliability
| |
• | Proven 12 times less likely to fail versus legacy UPS |
| |
• | Unique patented design delivers predictable, consistent, and continuous operation |
Sustainability
| |
• | Superior energy efficiency and power density to reduce fossil fuel generation |
| |
• | Permanent energy storage to minimize waste and emissions |
Competition
We compete with two primary products: UPS products and MIS products.
UPS Products. Our CleanSource UPS products compete primarily against conventional battery-based UPS systems from vendors such as Emerson/Liebert, Eaton/Powerware, and APC/MGE. We also compete against rotary (battery-free) UPS systems from vendors such as Piller, Eurodiesel, and Hitec. For applications requiring less than one megawatt of critical load, we largely compete against battery-based competitors and for applications greater than one megawatt we tend to compete against rotary systems vendors. We believe there is greater market acceptance of battery-free solutions (such as flywheel and rotary) compared to battery-based solutions in the one-megawatt and higher power range, making this an attractive market for our CleanSource 750/625HD UPS. Several of the leading conventional UPS battery vendors offer flywheel-based energy storage in place of batteries. Vycon is the principal manufacturer of these flywheel systems.
Our primary basis of competition as compared to battery-based UPS systems is our advantages in total cost of ownership, reliability, and sustainability. Our points of differentiation as compared to rotary UPS products are in space efficiencies (footprint) and total cost of ownership.
Modular Infrastructure Solutions. We provide competitive offerings in both the modular power and modular IT infrastructure segments. There are a variety of competitors with similar capabilities including systems integrators and value added service providers who may procure system components and assemble custom solutions. We believe that we are one of only a few manufacturers in the world offering pre-packaged standard modular power and IT solutions for quick delivery globally. Because of the significant up-front investment required, and the longer period between order and delivery relative to our UPS products, a significant increase in sales of our MIS products may materially increase the amount of working capital required to fund our operations.
The power density advantages we enjoy with our UPS products allow us to offer higher continuous power levels within the physical constraints of the containerized space compared to our battery-based competitors, which we believe is a barrier to entry for them. Our UPS products’ ability to operate in temperatures of up to 40 degrees Celsius in non-air -conditioned environments (such as a shell building or open-air facility) also acts as a competitive advantage for us compared to battery-based UPS systems which require sufficient air conditioning to operate.
We believe our experience with the power and cooling requirements of the infrastructure provides us with a competitive advantage in the design and manufacturing of these products compared to less experienced manufacturers. Further, the joint offering of our CleanSource PowerHouse with our modular IT solutions provides efficiencies, scale, and advantages in sales, marketing, and engineering we expect customers to find increasingly compelling.
Intellectual Property and Assets
We use proprietary manufacturing methods and techniques, as well as proprietary control algorithms for our products. We rely upon a combination of patents, trademarks, confidentiality agreements, and other contractual restrictions with employees and third parties to establish and protect these proprietary rights. We seek patent protection for inventions incorporated into our products where we believe obtaining such proprietary rights will improve our competitive position. While proprietary intellectual property is important to the Company, management believes the loss or expiration of any intellectual property right would not materially impact the Company.
We own the registered trademarks ACTIVE POWER, CLEANSOURCE, POWERHOUSE, and DRIVEN BY MOTION in the United States and abroad. The Active Power logo is a trademark of Active Power, Inc. All other trademarks, service marks, or trade names referred to in this report are the property of their respective owners.
Research and Development
We believe research and development efforts are essential to successfully delivering innovative products that address the current and emerging customer needs, particularly as power management/infrastructure needs evolve. Our research and development team works closely with our marketing and sales teams, IT channel partners, and OEMs to define product requirements that address specific customer needs. Our research and development expenses were $5.7 million, $6.7 million, and $7.4 million in 2015, 2014, and 2013, respectively. As of December 31, 2015, our research and development and engineering teams consisted of 29 engineers and technicians.
Manufacturing
We manufacture all of our UPS products for customers at our headquarters in Austin, Texas. MIS products for our customers in the Americas are manufactured at our facility in Austin. We are an ISO 9001:2008 quality certified operation. We source the majority of our components from contract manufacturers to enhance our ability to scale operations and minimize costs. This approach allows us to respond quickly to customer orders while maintaining high quality standards and optimizing inventory levels.
We strive to continually improve inventory turns through effective supply chain processes (e.g., supply base design, Kanban and vendor managed inventory) and supplier relationship management programs. We also have Lean programs in place to help us identify and eliminate waste and drive efficiencies throughout the company.
Our internal manufacturing process consists of the fabrication of certain critical components within the flywheel energy storage system and the assembly, functional testing, and quality control of our finished products. Our functional testing is system level testing that exercises the parts and subassemblies obtained from contract manufacturers for quality control purposes.
We have entered into long-term agreements with some of our key suppliers, but we currently purchase most of our components on a purchase order basis. We are working to renew or establish more long-term agreements with our sole suppliers and other key vendors. We utilize a rolling sales volume forecast to provide visibility to our supply base, which assists in ensuring component availability. We use standard parts and components for our products where possible, and have developed multiple sources for some of our most critical components including the flywheel rotors, cast housings, inductors and bearings. Lead times for ordering materials and components vary significantly and depend on factors such as material lead-time plus manufacturing cycle-time (driven by manufacturing complexity) and current market demand for such components or commodities.
We believe our current workforce, facilities, and inventory levels will be sufficient to handle our near-term projected sales demand. However, over time, we may need to hire additional manufacturing personnel with minimal equipment upgrades to address sales volume increases.
Local Assembly
For our MIS customers in Europe, we do much of the assembly, integration, and test work at our Evesham, UK facility. In Asia, this work is usually outsourced to local integration partners. A key component of our strategy is to maintain a flexible operating model that allows us to perform local integration, assembly, and testing of certain MIS products. We perform this work either at company managed facilities or with local integration partners that have assembly, integration, and test resources. We also have a full complement of integration, assembly, and test capabilities at our Austin, Texas facility.
Environmental Regulation
We must comply with many different federal, state, local, and foreign governmental regulations related to the use, storage, discharge, and disposal of certain chemicals and gases used in our manufacturing processes. Our facilities have been designed to comply with these regulations and we believe our activities are conducted in material compliance with such regulations. Any changes in such regulations or in their enforcement could require us to acquire costly equipment or to incur other significant expenses to comply with environmental regulations. Any failure by us to adequately control the storage, use, discharge, and disposal of regulated substances could result in significant future liabilities. Increasing public attention has been focused on the environmental impact of manufacturing operations. While we have not experienced any material adverse effects on our operations from recently adopted environmental regulations, our business and results of operations could suffer if for any reason we fail to control the storage or use of, or to adequately restrict the discharge or disposal of, hazardous substances under present or future environmental regulations.
Backlog
Normally, our products are shipped and revenue is recognized within three to six months from the date of the order. At times products are scheduled to ship in periods greater than this when the customer is constructing or expanding a new facility. Product revenue in any quarter is often dependent on orders booked and shipped throughout that quarter as historically our backlog has only provided a portion of the next quarter’s revenue. Service contracts, however, may extend for one or more years. We are attempting to increase the size of our backlog to promote greater efficiency in production, to facilitate business planning, and to improve revenue visibility. To support these efforts, we are working to drive consistent sales performance through targeted investing in and allocation of resources to our sales organization and distribution channels to build our backlog.
The dollar amount of backlog believed to be firm was approximately $30.8 million and $26.7 million at December 31, 2015 and 2014, respectively. This increase in backlog is primarily due to the restructuring of our sales organization, a shift in our market approach, and reengagement with our OEM partner Caterpillar. Of the total backlog, approximately $9.4 million and $5.4 million at December 31, 2015 and 2014, respectively, was not expected to be filled in the following year. These amounts include both long-term service contracts and product orders.
Backlog represents:
| |
• | anticipated revenue from unfulfilled product orders believed to be firm; and |
| |
• | service work not yet performed under signed contracts. |
Due to possible changes in product delivery schedules and the potential cancellation of unfulfilled product orders and service contracts, our backlog at any particular date should not be relied upon as being indicative of revenue for any succeeding period.
Employees
As of December 31, 2015, we had 219 total employees.
Seasonality
Our business has experienced seasonal customer buying patterns for a number of years. In recent years, both UPS and MIS sales were weaker in the first calendar quarter of the year. We believe this pattern, which we attribute to annual capital budgeting procedures, will continue. We also have historically seen a decline in demand for our products in Europe in the summer months compared to other regions because of reduced corporate buying patterns during the vacation season.
Where You Can Find Other Information
Active Power is a Delaware corporation originally founded in 1992 as a Texas corporation. We file annual, quarterly, current, and other reports, proxy statements, and other information with the SEC pursuant to the Exchange Act. You may read and copy any materials the company files with the SEC at the SEC’s Public Reference Room at 100 F Street, N.E., Washington, D.C. 20549. You may obtain information on the operation of the SEC’s Public Reference Room by calling the SEC at 1-800-SEC-0330. The SEC maintains an Internet site that contains reports, proxy, and other information statements, and other information regarding issuers, including Active Power, that file electronically with the SEC. The address of that site is www.sec.gov.
We maintain a website at www.activepower.com. We make available free of charge through this site our Annual Report on Form 10-K, quarterly reports on Form 10-Q, current reports on Form 8-K, and amendments to those reports filed or furnished pursuant to Section 13(a) or 15(d) of the Exchange Act as soon as reasonably practical after we electronically file such material with, or furnish it to, the SEC. This information can be found in the Investor Relations section of our website. The website and the information contained therein or connected thereto are not intended to be incorporated in this Annual Report on Form 10-K.
Executive Officers of the Company
The following table sets forth certain biographical information concerning our executive officers:
|
| | | | |
Name | | Age | | Position(s) |
Mark A. Ascolese | | 65 | | President and Chief Executive Officer |
James A. Powers | | 54 | | Chief Financial Officer and Vice President Finance |
Randall J. Adleman | | 58 | | Vice President of Global Sales and Marketing |
Mark A. Ascolese became President and Chief Executive Officer of Active Power on October 14, 2013. Mr. Ascolese has more than 40 years of experience serving a variety of mission critical and energy markets, including data centers. Prior to joining Active Power, Mr. Ascolese first served as CEO and then as Executive Board Chairman of Power Analytics Corporation (now part of Causam Energy, Inc.), an electrical infrastructure enterprise software firm focused on the mission critical and smart grid markets. Mr. Ascolese was appointed CEO of Power Analytics in March 2008 where he recruited the organization’s management team and created and implemented a successful strategic plan, transitioning the firm from a family owned company to a professionally managed business. In August 2012, Mr. Ascolese was appointed Executive Board Chairman at Power Analytics and served in this role prior to joining Active Power in October 2013. Previously, he served as President at Powerware Corporation (now part of Eaton Corporation) and in senior management positions at General Electric Company. From 2000 through 2002, Mr. Ascolese served as Senior Vice President of Business Development at Active Power during the company’s initial public offering. Mr. Ascolese earned a bachelor’s of Science in Commerce from the University of Louisville.
James A. Powers has served as Chief Financial Officer and Vice President of Active Power since December 4, 2013. As Chief Financial Officer and Vice President of Finance, he oversees all accounting, finance, treasury, and investor relations activities, as well as the company’s IT organization. From May 2013 until he joined Active Power, he served as Senior Vice President of Finance of the U.S. Windows and Doors division of Ply Gem Industries, Inc., a North American manufacturer of exterior building products. In this role, he managed the finance and IT organizations, leading all accounting, forecasting, budgeting, reporting, business analysis, internal controls, and working capital management activities. From May 2006 through May 2013, Mr. Powers served in various executive finance positions at Xerium Technologies Inc., a global manufacturer and supplier of consumable products and services used in various industries. From January 2011 through May 2013, he served as Vice President and Global Controller where he managed all corporate controllership functions, including SEC reporting and board financial reporting and analysis. From June 2008 through December 2010, Mr. Powers was Vice President of Finance, North America, at Xerium where he directed a broad range of financial functions. Prior to 2006, Mr. Powers served in various executive finance positions for international electrical equipment manufacturing businesses within Invensys Group PLC and ABB Ltd. Mr. Powers received a bachelor’s of Science in Accounting from the State of University of New York at Albany.
Randall J. Adleman served as Vice President of Global Sales and Marketing of Active Power from November 18, 2013, through February 2, 2016. In this role, he had overall responsibility for the company’s global sales and marketing organizations. From March 2010 until he joined Active Power, Mr. Adleman served as Vice President of Sales and Marketing for Valence Technology, Inc., a global manufacturer of lithium-ion energy storage solutions. There, he directed all worldwide sales and marketing efforts for the company’s motive, backup, industrial, and marine segments. Valence Technology filed a voluntary petition for chapter 11 business reorganization in the U.S. Bankruptcy Court for the Western District of Texas on July 12, 2012, during Mr. Adleman’s tenure as an executive officer. The U.S. Bankruptcy Court for the Western District of Texas approved the company’s exit from chapter 11 on November 13, 2013. Prior to that position, Mr. Adleman founded and served as Principal at Fords Barron Advisership, a corporate consultancy focused on sales force effectiveness. He has also held executive level sales positions at Misys Healthcare LLC, now part of Allscripts Healthcare Solutions, Inc.; Ingersoll-Rand plc; and Invensys Ltd. Powerware division, now part of Eaton Corporation plc. Mr. Adleman holds an undergraduate degree from Colgate University and a master’s in Business Administration with a concentration in Marketing from Fairleigh Dickinson University.
You should carefully consider the risks described below before making a decision to invest in our common stock or in evaluating Active Power and our business. The risks and uncertainties described below are not the only ones we face. Additional risks and uncertainties that we do not presently know, or that we currently view as immaterial, may also impair our business operations.
This Form 10-K contains forward-looking statements that involve risks and uncertainties. Our results could materially differ from those anticipated in these forward-looking statements as a result of certain factors, including the risks described below and elsewhere. See “Special Note Regarding Forward-Looking Statements.”
Risks Related to our Business
We have a history of significant operating losses.
We have incurred annual operating losses each year since our inception in 1992. Although we achieved operating profitability on a quarterly basis in the second quarter of 2012, we have not been able to sustain this and achieve quarterly or annual operating profitability since then. As of December 31, 2015, we had an accumulated deficit of $290.5 million. To date, we have funded our operations principally through the public and private sales of our stock, from borrowings under our credit facilities, from product and service revenue, and from development funding. We will need to generate significant additional revenue while maintaining our current margins to achieve annual profitability, and we cannot assure you that we will ever realize such revenue levels or achieve profitability on a consistent basis.
If our revenues do not meet our expectations, our costs exceed our estimates, or our working capital needs are greater than anticipated, we may not have adequate liquidity to continue operating our business. Our cash requirements will depend on many factors, including:
| |
• | the demand for our products; |
| |
• | the gross profit we are able to generate from our sales; |
| |
• | the timing, level, and extent of our research and development funding; |
| |
• | the rate of expansion of our sales and marketing activities; |
| |
• | the rate of expansion of our manufacturing processes; |
| |
• | our overall level of operating expenses; |
| |
• | the payment terms we negotiate with our suppliers; and |
| |
• | our default rates on receivables. |
A substantial increase in sales of our MIS solutions or a substantial increase in UPS sales may materially impact the amount of working capital required to fund our operations. In order to increase our MIS sales, we may be required to make larger investments in inventory and to increase the amount of our outstanding receivables. These larger investments may require us to obtain additional sources of working capital, debt, or equity financing in order to fund our business. Even if we obtain additional debt financing, a substantial portion of our operating cash flow may be dedicated to the payment of principal and interest on such indebtedness.
We may need additional capital in the future, and it may not be available to us on favorable terms, or at all.
We have historically relied on outside financing and cash flow from operations to fund our operating losses, operations, capital expenditures, and expansion. We may require additional capital from equity or debt financing in the future to fund our operations or respond to competitive pressures or strategic opportunities. We may not be able to secure timely additional financing on favorable terms, or at all. The terms of any additional financing may place limits on our financial and operating flexibility. If we are unable to obtain adequate financing or financing on terms satisfactory to us, if and when we require it, our ability to grow or support our business and to respond to business challenges could be significantly limited. We do not know whether we will be able to secure additional funding, or funding on terms acceptable to us, to continue our operations as planned. If financing is not available, we may be required to reduce, delay, or eliminate certain activities or to license or sell to others some of our proprietary technology.
Our business may be affected by general economic conditions and uncertainty that may cause customers to defer or cancel sales commitments previously made to us.
Any future economic uncertainty in the United States or certain international markets may lead to an economic recession or lower capital spending and credit availability in some or all of the markets in which we operate. A recession or even the risk of a potential recession or uneven economic growth conditions may be sufficient reason for customers to delay, defer, or cancel
purchase decisions, including decisions previously made. This risk is magnified for capital goods purchases such as UPS and MIS products that we supply. Although we believe that our competitive advantage and our efforts to broaden the number of different markets in which we sell may help mitigate the economic risk associated with any one country or market vertical, any customer delays or cancellation in sales orders could materially adversely affect our level of revenues and operating results.
Our backlog may not result in revenue.
Our backlog is not necessarily a meaningful predictor of future results. Backlog represents anticipated revenue from unfulfilled product orders and from service work not yet performed under signed contracts. Due to possible changes in product delivery schedules and the potential for cancellation of unfulfilled product orders and service contracts by our customers, our backlog at any particular date should not be relied upon as being indicative of revenue for any succeeding period. Time periods from receipt of an order to shipment date and installation vary widely, and may be determined by a number of factors, including the terms of the customer contract and the customer’s deployment plan. The value of service contracts included in backlog could cover services extending one or more years into the future. The size of an order or the scope of a service contract can be reduced significantly during the course of a project. If the scope of an order or contract is revised or an order or contract is canceled, we adjust backlog accordingly. Also, some of the orders we accept from customers require certain conditions or contingencies to be satisfied prior to shipment or prior to commissioning or installation, some of which are outside of our control and some of which may not be satisfied. For these and other reasons, we may not fully realize our backlog as revenue.
Our reliance on large and complex system solutions and customer concentration may adversely affect our ability to accurately predict the timing of revenues and to meet short-term expectations of operating results.
Our reliance on large and complex system solutions means that we must devote substantial effort and time to complete sales to customers. Further, a large portion of our quarterly revenue is derived from relatively few large transactions with relatively few customers. For example, in 2015 and 2014, our three largest customers contributed 48% and 30% of our revenue, respectively. Any delay in completing these large sales transactions or any reduction in the number of customers or large transactions, may result in significant adverse fluctuations in our quarterly revenue. Further, we use anticipated revenues to establish our operating budgets and a large portion of our expenses, particularly rent and salaries are fixed in the short term. As a result, any shortfall or delay in revenue could result in increased losses and would likely cause our operating results to be below public expectations. The occurrence of any of these events would likely materially adversely affect our results of operations.
Our financial results may vary significantly from quarter to quarter.
Our product revenue, operating expenses, and quarterly operating results have varied in the past and may fluctuate significantly from quarter to quarter in the future due to a variety of factors, many of which are outside of our control. As a result, you should not rely on our operating results during any particular quarter as an indication of our future performance in any quarterly period or fiscal year. The factors which may affect our business include, among others:
| |
• | timing of orders from our customers and the possibility that customers may change their order requirements with little or no notice to us; |
| |
• | demand for of our flywheel-based energy storage system as an alternative to lead-acid batteries and our continuous power and infrastructure solutions; |
| |
• | ongoing need for short-term power outage protection in traditional UPS systems; |
| |
• | deferral of customer orders in anticipation of new products from us or other providers of power quality systems; |
| |
• | our order backlog may not increase and does not always result in revenue; |
| |
• | limited visibility into customer spending plans; |
| |
• | timing of deferred revenue components associated with large orders; |
| |
• | ability to manage capital requirements associated with large orders; |
| |
• | timing and execution of our new product introductions; |
| |
• | new product releases, licensing, or pricing decisions by our competitors; |
| |
• | commodity and raw material component prices; |
| |
• | ability to adjust our cost structure in response to reductions in income; |
| |
• | loss of a significant customer or distributor; |
| |
• | impact of changes to our product distribution strategy and pricing policies; |
| |
• | failure to achieve our anticipated revenue growth rate; |
| |
• | impact of changes to our product distribution strategy and pricing policies of our distributors; |
| |
• | fluctuations in currency exchange rates; |
| |
• | changes in the mix of domestic and international sales; |
| |
• | rate of market growth for our products; and |
| |
• | acceptance of our latest generation UPS product in the marketplace. |
The market for power quality products is evolving and it is difficult to predict its potential size or future growth rate. Most of the organizations that may purchase our products have invested substantial resources in their existing power systems and, as a result, have been reluctant or slow to adopt a new technology, particularly during a period of reduced capital expenditures. Moreover, our current products are alternatives to traditional battery-based UPS systems and may never be accepted by our customers or may be made obsolete by other advances in power quality technologies.
Significant portions of our expenses are not variable in the short term and cannot be quickly reduced to respond to decreases in revenue. Therefore, if our revenue is below our expectations, our operating results are likely to be adversely and disproportionately affected. In addition, we may change our prices; modify our distribution strategy and policies; accelerate our investment in research and development; or shift our sales and marketing efforts in response to competitive pressures or to pursue new market opportunities. Any one of these activities may further limit our ability to adjust spending in response to revenue fluctuations. We use forecasted revenue to establish our expense budget. Because most of our expenses are fixed in the short term or incurred in advance of anticipated revenue, any shortfall in revenue may result in significant losses.
A significant increase in sales of our MIS products may materially increase the amount of working capital required to fund our operations.
Because of the significant up-front investment required, and the longer period between order and delivery relative to our UPS products, a significant increase in sales of our MIS products may materially increase the amount of working capital required to fund our operations. The amount of time between the receipt of payment from our customers and our expenditures for raw materials, manufacturing, and shipment of products (the cash cycle) for MIS sales can be as much as 210 days, depending on customer payment terms. If we experience a substantial increase in the size or number of MIS orders, we may need to obtain additional sources of working capital, debt, or equity financing to fund the business. If we are unsuccessful at obtaining additional sources of working capital, we may be required to curtail our level of MIS sales or we may lose potential customers, either of which may adversely impact our results of operations.
Our credit facility includes certain covenants and other events of default. Should we not comply with these covenants or incur an event of default, we may be required to repay our obligation in cash, which could have an adverse effect on our liquidity.
Our Second Amended and Restated Loan and Security Agreement dated August 5, 2010 (as amended on March 5, 2012, August 15, 2012, and July 28, 2014, the “Loan Agreement”) with Silicon Valley Bank (“SVB”) includes certain financial and administrative covenants, including a requirement to maintain a liquidity ratio equal to or greater than 1.25:1.00. The liquidity ratio is defined as unrestricted cash, cash equivalents and marketable securities on which bank has a perfected security interest, plus the aggregate amount of eligible accounts receivable accounts divided by all obligations we owe to SVB. If we fail to stay in compliance with our covenants or suffer some other event of default under the Loan Agreement, we may be required to repay the outstanding borrowings. Should this occur, our liquidity would be adversely impacted. For additional information related to the Loan Agreement, please refer to Footnote 4, “Revolving Credit Facility,” of the consolidated financial statements on pages 56 to 57 of this Form 10-K.
Our liquidity could be impacted by customer credit risk on receivables.
Most of our sales are on an open credit basis. Our failure to collect receivables from any of our customers in a timely manner could have a significant adverse effect on our liquidity. The collection risk may potentially increase if we sell a higher proportion of MIS, such as our CleanSource PowerHouse products, due to their higher average selling price. If future actual default rates on receivables differ from those currently anticipated, our working capital could decrease and we may not have adequate liquidity to continue operating our business.
We derive a substantial portion of our revenues from international markets and plan to continue to expand such efforts, which subjects us to additional business risks including increased logistical and financial complexity, managing internal controls and processes, political instability, and currency fluctuations.
The percentage of our total revenue derived from customers located outside of North America was 30%, 42%, and 20% in 2015, 2014, and 2013, respectively. Our international operations are subject to a number of risks, including:
| |
• | foreign laws and business practices that favor local competition; |
| |
• | dependence on local channel partners; |
| |
• | compliance with multiple, conflicting, and changing government laws and regulations; |
| |
• | difficulties in managing and staffing foreign operations; |
| |
• | foreign currency exchange rate fluctuations and the associated effects on product demand and timing of payment; |
| |
• | political and economic stability, particularly in the Middle East and Africa; |
| |
• | greater difficulty in the contracting and shipping process and in accounts receivable collection including longer collection periods; |
| |
• | ability to fund working capital requirements; |
| |
• | greater difficulty in hiring qualified technical sales and application engineers; and |
| |
• | difficulties with financial reporting in foreign countries. |
To date, the majority of our sales to international customers and purchases of components from international suppliers have been denominated in U.S. dollars, Euros, and British Pounds. All of our UPS products are manufactured in the U.S. and then sold to our foreign subsidiaries and customers, normally in U.S. dollars. An increase in the value of the U.S. dollar relative to foreign currencies could make our products more expensive for our international customers to purchase, thus rendering our products less competitive. We also source the non-UPS components for our modular power infrastructure products locally where possible and pay for these components in local currencies as a way to mitigate the impact of fluctuations in foreign currencies and lessen the impact of any unfavorable fluctuations with the U.S. dollar. We and many of our subsidiaries sell products outside of the country of incorporation, and often in foreign currencies. To the extent we record sales in other than our local currency; this can result in translation gains and losses. Currently, we do not engage in hedging activities for our international operations to offset this currency risk. However, we may engage in hedging activities in the future.
We are subject to risks relating to product concentration and lack of revenue diversification.
We derive a substantial portion of our revenue from a limited number of products, particularly from our CleanSource 300/250 Series UPS product family. These UPS products are also an integral component of our CleanSource PowerHouse products. We expect these products to continue to account for a large percentage of our revenues in the near term. Continued market acceptance of these products is therefore critical to our future success.
Our future success will also depend on our ability to reduce our dependence on these few products by developing and introducing new products and product or feature enhancements in a timely manner. Specifically, our ability to capture significant market share depends on our ability to develop and market extensions to our existing product lines at higher and lower power range offerings and as containerized solutions. We are currently investing significant amounts in our UPS and MIS products to broaden our product portfolio. Even if we are able to develop and commercially introduce new products and enhancements, they may not achieve market acceptance and the revenue generated from these new products and enhancements may not offset the costs, which would substantially impair our revenue, profitability, and overall financial prospects. Successful product development and market acceptance of our existing and future products depend on a number of factors, including:
| |
• | changing requirements of customers; |
| |
• | accurate prediction of market and technical requirements; |
| |
• | timely completion and introduction of new designs; |
| |
• | quality, price, and performance of our products; |
| |
• | availability, quality, price, and performance of competing products and technologies; |
| |
• | our customer service and support capabilities and responsiveness; |
| |
• | successful development of our relationships with existing and potential customers; and |
| |
• | changes in technology, industry standards, or end-user preferences. |
We must expand our distribution channels and manage our existing and new product distribution relationships to grow our business.
The future growth of our business will depend on our ability to expand our existing relationships with distributors; to identify and develop additional channels for the distribution and sale of our products; and to manage these relationships. As part of our growth strategy, we may expand our relationships with distributors and develop relationships with new distributors. We will also look to identify and develop new relationships with additional third parties that could serve as outlets for our products, or provide additional opportunities for our existing sales channels, such as the relationships we have developed with IT hardware manufacturers such as HPE. Our inability to execute this strategy successfully and to integrate and manage our existing OEM channel partners and our new distributors and manufacturer’s representatives would likely impede our future growth.
We must continue to hire and retain skilled personnel.
We believe our future success will depend upon our ability to attract, motivate, and retain highly skilled managerial, engineering, sales, and product marketing personnel. There is a limited supply of skilled employees in the power quality marketplace. Our small size relative to our competitors, our history of significant operating losses and our lack of brand equity, particularly in foreign markets, makes it very difficult for us to attract new personnel. If we are unable to attract the new personnel we desire, retain personnel we currently employ, or if we are unable to replace departing employees quickly, our operations and new product development may suffer.
We are significantly dependent on our relationships with Caterpillar and Hewlett Packard Enterprise Company. If these relationships are unsuccessful, for whatever reason, our business and financial prospects would likely suffer.
Caterpillar, together with its dealer network, is our primary OEM customer and the single largest customer for our flywheel-based UPS products. Caterpillar accounted for 25%, 18%, and 14% of our revenue in 2015, 2014, and 2013, respectively. HPE is our largest IT channel partner and accounted for 18%, 1%, and 22% of our revenue in 2015, 2014, and 2013, respectively. A number of factors could cause these customers to cancel or defer orders, including interruptions to their operations due to a downturn in their industries; delays or changes in their product offerings; securing other sources for the products we manufacture; or developing such products internally. If our relationships with Caterpillar or HPE are not successful or suffer a material adverse change, such as a material reduction in the level of orders due to an inability to win customer projects or other factors outside of our control; or their failure to pay us on a timely basis, our business and operating results would suffer unless we are able to replace these revenues from another source or sources in a timely manner.
We face significant competition from other companies.
The markets for power quality and power reliability systems are intensely competitive. There are many companies engaged in all areas of traditional and alternative UPS and backup power systems in the U.S. and abroad, including, among others, major electric and specialized electronics firms, as well as universities, research institutions, and foreign government-sponsored companies. There are many companies that are developing flywheel-based energy storage systems and flywheel-based power quality systems. We may face future competition from companies that are developing other types of emerging power technologies, such as advanced new battery chemistries, high-speed composite flywheels, ultra-capacitors, and superconducting magnetic energy storage.
Many of our current and potential competitors have longer operating histories, significantly greater financial, technical, service, marketing, and other resources, broader name and brand recognition, and a larger installed base of customers. As a result, these competitors may have greater credibility with our existing and potential customers and greater service infrastructure than we do. Given our current production volumes and lack of strategic supplier management programs, we may receive less favorable pricing from our suppliers than some of our larger competitors. Our competitors may be able to adopt more aggressive pricing policies and devote greater resources to the development, promotion, and sale of their products than we can, which would allow them to respond more quickly than us to new or emerging technologies or changes in customer requirements.
In addition, some of our current and potential competitors have established supplier or joint development relationships with our current or potential customers. These competitors may be able to use their existing relationships to discourage these customers from purchasing products from us or to persuade them to replace our products with their products. Increased competition could decrease our prices, reduce our sales, lower our margins, or decrease our market share. These and other competitive pressures could prevent us from competing successfully against current or future competitors and could materially harm our business.
We have underutilized manufacturing capacity and have no experience manufacturing our products in large quantities.
In 2001, we leased and equipped a 127,000 square foot facility used for manufacturing and testing of our three-phase product line, including our UPS and energy storage products. To be financially successful and to fully utilize the capacity of our facility and allocate its associated overhead, we must achieve significantly higher sales volumes. We must accomplish this while also preserving the quality levels we achieved when manufacturing these products in more limited quantities. To date, we have not been successful at increasing our sales volume to a level that fully utilizes the capacity of the facility and we may never increase our sales volume to necessary levels. If we do not reach these necessary sales volume levels, or if we cannot sell our products at our suggested prices, our ability to reach profitability on a quarterly or annual basis would be adversely impacted.
Achieving the necessary production levels to absorb the capacity of our manufacturing facility efficiently presents a number of technological and engineering challenges for us. We have not previously manufactured our products in high volume. We do not know whether or when we will be able to develop efficient, low-cost manufacturing capability and processes that will enable us to meet the quality, price, engineering, design, and product standards or production volumes required to manufacture large quantities of our products successfully. Even if we are successful in developing our manufacturing capability and processes, we do not know whether we will do so in time to meet our product commercialization objectives or to satisfy the requirements of our customers.
We must build quality products to ensure acceptance of our products.
The market perception of our products and related acceptance of such products is highly dependent upon the quality and reliability of the products we build. Any quality problems attributable to our UPS or MIS product lines may substantially impair our revenue and operating results. Moreover, quality problems for our product lines could cause us to delay or cease shipments of products or have to recall or field upgrade products, thus adversely affecting our ability to meet revenue or cost targets. In addition, while we seek to limit our liability as a result of product failure or defects through warranty and other limitations, if one of our products fails, a customer could suffer a significant loss and seek to hold us responsible for that loss and our reputation with other current or potential customers would likely suffer.
We depend on sole and limited source suppliers and outsource selected component manufacturing.
We purchase some of our critical component parts from sole source and limited source suppliers. If our suppliers receive excess demand for their products, we may receive a low priority for order fulfillment as large volume customers may receive priority that may result in delays in our acquiring components. A delay in acquiring components for our products may delay the manufacture and shipment of our products. Some of these delays may be substantial. As a result, we may purchase critical long-lead time or single-sourced components in large quantities to help protect our ability to deliver finished products on time. If we overestimate our component requirements, we may have excess inventory, which will increase our costs. If we underestimate our component requirements, we will have inadequate inventory, which will delay our manufacturing and render us unable to deliver products to customers on scheduled delivery dates. If we are unable to obtain a component from a supplier or if the price of a component has increased substantially, we may be required to manufacture the component internally, which will also result in delays or we may be required to absorb price increases. Manufacturing delays could negatively impact our ability to sell our products and could damage our customer relationships.
To assure the availability of our products to our customers, we outsource the manufacturing of selected components prior to the receipt of purchase orders from customers based on their forecasts of their product needs and internal product sales revenue forecasts. However, these forecasts do not represent binding purchase commitments from our customers. We do not recognize revenue for such products until we receive an order from the customer and the product is shipped to the customer. As a result, we incur inventory and manufacturing costs in advance of anticipated revenue. As demand for our products may not materialize, this product delivery method subjects us to increased risks of high inventory carrying costs, obsolescence and excess, and may increase our operating costs. In addition, we may from time to time make design changes to our products, which could lead to obsolescence of inventory.
Our manufacturing operations are concentrated in a small number of nearby facilities.
All of our UPS systems and our MIS products for customers in the Americas are manufactured in our Austin, Texas facility. Our manufacturing, research and development, and administrative activities are concentrated in two nearby facilities. If, for any reason, including as a result of a natural disaster, act of terrorism, or other similar event, either of these facilities should be damaged or destroyed or become inoperable or inaccessible, our ability to conduct our business could be adversely affected or interrupted entirely.
We may be unable to protect our intellectual property and proprietary rights.
We expect future technological advancements made by us will be critical to achieving and sustaining market acceptance of our products. We rely on a combination of patent, copyright, trademark, and trade secret laws and restrictions on disclosure to protect our intellectual property rights. We also enter into confidentiality or license agreements with our employees, consultants, and business partners and control access to and distribution of our software, documentation, and other proprietary information.
Despite these efforts, unauthorized parties may attempt to copy or otherwise obtain and use our products or technology. Monitoring unauthorized use of our products is difficult, and we cannot be certain the steps we have taken will prevent unauthorized use of our technology, particularly in foreign countries where applicable laws may not protect our proprietary rights as fully as in the U.S. In addition, the measures we undertake may not be sufficient to protect our proprietary technology adequately and may
not preclude competitors from independently developing products with functionality or features similar to those of our products. We believe that our success depends more on the knowledge, passion, experience and technological expertise of our employees than on the legal protection that our patents and other proprietary rights might afford.
We may be subject to claims by others that we infringe on their proprietary technology.
In recent years, there has been significant litigation in the U.S. involving patents, trademarks, and other intellectual property rights. We may become involved in litigation in the future to protect our intellectual property or defend allegations of infringement asserted by others. Legal proceedings could subject us to significant liability for damages or invalidate our intellectual property rights. Any litigation, regardless of its merits or its outcome, would likely be time consuming and expensive to resolve and would divert management’s time and attention. Any potential intellectual property litigation also could force us to take specific actions, including:
| |
• | cease selling our products that use the challenged intellectual property; |
| |
• | obtain from the owner of the infringed intellectual property right a license to sell or use the relevant technology or trademark, which license may not be available on reasonable terms, or at all; |
| |
• | redesign those products that use infringing intellectual property; or |
| |
• | cease to use an infringing trademark. |
Our involvement in any such litigation may cause us to incur unexpected litigation costs, require modifications to or limit our ability to sell our products, and adversely impact our business and reputation.
Our internal control over financial reporting may not prevent or detect misstatements because of its inherent limitations.
Pursuant to the Sarbanes-Oxley Act of 2002, we are required to provide a report by management on our internal control over financial reporting, including management’s assessment of the effectiveness of such control. Internal control over financial reporting may not prevent or detect misstatements because of its inherent limitations, including the possibility of human error, the circumvention or overriding of controls, or fraud. Therefore, even effective internal controls can provide only reasonable assurance with respect to the preparation and fair presentation of financial statements. In addition, projections of any evaluation of effectiveness of our internal control over financial reporting to future periods are subject to the risk that the control may become inadequate because of changes in conditions, or that the degree of compliance with the policies or procedures may deteriorate. If we fail to maintain the adequacy of our internal controls, including any failure to implement required new or improved controls, or if we experience difficulties in their implementation, our business and operating results could be harmed and we could fail to meet our reporting obligations.
A material weakness or other control deficiency could result in errors in our reported results and could have a material adverse effect on our operations.
A material weakness is a control deficiency or combination of control deficiencies, such that there is a reasonable possibility that a material misstatement of annual or interim financial statements will not be prevented or detected. In 2013, our management identified a material weakness resulting from control deficiencies related to our credit approval process whereby we did not confirm information from an employee of ours in China regarding the facts surrounding Qiyuan, a distributor with which we entered into a distribution agreement.
In response to such material weakness, management implemented additional credit approval process procedures including actions to further verify the financial condition and ownership structure of all new customers. The material weakness was remediated as of December 31, 2013. Any further material weakness or unsuccessful remediation could adversely impact investor confidence in the accuracy and completeness of our financial statements. As a result, our ability to obtain any additional financing could be materially and adversely affected, which in turn could materially and adversely affect our business and our financial condition. In addition, perceptions of us among customers, lenders, investors, securities analysts, and others could also be adversely affected. We can give no assurances the measures we have taken to date, or any future measures we may take, will prevent or remediate any additional material weaknesses in the future.
Our pending legal matters have increased our costs and could result in fines and penalties.
We are involved in legal matters from time to time. These matters may harm our business and liquidity in the future. We have incurred and may continue to incur substantial expenses for legal and accounting services related to such matters. These matters have also required significant time and attention from our management. At this point, we remain unable to predict the
duration, scope, or results of the pending SEC investigation described in Footnote 7, "Contingencies," of the consolidated financial statements on page 60 of this Form 10-K. We may incur defense costs that may exceed our insurance coverage. We may also incur costs if the insurers of our directors and officers and our liability insurers deny coverage for the costs and expenses related to any litigation. Adverse outcomes or other developments during the course of such matters may harm our business, financial condition, results of operations, or liquidity.
Cybersecurity incidents could disrupt business operations, result in loss of critical and confidential information, and adversely impact our reputation and results of operation.
Global cybersecurity threats can range from uncoordinated individual attempts to gain unauthorized access to our information technology (IT) systems to sophisticated and targeted measures known as advanced persistent threats. While we employ comprehensive measures to prevent, detect, address, and mitigate these threats (including access controls, data encryption, vulnerability assessments, continuous monitoring of our IT networks, and systems and maintenance of backup and protective systems), cybersecurity incidents, depending on their nature and scope, could potentially result in the misappropriation, destruction, corruption, or unavailability of critical data and confidential or proprietary information (our own or that of third parties) and the disruption of business operations. The potential consequences of a material cybersecurity incident include reputational damage; litigation with third parties; diminution in the value of our investment in research; development and engineering; and increased cybersecurity protection and remediation costs; which in turn could adversely affect our competitiveness and results of operations.
Tax matters could adversely impact our results of operations and financial condition.
We are subject to potential income tax and other taxes in the United States and in foreign jurisdictions. Our tax liabilities are affected by the amount of income we have in various jurisdictions and the amounts we charge in intercompany transactions for products, services, funding, and other items. We are subject to periodic tax audits in the United States and in other various jurisdictions. Tax authorities may disagree with our intercompany charges, cross-jurisdictional transfer pricing, or other matters and assess additional taxes. We assess the likelihood of adverse outcomes resulting from these examinations to determine the need for and adequacy of a provision for income taxes. However, the outcomes from these examinations could have an adverse effect on our provision for income taxes and cash tax liability. In addition, our income taxes and other tax liability in the future could be adversely affected by numerous factors including changes in tax laws, regulations, accounting principles, or interpretations thereof, which could adversely impact our results of operations and financial condition.
Seasonality may contribute to fluctuations in our quarterly operating results.
Historically, our business has experienced seasonal customer buying patterns. In recent years, our business has generally experienced relatively weaker demand in the first calendar quarter of the year. We believe this pattern, which we attribute to annual capital budgeting procedures, may possibly continue. In addition, we anticipate demand for our products in Europe may decline in the summer months, compared to other regions, because of reduced corporate buying patterns during the vacation season.
Risks Related to our Common Stock
We have anti-takeover provisions that could discourage, delay or prevent our acquisition.
Provisions of our certificate of incorporation and bylaws could have the effect of discouraging, delaying, or preventing a merger or acquisition that a stockholder may consider favorable. We also are subject to the anti-takeover laws of the State of Delaware, which may further discourage, delay, or prevent someone from acquiring or merging with us. In addition, our agreement with Caterpillar for the distribution of UPS products provides that Caterpillar may terminate the agreement in the event we are acquired or undergo a change in control. The possible loss of a significant customer could be a significant deterrent to possible acquirers and may substantially limit the number of possible acquirers. All of these factors may decrease the likelihood we would be acquired, which may depress the market price of our common stock.
The trading price of our common stock has been volatile and is likely to be volatile in the future.
Historically, the market price of our common stock has fluctuated significantly. In 2015, the sales price of our common stock ranged from $1.16 to $2.60 per share. In addition to the other risks described in the “Risk Factors” section of this Form 10-K, the market price of our common stock can be expected to fluctuate significantly in response to numerous other factors, many of which are beyond our control, including the following:
| |
• | actual or anticipated fluctuations in our operating results; |
| |
• | changes in financial estimates by securities analysts, any financial guidance we may provide, or our failure to perform in line with such estimates or guidance; |
| |
• | changes in market valuations of other technology companies, particularly those that sell products used in power quality systems; |
| |
• | announcements by us or our competitors of significant sales, technical innovations, acquisitions, strategic partnerships, joint ventures or capital commitments; |
| |
• | introduction of technologies or product enhancements that reduce the need for flywheel energy storage or modular infrastructure products; |
| |
• | our loss of one or more key OEM customers or channel partners; |
| |
• | an inability to expand our distribution channels successfully; |
| |
• | departures of key personnel; |
| |
• | our ability to obtain additional equity capital or borrowings under our credit agreement; |
| |
• | the outcome of our pending SEC investigation; and |
| |
• | changing external capital market conditions. |
If the market for technology stocks or the stock market in general experiences loss of investor confidence, the trading price of our common stock could decline for reasons unrelated to our business, operating results, or financial condition. The trading price of our common stock might also decline in reaction to events that affect other companies in our industry or the stock market generally even if these events do not directly affect us. Each of these factors, among others, could cause our stock price to decline.
We have not in the past and do not currently intend to pay cash dividends on our common stock.
We have never declared or paid any cash dividends on our common stock, and we do not expect to declare or pay any cash dividends on our common stock in the foreseeable future. Future cash dividends, if any, will be determined by our Board of Directors, in its discretion, based upon our earnings, financial condition, cash flow, capital resources, capital requirements, charter restrictions, contractual restrictions including those under our bank credit facility, and such other factors as our Board of Directors deems relevant.
| |
ITEM 1B. | Unresolved Staff Comments. |
None.
Our corporate headquarters facility is a 127,000 square foot building we lease in Austin, Texas. We lease this building pursuant to a lease agreement that expires in December 2021. Our manufacturing, administrative, information systems, sales and service groups currently utilize this facility.
Our engineering facility of approximately 12,150 square feet is also located in Austin, Texas and is leased pursuant to a lease agreement that expires in December 2021.
In addition to these properties, we lease facilities totaling 12,979 square feet in the United Kingdom, Germany and China for sales and service activities.
Our current manufacturing and test facilities located at our corporate headquarters can support a business volume significantly in excess of our current revenues primarily with the addition of direct labor only and no need for additional significant capital investment. We believe our existing facilities are adequate to meet our current needs and plans.
| |
ITEM 3. | Legal Proceedings. |
Refer to Footnote 7, “Contingencies,” of the consolidated financial statements on page 60 of this Form 10-K.
| |
ITEM 4. | Mine Safety Disclosures. |
Not applicable.
PART II.
| |
ITEM 5. | Market for Registrant’s Common Equity, Related Stockholder Matters and Issuer Purchases of Equity Securities. |
Our common stock is traded on The NASDAQ Stock Market LLC under the symbol “ACPW.” The following table lists the high and low per share sales prices for our common stock as reported by The NASDAQ Stock Market LLC for the periods indicated:
|
| | | | | | | |
| High | | Low |
2015 | | | |
Fourth Quarter | $ | 1.74 |
| | $ | 1.16 |
|
Third Quarter | $ | 2.12 |
| | $ | 1.59 |
|
Second Quarter | $ | 2.48 |
| | $ | 1.94 |
|
First Quarter | $ | 2.60 |
| | $ | 1.72 |
|
| | | |
2014 | |
| | |
|
Fourth Quarter | $ | 2.00 |
| | $ | 1.63 |
|
Third Quarter | $ | 2.79 |
| | $ | 1.88 |
|
Second Quarter | $ | 3.40 |
| | $ | 2.63 |
|
First Quarter | $ | 3.67 |
| | $ | 3.15 |
|
As of February 16, 2016, there were 23,109,207 shares of our common stock outstanding held by 120 stockholders of record.
We have never declared or paid cash dividends on our capital stock. We currently intend to retain any earnings for use in our business and do not anticipate paying any cash dividends in the foreseeable future. Future dividends, if any, will be determined by our board of directors.
We did not repurchase any of our securities during 2015.
Please refer to "Item 12 - Security Ownership of Certain Beneficial Owners and Management and Related Stockholder Matters" in this Form 10-K for the information required by Item 201(d) of Regulation S-K with respect to securities authorized for issuance under our equity compensation plans at December 31, 2015.
Sale of Unregistered Securities
None.
| |
ITEM 6. | Selected Financial Data. |
The following tables include selected consolidated financial data for each of our last five fiscal years. The consolidated statement of operations data for the years ended December 31, 2015, 2014, and 2013 and consolidated balance sheet data at December 31, 2015 and 2014 have been derived from the audited consolidated financial statements appearing elsewhere in this Form 10-K. The consolidated statement of operations data for the years ended December 31, 2012 and 2011 and the consolidated balance sheet data at December 31, 2013, 2012 and 2011, have been derived from audited consolidated financial statements not appearing in this document. This data should be read in conjunction with the consolidated financial statements and notes thereto, with “Management’s Discussion and Analysis of Financial Condition and Results of Operations” in Item 7 and with the other financial data set forth elsewhere in this Form 10-K. Our historical results of operations are not necessarily indicative of results of operations to be expected for future periods.
|
| | | | | | | | | | | | | | | | | | | |
Consolidated Statement of Operations Data | | | | | | | | | |
In thousands except per share data | Year Ended December 31, |
| 2015 | | 2014 | | 2013 | | 2012 | | 2011 |
Total revenue | $ | 57,421 |
| | $ | 49,136 |
| | $ | 61,699 |
| | $ | 76,315 |
| | $ | 75,482 |
|
Total cost of goods sold | $ | 40,604 |
| | $ | 36,484 |
| | $ | 42,303 |
| | $ | 51,601 |
| | $ | 57,581 |
|
Gross profit | $ | 16,817 |
| | $ | 12,652 |
| | $ | 19,396 |
| | $ | 24,714 |
| | $ | 17,901 |
|
Total operating expenses | $ | 22,877 |
| | $ | 24,672 |
| | $ | 27,013 |
| | $ | 26,440 |
| | $ | 24,781 |
|
Operating loss | $ | (6,060 | ) | | $ | (12,020 | ) | | $ | (7,617 | ) | | $ | (1,726 | ) | | $ | (6,880 | ) |
Net loss | $ | (6,459 | ) | | $ | (12,827 | ) | | $ | (8,351 | ) | | $ | (1,922 | ) | | $ | (7,094 | ) |
Basic and diluted net loss per share | $ | (0.28 | ) | | $ | (0.57 | ) | | $ | (0.43 | ) | | $ | (0.10 | ) | | $ | (0.11 | ) |
|
| | | | | | | | | | | | | | | | | | | |
Consolidated Balance Sheet Data | |
| | |
| | |
| | |
| | |
|
In thousands | Year Ended December 31, |
| 2015 | | 2014 | | 2013 | | 2012 | | 2011 |
Cash and investments | $ | 12,260 |
| | $ | 14,824 |
| | $ | 12,261 |
| | $ | 13,524 |
| | $ | 10,746 |
|
Working capital | $ | 11,946 |
| | $ | 17,247 |
| | $ | 17,696 |
| | $ | 23,945 |
| | $ | 13,753 |
|
Total assets | $ | 30,595 |
| | $ | 36,098 |
| | $ | 37,907 |
| | $ | 45,799 |
| | $ | 35,027 |
|
Long-term obligations | $ | 583 |
| | $ | 821 |
| | $ | 741 |
| | $ | 713 |
| | $ | 726 |
|
Total stockholders' equity | $ | 13,555 |
| | $ | 18,793 |
| | $ | 20,306 |
| | $ | 25,999 |
| | $ | 16,292 |
|
| |
ITEM 7. | Management’s Discussion and Analysis of Financial Condition and Results of Operations. |
The following discussion should be read in conjunction with the financial statements and related notes appearing elsewhere in this Form 10-K. This report contains forward-looking statements within the meaning of Section 27A of the Securities Act and Section 21E of the Exchange Act, that involve risks and uncertainties. Our expectations with respect to future results of operations that may be embodied in oral and written forward-looking statements, including any forward looking statements that may be included in this report, are subject to risks and uncertainties that must be considered when evaluating the likelihood of our realization of such expectations. Our actual results could differ materially. The words “believe,” “expect,” “intend,” “plan,” “project,” “will” and similar phrases as they relate to us are intended to identify forward-looking statements. For further discussion regarding forward-looking statements, please see “Special Note Regarding Forward-Looking Statements.” In addition, please see the risk factors section above for a discussion of items that may affect our future results.
Management’s Discussion and Analysis (“MD&A”) of Financial Condition and Results of Operations is designed to provide readers with narrative from the perspective of our management on our financial condition, results of operations, liquidity, and certain other factors that may impact our future results. Our MD&A is presented in the following sections:
| |
• | Critical Accounting Policies and Estimates |
| |
• | Liquidity and Capital Resources |
| |
• | Off-Balance Sheet Arrangements |
| |
• | New Accounting Pronouncements |
2015 Highlights
Our total revenue in 2015 was $57.4 million, an increase of $8.3 million or 17% from 2014. Product revenue in 2015 was $43.2 million, an increase of $7.0 million or 19% from 2014. Service revenue in 2015 was $14.2 million, an increase of $1.2 million or 10% from 2014.
The change we made to the business in early 2014 primarily to our sales organization and go-to market approach coupled with a continued focus on increasing bookings and backlog, improving operational efficiencies, and controlling costs yielded steady progress in 2015. A number of achievements from 2015 are highlighted below.
| |
• | Increased backlog by 15% or $4.1 million to $30.8 million at December 2015, compared to $26.7 million at December 31, 2014 |
| |
• | Reduced net inventory by 6% or $0.4 million since December 2014, through December 31, 2015 and improved inventory turns to 6.1 in 2015 versus 3.9 in 2014 |
| |
• | Lowered operating expenses by 7% or $1.8 million in 2015 versus 2014 with expenses down seven of last nine quarters. Excluding the management incentive plan our operating expenses would have been lowered by $3.0 million or 12% versus 2014 |
| |
• | Won a large, multimillion dollar deal from one of our strategic IT partners for our new modular product, a cost reduced alternative to enable us and our IT partners in selling modular data center and infrastructure enclosures |
| |
• | Introduced Extended Runtime option on CleanSource HD UPS that can provide customers up to 30 minutes of additional UPS runtime. A secondary energy storage system, such as batteries or additional flywheel modules, supplements the primary flywheel and is available to those customers that require longer UPS autonomy |
| |
• | Increased number of non-data center projects entering our opportunities pipeline as a result of renewed focus on non-IT applications including healthcare and industrial to diversify revenue stream |
| |
• | Settled stockholder class action complaint and derivative actions in May 2015 with total settlement amounts and related expenses paid from insurance proceeds |
UPS sales increased $3.0 million or 11% compared to 2014, making up 72% of total product revenue versus 78% in 2014. MIS sales increased $4.1 million or 50% compared to 2014, making up 28% of total product revenue.
Service sales increased $1.2 million or 10% in 2015 compared to 2014. This increase is primarily attributable to higher sales of spare parts compared to 2014.
Our gross profit was 29% of revenue for fiscal 2015 compared to 26% in fiscal 2014. This margin increase is related to improvements in manufacturing absorption on increased revenue and production in 2015.
Net loss was $6.5 million in 2015 compared to $12.8 million in 2014. The decrease in net loss from 2014 to 2015 was due to an increase in revenue and gross margin and lower operating expenses.
Cash and cash equivalents totaled $12.3 million at December 31, 2015, compared to $14.8 million at December 31, 2014. Management believes this available cash balance, combined with cash we anticipate to generate from operations and the credit facility we have in place, will be sufficient to fund our operations as we work to increase sales volume and scale the business. In March 2014, we raised additional funds through a public offering to provide additional funds for our future anticipated working capital needs. See Note 3 to the consolidated financial statements of this Form 10-K for more information.
2016 Plan
Our priorities remain unchanged in 2016 as we continue to focus on increasing bookings and backlog, improving operational efficiencies, and controlling costs. Our efforts to grow the business will be supported through continued expansion of our sales distribution network worldwide; diversifying our revenue stream through pursuing health care and industrial applications where our UPS and MIS products are uniquely suited; and reinforcing our value proposition with customers. We will also look for ways to strengthen our operating base and lower our overall cost structure.
Our sales cycles have been extending which we believe is a function of a number of variables including delays in customers’ deployment schedules related to persistent sluggishness in the economy. We have seen delays in orders being awarded and schedule changes to defer deliveries. We remain vigilant in our expense management initiatives in light of these market conditions.
A number of risks and challenges face our business going forward.
| |
• | We have a history of operating losses and have not yet reached operating profitability on an annual basis. We believe the success of our UPS and MIS products and our service offerings combined with our focus on direct sales to customers and a lower overall operating cost base, will help us to further increase our revenues and reduce our level of operating losses. Consequently, we willcontinue to focus on our operating costs and cash and working capital management in 2016 to maintain sufficient funds for our operating activities. |
| |
• | The higher sales price of our CleanSource PowerHouse and modular IT infrastructure orders can cause large quarterly fluctuations in our inventory, receivables and payables balances, depending on the number of such orders in progress at any point in time. This can cause material fluctuations in the level of working capital we require. If the number of such orders increases rapidly or any of these orders have payment terms that are less favorable, we will need access to more working capital to fund the growth of our business and to fulfill these orders. We extended our bank credit facility in 2014 to help fund our growth and manage our working capital requirements. |
| |
• | Our sales cycle is such that we generally have some visibility in advance for future orders. However, a sudden change in business volume or product mix, positive or negative, from any of our business or channel partners or in our direct business can significantly impact our expected revenues and impact our ability to quickly respond to opportunities. The continued slow global economic growth has reduced our confidence in the ability to predict future revenues, and even with improving economic conditions, there is still uncertainty and risk in our forecasting. Our limited window of sales visibility does provide us with some opportunity to adjust expenditures or take other measures to reduce our cash consumption if we can see and anticipate a shortfall in revenue. This window may also give us time to identify additional sources of funding if we anticipate an increase in our working capital requirements due to increased revenues or changes in our revenue mix. A significant increase in sales, especially in our MIS business, would likely increase our working capital requirements due to the longer production time and cash cycle of sales of these products. |
| |
• | Foreign currency volatility could make it more challenging for us to sell outside of the US. As foreign currencies strengthen against the dollar, our pricing may not be as competitive in certain geographies. |
Results of Operations
Below are our revenues and costs and expenses for fiscal 2015, 2014, and 2013. This information should be read in conjunction with our Consolidated Financial Statements and notes thereto.
|
| | | | | | | | | | | | | | | | | | | | | | | | | | | | | |
| Year Ended December 31, | | Year Ended December 31, |
($ in thousands) | 2015 | | 2014 | | $ change | | % change | | 2014 | | 2013 | | $ change | | % change |
Product revenue | $ | 43,247 |
| | $ | 36,211 |
| | $ | 7,036 |
|
| 19 | % | | $ | 36,211 |
|
| $ | 44,158 |
|
| $ | (7,947 | ) |
| (18 | )% |
Service and other revenue | 14,174 |
| | 12,925 |
| | 1,249 |
|
| 10 | % | | 12,925 |
|
| 17,541 |
|
| (4,616 | ) |
| (26 | )% |
Total revenue | 57,421 |
| | 49,136 |
| | 8,285 |
|
| 17 | % | | 49,136 |
|
| 61,699 |
|
| (12,563 | ) |
| (20 | )% |
Cost of product revenue | 32,017 |
| | 29,182 |
| | 2,835 |
|
| 10 | % | | 29,182 |
|
| 32,825 |
|
| (3,643 | ) |
| (11 | )% |
Cost of service and other revenue | 8,587 |
| | 7,302 |
| | 1,285 |
|
| 18 | % | | 7,302 |
|
| 9,478 |
|
| (2,176 | ) |
| (23 | )% |
Total cost of goods sold | 40,604 |
| | 36,484 |
| | 4,120 |
|
| 11 | % | | 36,484 |
|
| 42,303 |
|
| (5,819 | ) |
| (14 | )% |
Gross profit | 16,817 |
| | 12,652 |
| | 4,165 |
|
| 33 | % | | 12,652 |
|
| 19,396 |
|
| (6,744 | ) |
| (35 | )% |
Operating expenses: |
|
| |
|
| |
|
|
| |
|
|
|
|
|
|
|
Research and development | 5,723 |
| | 6,689 |
| | (966 | ) |
| (14 | )% | | 6,689 |
|
| 7,430 |
|
| (741 | ) |
| (10 | )% |
Selling and marketing | 10,589 |
| | 11,940 |
| | (1,351 | ) |
| (11 | )% | | 11,940 |
|
| 12,032 |
|
| (92 | ) |
| (1 | )% |
General and administrative | 6,565 |
| | 6,043 |
| | 522 |
|
| 9 | % | | 6,043 |
|
| 7,551 |
|
| (1,508 | ) |
| (20 | )% |
Total operating expenses | 22,877 |
| | 24,672 |
| | (1,795 | ) |
| (7 | )% | | 24,672 |
|
| 27,013 |
|
| (2,341 | ) |
| (9 | )% |
Loss from Operations | (6,060 | ) | | (12,020 | ) | | 5,960 |
|
| 50 | % | | (12,020 | ) |
| (7,617 | ) |
| (4,403 | ) |
| (58 | )% |
Interest expense, net | (375 | ) | | (395 | ) | | 20 |
|
| 5 | % | | (395 | ) |
| (370 | ) |
| (25 | ) |
| (7 | )% |
Other income (expense), net | (24 | ) | | (160 | ) | | 136 |
|
| 85 | % | | (160 | ) |
| (364 | ) |
| 204 |
|
| 56 | % |
Loss before income taxes | (6,459 | ) | | (12,575 | ) | | 6,116 |
|
| 49 | % | | (12,575 | ) |
| (8,351 | ) |
| (4,224 | ) |
| (51 | )% |
Income tax expense | — |
| | (252 | ) | | 252 |
|
| 100 | % | | (252 | ) |
| — |
|
| (252 | ) |
| 100 | % |
Net Loss | $ | (6,459 | ) | | $ | (12,827 | ) | | $ | 6,368 |
|
| 50 | % | | $ | (12,827 | ) |
| $ | (8,351 | ) |
| $ | (4,476 | ) |
| (54 | )% |
Fiscal 2015 Compared to Fiscal 2014
Product Revenue. Our product revenue was derived from the following sources:
|
| | | | | | | | | | | | | | | | | | | | | | | | | | | | | |
| Year Ended December 31, | | Year Ended December 31, |
($ in thousands) | 2015 | | 2014 | | $ change | | % change | | 2014 | | 2013 | | $ change | | % change |
Product revenue: | | | | | | | | | | | | | | | |
UPS product revenue | $ | 31,046 |
| | $ | 28,064 |
| | $ | 2,982 |
| | 11 | % | | $ | 28,064 |
| | $ | 22,620 |
| | $ | 5,444 |
| | 24 | % |
Modular Infrastructure Solutions | 12,201 |
| | 8,147 |
| | 4,054 |
| | 50 | % | | 8,147 |
| | 21,538 |
| | (13,391 | ) | | (62 | )% |
Total product revenue | $ | 43,247 |
| | $ | 36,211 |
| | $ | 7,036 |
| | 19 | % | | $ | 36,211 |
| | $ | 44,158 |
| | $ | (7,947 | ) | | (18 | )% |
Total product revenue for fiscal 2015 was $43.2 million, compared to $36.2 million in fiscal 2014, a $7.0 million increase. The increase in our product revenue in 2015 compared to 2014 came from higher sales primarily by the increase in MIS business that was driven by a large order from our IT channel partner, which fluctuates depending on their success and needs for modular infrastructure solutions. In 2015, 72% of our product revenue came from the sale of UPS systems and 28% from the sale of MIS products. Sales of our UPS products increased by approximately $3.0 million, or 11%, compared to 2014 as we saw an increase in our OEM channel sales.
Product revenue from our OEM channel for fiscal 2015 was $11.2 million, compared to $7.8 million in 2014, a $3.5 million increase or 45%. The size and volume of orders from our OEM channel can fluctuate significantly on a quarterly basis, and we continue to see a small number of large transactions from our OEM channel. Sales to Caterpillar, our primary OEM customer,
represented 25% of our total revenue for fiscal 2015 compared to 18% in fiscal 2014. We have supported our OEM partners’ efforts to sell total solutions to their customers that include generators and switchgear that they manufacture along with our UPS products as a total solution.
Product revenue from our IT channel partner for fiscal 2015 were $10.2 million, compared to $2.1 million in 2014, an increase of $8.1 million or 386%. This increase reflects larger orders of our MIS products during 2015 from our IT channel partner Hewlett Packard Enterprise ("HPE"). The level of orders may continue to fluctuate depending on our partner’s success and need for modular infrastructure solutions. Total sales to HPE represented 18% and 1% of our total revenue for fiscal 2015 and fiscal 2014.
Product revenue in North and South America ("Americas") was $32.1 million, an increase of $10.7 million or 50%, compared to $21.3 million for 2014. Our revenue in the Americas increased in 2015 compared to 2014, primarily as a result of higher MIS revenues and the increase in sales from our OEM channels, which historically have largely originated in the North American market.
Product revenue in Europe, the Middle East, and Africa (“EMEA”) decreased by approximately $2.2 million, or 19% to $9.5 million in fiscal 2015 compared to $11.7 million in fiscal 2014. This decrease is due to lower direct UPS sales.
Our product revenue in the Asia Pacific region (“APAC”) decreased by 48%, or $1.5 million in 2015 to $1.6 million compared to $3.1 million in 2014. This decrease is primarily due to lower UPS sales in the region.
We did not have any revenues greater than 10% concentrated in a single country outside of the United States in 2015 or 2014.
Service and other revenue. Service and other revenue increased by approximately $1.2 million, or 10%, to $14.2 million in fiscal 2015, compared to $12.9 million in fiscal 2014. These increases primarily reflect higher sales of spare parts.
Cost of product revenue. The cost of product revenue as a percentage of total product revenue was 74% and 81% in 2015 and 2014, respectively The decrease in costs as a percentage of revenue reflects higher MIS sales with better margin along with continued improvements in manufacturing absorption associated with increased production from the prior year, offset by lower margin UPS sales related to supply chain commitments we made more than two years ago to support our CleanSource HD UPS products at prices higher than we expect in the future. We expect to fully absorb these costs in the first half of fiscal 2016 resulting in improved margins. During 2015 and 2014, we operated a manufacturing facility that has a manufacturing and testing capacity significantly greater than required by our current product revenue levels. Our manufacturing operational costs include a large portion of fixed costs relative to our operational needs. We incurred approximately $5.9 million and $5.8 million, in 2015 and 2014, respectively, in fixed costs related to our manufacturing facility. We expense the excess costs of the underutilization of this facility as part of our cost of product revenues.
Cost of service and other revenue. The cost of service and other revenue as a percentage of total service and other revenue increased by 5%, to 61% in 2015 compared to 56% in 2014. The increase in costs as a percentage of revenue reflects higher unabsorbed costs and training costs for new employees during fiscal 2015. A large portion of the costs involved in operating our service organization are fixed in nature and we incurred approximately $3.2 million and $2.3 million in unabsorbed overhead costs in fiscal 2015 and 2014, respectively. The utilization of our service personnel will be affected by the number of products implemented in a particular period. When we have a lower number of installation projects we would expect our costs as a percentage of revenue to increase due to lower employee utilization.
Gross profit. Our gross profit was 29% of revenue for fiscal 2015 compared to 26% in fiscal 2014. This margin increase was related to higher MIS margins as we continue to improve manufacturing absorption from fiscal 2014. Our gross margins fluctuate on a quarterly basis depending on changes in the product and geographic mix of our revenues and were as high as 33% during the first quarter of 2015 and as low as 25% in the fourth quarter of 2015.
Research and development. Research and development expenses were approximately $5.7 million, $1.0 million or 14%, lower in fiscal 2015 compared to $6.7 million in fiscal 2014. The decrease was primarily due to lower payroll expense and employee benefits of $0.6 million and reduced fees from external parties of $0.4 million related to prototype and testing expenses which were incurred in fiscal 2014.
Selling and marketing. Selling and marketing costs were approximately $10.6 million, $1.4 million or 11% lower in fiscal 2015, compared to $11.9 million for the same period of 2014. The decrease was primarily due to lower payroll expense including sales commissions of $1.3 million in 2015 compared to 2014.
General and administrative. General and administrative expenses were approximately $6.6 million, $0.5 million or 9%, higher in fiscal 2015 compared to $6.0 million in 2014. The increases were primarily due to increases in bonus expense of $0.7 million and an increase is stock compensation expense of $0.4 million offset by a decrease of $0.4 million of legal fees.
Interest expense, net. Net interest expense remained flat at $0.4 million in fiscal 2015 compared to $0.4 million in 2014. The interest expense incurred during 2015 and 2014 was in connection with the outstanding balance on our revolving credit facility.
Other income (expense), net. Other income (expense), net was $24,000 in fiscal 2015 and $0.2 million in fiscal 2014, a $0.1 million decrease or 85%. This decrease primarily reflects foreign exchange losses or gains on settlement of intercompany balances and sales contracts held in foreign currencies.
Income tax expense. Our income tax expense for 2015 was $0 with an effective tax rate of 0%, compared to approximately $0.3 million with an effective tax rate of 2% for 2014. The decrease in the effective tax rate for fiscal 2015 was primarily due to settlement under tax examination by the German tax authorities from fiscal 2014. In September 2014, we settled a tax examination of our German subsidiary for years 2007 through 2011. In the settlement, we agreed to transfer pricing adjustments for the period under examination resulting in a reduction of loss carryovers and a deemed distribution subject to withholding taxes under German law. We recorded a provision for income taxes of $0.3 million in the quarter ended September 30, 2014 related to settlement of the German tax examination.
As a result of the examination, the Company also adjusted net operating losses in jurisdictions impacted by the transfer pricing adjustments to account for appropriate intercompany pricing for years prior to 2014. There was no overall tax impact as the net operating loss deferred tax assets are fully offset by a valuation allowance. Both the settlement and the adjustments to the net operating losses are reflected in the Company’s rate reconciliation of the income tax footnote.
Fiscal 2014 Compared to Fiscal 2013
Total revenues in fiscal 2014 were $49.1 million, compared to $61.7 million in fiscal 2013, a $12.6 million, or 20% decrease. The decrease in revenue was primarily attributed to our MIS products.
Total product revenue for fiscal 2014 was $36.2 million, compared to $44.2 million in fiscal 2013, a $8.0 million decrease. The decrease in our product revenue in 2014 compared to 2013 came from lower sales from our MIS products primarily related to HPE, which fluctuates depending on their success and needs for modular infrastructure solutions, partially offset by an increase in our UPS sales. In 2014, 78% of our product revenue came from the sale of UPS systems and 22% from the sale of MIS products. Sales of our UPS products increased by approximately $5.4 million, or 24%, compared to 2013 as we saw an increase in our direct sales to our customers.
Product revenue from our OEM channel for fiscal 2014 was $7.8 million, compared to $7.2 million in 2013, a $0.6 million increase or 7%. This reflects increased performance from our OEM partners, primarily in the U.S. market. Sales to Caterpillar, our primary OEM customer, represented 18% of our total revenue for fiscal 2014 compared to 14% in fiscal 2013.
Product revenue from our IT channel partners for fiscal 2014 was $2.1 million, compared to $11.1 million in 2013, a decrease of $9.0 million or 81%. This reduction reflects decreased demand for our MIS products during 2014 from our IT channel partner, HPE. The level of orders may continue to fluctuate depending on our partner’s success and need for infrastructure solutions.
Product revenue in the Americas was $21.3 million, or 59% of our total product revenue for 2014, a decrease of $15.1 million or 41%, compared to $36.4, or 82%, for 2013. Our revenue in the Americas decreased in 2014 compared to 2013, primarily as a result of lower MIS revenue associated with large projects in 2013 which were not repeated.
Product sales to customers in EMEA increased by approximately $7.7 million, or 195%, to $11.7 million in fiscal 2014 compared to $4.0 million in fiscal 2013. This increase relates primarily to two large UPS orders, one approximately $3.3 million and another approximately $1.2 million which were recognized in fiscal 2013.
Our product sales in APAC decreased by 18%, or $0.7 million, in 2014 to $3.1 million compared to $3.8 million in 2013. This decrease is primarily due to reduced UPS sales in China.
We did not have any revenues greater than 10% concentrated in a single country outside of the United States in 2014 or 2013.
Service and other revenue. Service and other revenue decreased by approximately $4.5 million, or 26%, to $13.0 million in fiscal 2014, compared to $17.5 million in fiscal 2013. The decrease primarily reflects reduced service revenue and professional fees stemming from lower MIS product demand in 2014.
Cost of product revenue. The cost of product revenue as a percentage of total product revenue was 81% and 74% in 2014 and 2013, respectively. During 2014 and 2013, we operated a manufacturing facility that has a manufacturing and testing capacity significantly greater than required by our current product revenue levels. Our manufacturing facility is comprised of a large portion of our fixed costs. We incurred approximately $5.8 million and $6.9 million, in 2014 and 2013, respectively, in fixed costs for our manufacturing facility. Our manufacturing capacity is in excess of our current business requirements. We expense the excess costs of the underutilization of this facility as part of our cost of product revenues.
Cost of service and other revenue. The cost of service and other revenue as a percentage of total service and other revenue increased by 2%, to 56% in 2014 compared to 54% in 2013. A large portion of the costs involved in operating our service organization are fixed in nature and we incurred approximately $2.3 million and $3.0 million in unabsorbed overhead costs in fiscal 2014 and 2013, respectively. The utilization of our service personnel will be affected by the number of MIS products implemented in a particular period. When we have a lower number of installation projects we would expect our costs as a percentage of revenue to increase due to lower employee utilization
Gross profit. Our gross profit was 26% of revenue for fiscal 2014 compared to 31% in fiscal 2013. The decrease in gross profit margin in 2014 compared to 2013 is related to under absorption of fixed overhead costs in manufacturing and service due to the lower revenue and manufacturing production in 2014. Our gross margins fluctuate on a quarterly basis depending on changes in the product and geographic mix of our revenues and were as high as 30% during the third quarter of 2014 and as low as 19% in the second quarter of 2014.
Research and development. Research and development expenses were approximately $6.7 million, $0.7 million or 10%, lower in fiscal 2014 compared to $7.4 million in fiscal 2013. The decrease was primarily due to reduced costs for development activities on our next generation of UPS products.
Selling and marketing. Selling and marketing costs were approximately $11.9 million in fiscal 2014, compared to $12.0 million for the same period in 2013. The decrease was primarily due to severance expense to former executives in 2013 offset by payroll expense increase in 2014.
General and administrative. General and administrative expenses were approximately $6.0 million, $1.5 million or 20%, lower in fiscal 2014 compared to $7.6 million in 2013. This decrease was primarily due to reductions in (i) relocation and temporary living costs for executives of $0.4 million; (ii) severance payments to former executives of $0.3 million, and (iii) legal fees of $0.3 million from 2013.
Interest expense, net. Net interest expense was relatively flat in fiscal 2014 compared to 2013. The interest expense incurred during 2014 and 2013 was in connection with the outstanding balance on our revolving credit facility.
Other income (expense), net. Other income (expense), net was $0.2 million in fiscal 2014 compared to income of $0.4 million in 2013, a $0.2 million decrease or 56%. This decrease primarily reflects foreign exchange losses or gains on settlement of intercompany balances and sales contracts held in foreign currencies.
Income tax expense. Our income tax expense for 2014 was approximately $0.3 million with an effective tax rate of 2%, compared to $0 for 2013. The increase in the effective tax rate for fiscal 2014 was primarily due to settlement under tax examination by the German tax authorities. In September 2014, we settled a tax examination of our German subsidiary for years 2007 through 2011. In the settlement, we agreed to transfer pricing adjustments for the period under examination resulting in a reduction of loss carryovers and a deemed distribution subject to withholding taxes under German law. We recorded a provision for income taxes of $0.3 million in the quarter ended September 30, 2014 related to settlement of the German tax examination.
As a result of the examination, the Company also adjusted net operating losses in jurisdictions impacted by the transfer pricing adjustments to account for appropriate intercompany pricing for years prior to 2014. There was no overall tax impact as the net operating loss deferred tax assets are fully offset by a valuation allowance. Both the settlement and the adjustments to the net operating losses are reflected in the Company’s rate reconciliation of the income tax footnote.
Critical Accounting Policies and Estimates
We consider an accounting policy to be critical if:
| |
• | the accounting estimate requires us to make assumptions about matters that are highly uncertain or require the use of judgment at the time we make that estimate; and |
| |
• | changes in the estimate that are reasonably likely to occur from period to period, or use of different estimates that we could have reasonably used instead in the current period, would have a material impact on our financial condition or results of operations. |
Management has reviewed the development and selection of these critical accounting estimates with the Audit Committee of our Board of Directors. In addition, there are other items within our financial statements that require estimation, but are not deemed critical as defined above. Changes in these and other items could still have a material impact upon our financial statements.
Revenue recognition
We recognize revenue when four criteria are met: (i) persuasive evidence that an arrangement exists; (ii) delivery has occurred or services have been rendered; (iii) the sales price is fixed or determinable; and (iv) collectability is reasonably assured. In general, revenue is recognized when revenue-generating transactions fall into one of the following categories of revenue recognition:
| |
• | We recognize product revenue at the time of shipment for a significant portion of all products sold directly to customers and through distributors because title and risk of loss typically pass on delivery to the common carrier. Our customers and distributors do not have the right to return products. We may enter into bill-and-hold arrangements and when this occurs delivery may not be present, but other criteria are reviewed to determine proper timing of revenue recognition. |
| |
• | Unless performed under a maintenance agreement, we recognize installation, service and maintenance revenue at the time the service is performed. |
| |
• | We recognize revenue associated with maintenance agreements over the life of the contracts using the straight-line method, which approximates the expected timing in which applicable services are performed. Amounts collected in advance of revenue recognition are recorded as a current liability in the deferred revenue line of the consolidated balance sheet or long-term liability based on the time from the balance sheet date to the future date of revenue recognition. |
| |
• | We recognize revenue on certain rental programs over the life of the rental agreements using the straight-line method. Amounts collected in advance of revenue recognition are recorded as a current or long-term liability based on the time from the balance sheet date to the future date of revenue recognition. |
| |
• | Shipping costs reimbursed by the customer are included in revenue. |
Multiple element arrangements (“MEAs”) are arrangements to sell products to customers that frequently include multiple deliverables. Our most significant MEAs include the sale of one or more of our CleanSource® UPS or CleanSource PowerHouse products, combined with one or more of the following products or services: design services, project management, commissioning and installation services, spare parts or consumables, and maintenance agreements. Delivery of the various products or performance of services within the arrangement may or may not coincide. Certain services related to design and consulting may occur prior to product delivery. Commissioning and installation typically take place within six months of product delivery, depending upon customer requirements. Maintenance agreements, consumables, and repair, maintenance or consulting services generally are delivered over a period of one to five years.
When arrangements include multiple elements, we allocate revenue to each element based on the relative selling price and recognize revenue when the elements have standalone value and the four criteria for revenue recognition have been met. We establish the selling price of each element based on Vendor Specific Objective Evidence (“VSOE”) if available, Third Party Evidence (“TPE”) if VSOE is not available, or Best Estimate of Selling Price (“BESP”) if neither VSOE nor TPE is available. We generally determine selling price based on amounts charged separately for the delivered and undelivered elements to similar customers in standalone sales of the specific elements. When arrangements include a maintenance agreement, we recognize revenue related to the maintenance agreement at the relative selling price on a straight-line basis over the life of the agreement.
Any taxes imposed by governmental authorities on our revenue-producing transactions with customers are shown in our consolidated statement of operations on a net-basis; that is, excluded from our reported revenues.
Inventories
Inventories are priced at the lower of cost (using the first-in, first-out method) or market. We estimate inventory reserves on a quarterly basis and record reserves for obsolescence or slow-moving inventory based on assumptions about future demand
and marketability of products, the impact of new product introductions, inventory turns and specific identification of items, such as product discontinuance, damaged goods or engineering/material changes.
Warranty liability
Estimated warranty liability costs are accrued for each of our products at the time of sale. Our estimates are principally based on assumptions regarding the lifetime warranty costs of each product, including where little or no claims experience may exist. Due to the uncertainty and potential volatility of these estimates, changes in our assumptions could have a material effect on our reported operating results. Our estimate of warranty liability is reevaluated on a quarterly basis. Experience has shown that initial data for a new product can be very volatile due to factors such as product and component failure rates, material usage and service delivery costs in correcting product failures; therefore our process relies upon long-term historical averages until actual data is available. As actual experience becomes available, it is used to modify the historical averages to ensure that the forecast is within the range of likely outcomes. The resulting balances are then compared to current spending rates to help ensure that the accruals are adequate to meet expected future obligations.
Stock-based compensation
Stock-based compensation cost is estimated at the grant date based on the fair value of the award and is recognized as an expense ratably over the requisite service period of the award. Determining the appropriate fair-value model and calculating the fair value of stock-based awards at the grant date requires considerable judgment, including estimating stock price volatility, expected option life and forfeiture rates. We develop our estimates based on historical data and market information that can change significantly over time. A small change in estimates used can have a relatively large impact on the estimated valuation.
We use the Black-Scholes option valuation model to value employee stock awards. We estimate stock price volatility based upon our historical volatility. Estimated option life and forfeiture rate assumptions are derived from historical data.
Liquidity and Capital Resources
Our primary sources of liquidity at December 31, 2015 are our cash and cash equivalents, our bank credit facilities and projected cash flows from operating activities. If we meet our cash flow projections, we expect that we will have adequate capital resources to continue operating our business for at least the next twelve months. Our projections and our assumptions around the adequacy of our liquidity are based on estimates regarding expected revenues and future costs. However, there are scenarios in which our revenues may not meet our projections, our costs may exceed our estimates or our working capital or capital expenditure needs may be greater than anticipated. Further, our estimates may change and future events or developments may also affect our estimates. Any of these factors may change our expectation of cash usage in 2016 and beyond or significantly affect our level of liquidity.
Our Second Amended and Restated Loan and Security Agreement dated August 5, 2010 (as amended on March 5, 2012, August 15, 2012, and July 28, 2014, the “Loan Agreement”) with Silicon Valley Bank (“SVB”) gives us flexibility to help fund our business operations and manage our working capital requirements. For additional information related to the Loan Agreement, please refer to Footnote 4, “Revolving Credit Facility,” of the consolidated financial statements on pages 56 to 57 of this Form 10-K.
In March 2014, we sold approximately 3.7 million shares of common stock at a purchase price of $3.15 per share, for proceeds, net of fees and expenses, of approximately $10.4 million, in a public underwritten offering made under a shelf registration statement that we had filed with the SEC and that had been declared effective in June 2013. The proceeds from this offering were used by us to help fund our working capital requirements and for general corporate purposes.
Should additional funding be required or desirable, we would expect to raise the required funds through borrowings or public or private sales of debt or equity securities. If we raise additional funds through the issuance of convertible debt or equity securities, the ownership of our existing stockholders could be significantly diluted. If we obtain additional debt financing, a substantial portion of our operating cash flow may be dedicated to the payment of principal and interest on such indebtedness, and the terms of the debt securities issued could impose significant restrictions on our operations. We do not know whether we will be able to secure additional funding, or funding on terms acceptable to us, to continue our operations as planned. If financing is not available, we may be required to reduce, delay or eliminate certain activities or to license or sell to others some of our proprietary technology.
Significant uses of cash
Operating Activities
The following table summarizes the yearly changes in cash used in operating activities (in thousands):
|
| | | | | | | | | | | |
Year | | Annual Amount | | Change from Prior Year | | Percent Change |
2015 | | $ | (1,611 | ) | | $ | 5,617 |
| | 78 | % |
2014 | | $ | (7,228 | ) | | $ | (5,921 | ) | | (453 | )% |
2013 | | $ | (1,307 | ) | | $ | 4,683 |
| | 78 | % |
Cash used in operating activities was $1.6 million in 2015 compared to $7.2 million in 2014. Cash used in operating activities was primarily related to our net loss of $6.5 million partially offset by the reduction in our accounts receivable of $2.5 million and non cash stock based compensation of $1.4 million. Changes in our net working capital resulted in cash provided of $2.6 million in 2015, compared to $3.1 million in 2014. The frequent changes in our working capital can result in very large fluctuation in inventory, payables and receivables, even weekly, based on the large size of some of our orders. Our $0.3 million change in inventory also includes a non-cash charge of $0.1 million in 2015 related to items purchased as inventory but later capitalized to property and equipment as test units.
Our top five customers represented 56% of our 2015 total revenue and 63% of our total receivables at December 31, 2015. As a result of this customer concentration, our failure to collect receivables from any of these customers in a timely manner could have a significant adverse effect on our liquidity. This risk may potentially increase as we sell more modular infrastructure solutions due to their higher average selling price. We do continue to request deposits and periodic payments from large customers where commercially possible, particularly for projects with multiple deliverables. However, the amount of such advance payments can fluctuate significantly on a quarterly basis, depending on the size and scope of customer orders at any point in time. As a result, we will need to continue to focus on management of cash and working capital in 2016 to manage the level of funds we use in our operating activities.
Cash used in operating activities was $7.2 million in 2014 compared to $1.3 million in 2013. Cash used in operating activities was primarily related to our net loss of $12.8 million partially offset by the change in our inventory of $5.3 million initiated by our current management team to bring inventory levels down. Changes in our net working capital resulted in cash provided of $3.1 million in 2014, compared to cash used of $4.3 million in 2013. Our change in inventory includes a non-cash charge of $44,000 in 2014 related to items purchased as inventory for our latest generation UPS product, but later capitalized to property and equipment as test units.
Investing Activities
Investing activities primarily consist of purchases of property and equipment. The cash used in investing activities increased to $0.8 million in 2015 from $0.3 million in 2014 as we invested more in capital improvements in 2015. Capital expenditures increased in 2015 from 2014 by approximately $0.5 million. Our capital expenditures in 2015 primarily included investments in equipment to support our demonstration units, manufacturing facility, computers and software.
The cash used in investing activities decreased to $0.3 million in 2014 from $0.9 million in 2013 as we invested less in capital improvements in 2014. Capital expenditures decreased in 2014 from 2013 by approximately $0.7 million. Our capital expenditures in 2014 primarily included investments in equipment to support our manufacturing facility, computers, software, and test units of our latest generation UPS product.
Financing Activities
Funds used in financing activities during 2015 was $9,000 compared to funds provided by financing activities of $10.6 million in 2014, a $10.6 million decrease. This decrease is primarily due to the 2014 sale of approximately 3.7 million shares of our common stock at a purchase price of $3.15 per share, for proceeds, net of fees and expenses, of approximately $10.4 million, in a public underwritten offering.
Funds provided by financing activities during 2014 was $10.6 million compared to $0.6 million in 2013, a $10.0 million increase. This increase primarily includes the sale of approximately 3.7 million shares of our common stock at a purchase price of $3.15 per share, for proceeds, net of fees and expenses, of approximately $10.4 million, in a public underwritten offering. Proceeds from the exercise of employee stock options were approximately $0.1 million during 2014.
Future uses of cash
We believe that our cash and investments, projected cash flows from operations and sources of available liquidity will be sufficient to fund our operations for the next twelve months. However, a sudden change in business volume, positive or negative, from any of our business or channel partners, or in our direct business, or any customer-driven events such as order or delivery deferral, could significantly impact our expected revenues and cash needs. The continuing global economic instability and currency fluctuation has increased the already present challenge of predicting future revenues. We do have some opportunity to adjust expenditures or take other measures to reduce our cash consumption if we see and anticipate a shortfall in revenue.We can also identify additional sources of funding if we anticipate an increase in our working capital requirements due to increased revenues or changes in our revenue mix. A significant increase in sales, especially in our MIS business, would likely increase our working capital requirements, due to the longer production time and cash cycle of sales of these products.
Other factors that may affect liquidity
Our cash requirements will depend on many factors, including any sales growth, the market acceptance of our products, the gross profit we are able to generate with our sales, the timing and level of development funding, the rate of expansion of our sales and marketing activities, the rate of expansion of our manufacturing processes, and the timing and extent of research and development projects. Although we are not a party to any agreement or letter of intent with respect to a potential acquisition or merger, we may enter into acquisitions or strategic arrangements in the future to help support our growth, which could also require us to seek additional equity or debt financing. Should additional funding be required or desirable, we may need to raise the required funds through borrowings or public or private sales of debt or equity securities. If we raise additional funds through the issuance of convertible debt or equity securities, the percentage ownership of our existing stockholders could be significantly diluted. If we obtain additional debt financing, a substantial portion of our operating cash flow may be dedicated to the payment of principal and interest on such indebtedness, and the terms of the debt securities issued could impose significant restrictions on our operations. We do not know whether we will be able to secure additional funding, or funding on terms acceptable to us, to continue our operations as planned. If financing is not available, we may be required to reduce, delay or eliminate certain activities or to license or sell to others some of our proprietary technology.
In March 2014, we sold approximately 3.7 million shares of common stock at a purchase price of $3.15 per share, for proceeds, net of fees and expenses, of approximately $10.4 million, in a public underwritten offering made under a shelf registration statement that we had filed with the SEC and that had been declared effective in June 2013. The proceeds from this offering were used by us to help fund our working capital requirements and for general corporate purposes.
Off-Balance Sheet Arrangements
During the years ended December 31, 2015, 2014, and 2013, we did not have any relationships with unconsolidated entities or financial partnerships, such as entities often referred to as structured finance or special purpose entities, which would have been established for the purpose of facilitating off-balance sheet arrangements or other contractually narrow or limited purposes.
New Accounting Pronouncements
Refer to Footnote 1, “Summary of Significant Accounting Policies,” of the consolidated financial statements on pages 53 to 54 of this Form 10-K.
| |
ITEM 8. | Financial Statements and Supplementary Data. |
The Financial Statements and Selected Quarterly Financial Data required by this item are included in Part IV, Item 15(a)(1) and are presented beginning on Page 43.
| |
ITEM 9. | Changes in and Disagreements with Accountants on Accounting and Financial Disclosure. |
None.
| |
ITEM 9A. | Controls and Procedures. |
Effectiveness of Disclosure Controls and Procedures.
Our Chief Executive Officer and our Chief Financial Officer, based on the evaluation of our disclosure controls and procedures (as defined in Rule 13a-15(e) or 15d-15(e) under the Exchange Act required by paragraph (b) of Rule 13a-15 or Rule 15d-15, have concluded that, as of December 31, 2015, our disclosure controls and procedures were effective to ensure that the information we are required to disclose in reports that we file or submit under the Exchange Act (i) is recorded, processed, summarized and reported within the time periods specified in SEC rules and forms, and (ii) is accumulated and communicated to our management, including our Chief Executive Officer and our Chief Financial Officer, as appropriate to allow timely decisions regarding required disclosure.
Management’s Report on Internal Control over Financial Reporting.
Management is responsible for establishing and maintaining adequate internal control over financial reporting, as such term is defined in Exchange Act Rules 13a-15(f) and 15d-15(f). Internal control over financial reporting is a process, designed by, or under the supervision of, our Chief Executive Officer and Chief Financial Officer, and effected by our Board, management and other personnel, to provide reasonable assurance regarding the reliability of financial reporting, and the preparation of financial statements for external purposes in accordance with U.S. generally accepted accounting principles.
Internal control over financial reporting includes those policies and procedures that (1) pertain to the maintenance of records that, in reasonable detail, accurately and fairly reflect the transactions and dispositions of the assets of the company; (2) provide reasonable assurance that transactions are recorded as necessary to permit preparation of financial statements in accordance with generally accepted accounting principles, and that our receipts and expenditures are being made only in accordance with the authorizations of our management and directors; and (3) provide reasonable assurance regarding prevention or timely detection of unauthorized acquisition, use, or disposition of our assets that could have a material effect on our financial statements.
Management assessed the effectiveness of our internal control over financial reporting as of December 31, 2015. In making this assessment, management used the criteria set forth in Internal Control – Integrated Framework issued by COSO (2013 framework). A material weakness is a control deficiency, or combination of control deficiencies, that results in more than a remote likelihood that a material misstatement of the annual or interim financial statements will not be prevented or detected. Based on our assessment, management concluded that, as of December 31, 2015, our internal control over financial reporting was effective to provide reasonable assurance regarding the reliability of financial reporting and the preparation of financial statements for external purposes in accordance with U.S. generally accepted accounting principles.
This Annual Report on Form 10-K does not include an attestation report of our registered public accounting firm regarding internal control over financial reporting. Management's report was not subject to attestation by our registered public accounting firm pursuant to rules of the SEC that permit us to provide only management's report in this Annual Report on Form 10-K.
Changes in Internal Control over Financial Reporting.
There have been no changes in our internal control over financial reporting during the quarter ended December 31, 2015 that have materially affected, or are reasonably likely to affect materially, our internal control over financial reporting.
Because of its inherent limitations, internal control over financial reporting may not prevent or detect misstatements. Forward looking statements regarding the effectiveness of internal controls during future periods are subject to the risk that controls may become inadequate because of change in conditions, or that the degree of compliance with the policies and procedures may deteriorate.
| |
ITEM 9B. | Other Information. |
None.
PART III.
| |
ITEM 10. | Directors, Executive Officers and Corporate Governance. |
Pursuant to General Instruction G(3) of Form 10-K, the information required by this item relating to our executive officers is included under the caption “Executive Officers of the Company” in Part I of this Form 10-K.
The other information required under Item 10 will be included in our Proxy Statement for the 2016 Annual Meeting of Stockholders, which information is incorporated into this Annual Report by reference.
| |
ITEM 11. | Executive Compensation. |
The information required by this Item will be included in our definitive Proxy Statement for the 2016 Annual Meeting of Stockholders, which information is incorporated into this Annual Report by reference.
| |
ITEM 12. | Security Ownership of Certain Beneficial Owners and Management and Related Stockholder Matters. |
The information required by this Item will be included under the sections captioned “Ownership of Securities,” “Equity Compensation Plan Information” and “Potential Payments upon Termination or Change of Control” in our definitive Proxy Statement for the 2016 Annual Meeting of Stockholders, which information is incorporated into this Annual Report by reference.
| |
ITEM 13. | Certain Relationships and Related Transactions, and Director Independence. |
The information required by this Item will be included under the sections captioned “Certain Transactions” and “Director Independence” in our definitive Proxy Statement for the 2016 Annual Meeting of Stockholders, which information is incorporated into this Annual Report by reference.
| |
ITEM 14. | Principal Accounting Fees and Services. |
The information required by this Item will be included under the section captioned “Proposal Three: Ratification of Appointment of Independent Registered Public Accounting Firm” in our definitive Proxy Statement for the 2016 Annual Meeting of Stockholders, which information is incorporated into this Annual Report by reference.
PART IV.
| |
ITEM 15. | Exhibits, Financial Statement Schedules. |
(a)
1. Financial Statements.
The following financial statements of Active Power, Inc. were filed as a part of the Annual Report on Form 10-K for the fiscal year ending December 31, 2015:
|
| |
| Page |
| |
| |
Financial Statements: | |
| |
| |
| |
| 46 |
| |
2. Schedules.
All schedules have been omitted since the information required by the schedule is not applicable, or is not present in amounts sufficient to require submission of the schedule, or because the information required is included in the Financial Statements and notes thereto.
3. Exhibits.
The exhibits listed on the accompanying index to exhibits immediately following the financial statements are filed herewith, or are incorporated by reference as indicated below.
(b) Exhibits
See the Exhibit Index beginning on page 39 of this Form 10-K.
SIGNATURES
Pursuant to the requirements of Section 13 or 15(d) of the Securities Exchange Act of 1934, the registrant has duly caused this report to be signed on its behalf by the undersigned, thereunto duly authorized.
|
| | |
| ACTIVE POWER, INC. |
| | |
Dated: February 23, 2016 | By: | /s/ MARK A. ASCOLESE |
| | |
| | President and Chief Executive Officer |
Power of Attorney
KNOW ALL PERSONS BY THESE PRESENTS, that each person whose signature appears below hereby severally constitutes and appoints, Mark A. Ascolese and James A. Powers, and each or any of them, his true and lawful attorney-in-fact and agent, each with the power of substitution and resubstitution, for him in any and all capacities, to sign any and all amendments to this Annual Report on Form 10-K and to file the same, with exhibits thereto and other documents in connection therewith, with the Securities and Exchange Commission, hereby ratifying and confirming all that each said attorney-in-fact and agent, or his substitute or substitutes, may lawfully do or cause to be done by virtue hereof.
Pursuant to the requirements of the Securities Exchange Act of 1934, this report has been signed below by the following persons on behalf of the registrant and in the capacities and on the dates indicated.
|
| | | | |
Name | | Title | | Date |
| | | | |
/s/ MARK A. ASCOLESE | | President and Chief Executive Officer (principal executive officer) | | February 23, 2016 |
Mark A. Ascolese | | | |
| | | | |
/s/ JAMES A. POWERS | | Vice President—Finance, Chief Financial Officer (principal financial and accounting officer) | | February 23, 2016 |
James A. Powers | | | |
| | | | |
/s/ AKE ALMGREN | | Chairman of the Board, Director | | February 23, 2016 |
Ake Almgren | | | | |
| | | | |
/s/ JAMES E. DEVENNY III | | Director | | February 23, 2016 |
James E. deVenny III | | | | |
| | | | |
/s/ ROBERT S. GREENBERG | | Director | | February 23, 2016 |
Robert S. Greenberg | | | | |
| | | | |
/s/ STEPHEN J. CLEARMAN | | Director | | February 23, 2016 |
Stephen J. Clearman | | | | |
| | | | |
/s/ T. PATRICK KELLY | | Director | | February 23, 2016 |
T. Patrick Kelly | | | | |
/s/ PETER GROSS | | Director | | February 23, 2016 |
Peter Gross | | | | |
| | | | |
INDEX TO EXHIBITS
|
| | |
Exhibit Number | | Description |
3.1* | | Restated Certificate of Incorporation of Active Power, Inc., as amended (filed as Exhibit 3.1 to Active Power’s Quarterly Report on Form 10-Q filed on August 1, 2014) |
3.2* | | Second Amended and Restated Bylaws of Active Power, Inc., as amended (filed as Exhibit 3.2 to Active Power’s Quarterly Report on Form 10-Q filed on May 1, 2014) |
4.1* | | Specimen certificate for shares of Common Stock (filed as Exhibit 4.1 to Active Power’s IPO Registration Statement on Form S-1 (SEC File No. 333-36946) (the “IPO Registration Statement")) |
4.2* | | See Exhibits 3.1 and 3.2 for provisions of the Certificate of Incorporation and Bylaws of the registrant defining the rights of holders of common stock |
10.1* | | Form of Indemnity Agreement (filed as Exhibit 10.1 to the IPO Registration Statement) |
10.2*† | | Active Power, Inc. 2000 Stock Incentive Plan (filed as Exhibit 10.2 to the IPO Registration Statement) |
10.3*† | | Active Power, Inc. 2010 Equity Incentive Plan, as amended (filed as Exhibit 10.1 to Active Power's Quarterly Report on Form 10-Q filed on August 3, 2012) |
10.4*† | | Form of Standard Stock Option Agreement (filed as Exhibit 10.2 to Active Power's Current Report on Form 8-K filed on May 18, 2010) |
10.5*† | | Form of Standard Restricted Stock Agreement Stock Agreement (filed as Exhibit 10.3 to Active Power's Current Report on Form 8-K filed on May 18, 2010) |
10.6*† | | Form of Standard Restricted Stock Unit Agreement (filed as Exhibit 10.4 to Active Power's Current Report on Form 8-K filed on May 18, 2010) |
10.7* | | Lease Agreement between Active Power, Inc. and Braker Phase III, Ltd. (filed as Exhibit 10.9 to the IPO Registration Statement) |
10.8* | | First Amendment to Lease Agreement between Active Power, Inc. and Braker Phase III, Ltd. (filed as Exhibit 10.10 to the IPO Registration Statement) |
10.9* | | Second Amendment to Lease Agreement between Active Power, Inc. and Braker Phase III, Ltd. (filed as Exhibit 10.11 to the IPO Registration Statement) |
10.10* | | Third Amendment to Lease Agreement between Active Power, Inc. and Braker Phase III, Ltd. (filed as Exhibit 10.12 to the IPO Registration Statement) |
10.11* | | Fourth Amendment to Lease Agreement between Active Power, Inc. and Metropolitan Life Insurance Company (filed as Exhibit 10.13 to the IPO Registration Statement) |
10.12* | | Fifth Amendment to Lease Agreement between Active Power, Inc. and Metropolitan Life Insurance Company (filed as Exhibit 10.14 to the IPO Registration Statement) |
10.13* | | Sixth Amendment to Lease Agreement between Active Power, Inc. and Metropolitan Life Insurance Company (filed as Exhibit 10.18 to Active Power’s Annual Report on Form 10-K filed on March 16, 2001) |
10.14* | | Seventh Amendment to Lease Agreement between Active Power, Inc. and Metropolitan Life Insurance Company (filed as Exhibit 10.19 to Active Power’s Annual Report on Form 10-K filed on March 16, 2001) |
10.15* | | Eight Amendment to Lease Agreement between Active Power, Inc. and Metropolitan Life Insurance Company (filed as Exhibit 10.15 to Active Power’s Annual Report on Form 10-K filed on February 27, 2015) |
10.16* | | Ninth Amendment to Lease Agreement between Active Power, Inc. and Metropolitan Life Insurance Company (filed as Exhibit 10.16 to Active Power’s Annual Report on Form 10-K filed on February 27, 2015) |
10.17* | | Tenth Amendment to Lease Agreement between Active Power, Inc. and Metropolitan Life Insurance Company (filed as Exhibit 10.17 to Active Power’s Annual Report on Form 10-K filed on February 27, 2015) |
10.18* | | Eleventh Amendment to Lease Agreement between Active Power, Inc. and Metropolitan Life Insurance Company (filed as Exhibit 10.18 to Active Power’s Annual Report on Form 10-K filed on February 27, 2015) |
10.19* | | Twelfth Amendment to Lease Agreement between Active Power, Inc. and Metropolitan Life Insurance Company (filed as Exhibit 10.19 to Active Power’s Annual Report on Form 10-K filed on February 27, 2015) |
10.20* | | Thirteenth Amendment to Lease Agreement between Active Power, Inc. and Braker-Stonehollow, Ltd. (successor to Metropolitan Life Insurance Company) (filed as Exhibit 10.20 to Active Power’s Annual Report on Form 10-K filed on February 27, 2015) |
10.21* | | Fourteenth Amendment to Lease Agreement between Active Power, Inc. and Windsor at Stonehollow, LP (successor to Braker-Stonehollow, Ltd.) (filed as Exhibit 10.21 to Active Power’s Annual Report on Form 10-K filed on February 27, 2015) |
10.22* | | Fifteenth Amendment to Lease Agreement between Active Power, Inc. and Windsor at Stonehollow, LP (filed as Exhibit 10.22 to Active Power’s Annual Report on Form 10-K filed on February 27, 2015) |
|
| | |
10.23* | | Sixteenth Amendment to Lease Agreement between Active Power, Inc. and Stonehollow Industrial Investors, LLC (filed as Exhibit 10.23 to Active Power’s Annual Report on Form 10-K filed on February 27, 2015) |
10.24* | | Seventeenth Amendment to Lease between TR Stonehollow Corp. (successor-in-interest to Stonehollow Industrial Investors, LLC) and Active Power, Inc. (filed as Exhibit 10.1 to Active Power's Quarterly Report on Form 10-Q filed on October 27, 2015) |
10.25* | | Lease Agreement between Active Power, Inc. and BC12 99, Ltd. (filed as Exhibit 10.17 to Active Power’s Annual Report on Form 10-K filed on March 16, 2001) |
10.26* | | First Amendment to Lease Agreement between Active Power, Inc. and BC 12 99, LTD. (filed as Exhibit 10.25 to Active Power’s Annual Report on Form 10-K filed on February 27, 2015) |
10.27* | | Second Amendment to Lease Agreement between Active Power, Inc. and BC 12 99, LTD. (filed as Exhibit 10.26 to Active Power’s Annual Report on Form 10-K filed on February 27, 2015) |
10.28* | | Third Amendment to Lease Agreement between Active Power, Inc. and BC 12 99, LTD. (filed as Exhibit 10.27 to Active Power’s Annual Report on Form 10-K filed on February 27, 2015) |
10.29* | | Fourth Amendment to Lease Agreement between Active Power, Inc. and Levy Braker 12 Associates, LLC (successor in interest to BC 12 99, LTD.) (filed as Exhibit 10.28 to Active Power’s Annual Report on Form 10-K filed on February 27, 2015) |
10.30* | | Fifth Amendment to Lease Agreement between Levy Braker 12 Associates, LLC and Active Power, Inc. (filed as Exhibit 10.2 to Active Power's Quarterly Report on Form 10-Q filed on October 27, 2015) |
10.31*† | | 2015 Adleman Incentive Plan (filed as Exhibit 10.29 to Active Power’s Annual Report on Form 10-K filed on February 27, 2015) |
10.32*† | | Form of Severance Benefits Agreement (filed as Exhibit 10.4 to Active Power's Quarterly Report on Form 10-Q filed on April 27, 2010) |
10.33*† | | Offer Letter, effective September 26, 2013, between Active Power, Inc. and Mark A. Ascolese (filed as Exhibit 10.1 to Active Power’s Quarterly Report on Form 10-Q filed on November 18, 2013) |
10.34*† | | Severance Benefits Agreement, effective September 26, 2013, between Active Power, Inc. and Mark A. Ascolese (filed as Exhibit 10.2 to Active Power’s Quarterly Report on Form 10-Q filed on November 18, 2013) |
10.35*† | | Offer Letter, effective November 4, 2013, between Active Power, Inc. and Randall J. Adleman (filed as Exhibit 10.3 to Active Power’s Quarterly Report on Form 10-Q filed on November 18, 2013) |
10.36*† | | Severance Benefits Agreement, effective November 4, 2013, between Active Power, Inc. and Randall J. Adleman (filed as Exhibit 10.4 to Active Power’s Quarterly Report on Form 10-Q filed on November 18, 2013) |
10.37*† | | Offer Letter, dated November 14, 2013, between Active Power, Inc. and James A. Powers (filed as Exhibit 10.21 to Active Power’s Annual Report on Form 10-K filed on March 4, 2014) |
10.38*† | | Severance Benefits Agreement, dated November 14, 2013, between Active Power, Inc. and James A. Powers (filed as Exhibit 10.22 to Active Power’s Annual Report on Form 10-K filed on March 4, 2014) |
10.39* | | Second Amended and Restated Loan and Security Agreement dated as of August 5, 2010 between Active Power, Inc. and Silicon Valley Bank (filed as Exhibit 10.1 to Active Power's Quarterly Report on Form 10-Q filed on October 27, 2010) |
10.40* | | First Amendment to Second Amended and Restated Loan and Security Agreement, dated March 5, 2012, between Active Power, Inc. and Silicon Valley Bank (filed as Exhibit 10.3 to Active Power's Quarterly Report on Form 10-Q filed on August 3, 2012) |
10.41* | | Second Amendment to Second Amended and Restated Loan and Security Agreement dated August 15, 2012 between Active Power, Inc. and Silicon Valley Bank (filed as Exhibit 10.1 to Active Power’s Current Report on Form 8-K filed on August 20, 2012) |
10.42* | | Third Amendment to Second Amended and Restated Loan and Security Agreement dated July 28, 2014 between Active Power, Inc. and Silicon Valley Bank (filed as Exhibit 10.1 to Active Power’s Current Report on Form 8-K filed on July 29, 2014) |
10.43* | | Guarantee and Debenture Agreement, dated as of August 5, 2010 between Active Power Solutions Limited and Silicon Valley Bank(filed as Exhibit 10.2 to Active Power's Quarterly Report on Form 10-Q filed on October 27, 2010) |
10.44*+ | | Purchase Agreement effective as of June 1, 2011 between Active Power, Inc. and Caterpillar, Inc. (filed as Exhibit 10.6 to Active Power’s Quarterly Report on Form 10-Q filed on April 30, 2012) |
|
| | |
10.45*† | | 2015 Management Incentive Plan (filed as Exhibit 10.1 to Active Power’s Current Report on Form 8-K filed on February 17, 2015) |
10.46*† | | Cash Incentive Plan (filed as Exhibit 10.1 to Active Power’s Current Report on Form 8-K filed on February 16, 2016) |
10.47*+ | | Hardware Product Purchase Agreement, dated April 30, 2010 between Active Power, Inc. and Hewlett-Packard Company (filed as Exhibit 10.25 to Active Power's Annual Report on Form 10-K filed on March 1, 2012) |
10.48++ | | Amendment 1, dated January 1, 2014, to Hardware Product Purchase Agreement between Active Power, Inc. and Hewlett-Packard Company |
10.49++ | | Amendment 2, dated April 1, 2015, to Hardware Product Purchase Agreement between Active Power, Inc. and Hewlett-Packard Company |
21.1 | | Subsidiaries of the Registrant |
23.1 | | Consent of Grant Thornton LLP |
24.1 | | Power of Attorney, pursuant to which amendments to this Form 10-K may be filed, is included on the signature page contained in Part IV of this Form 10-K |
31.1 | | Certification of Principal Executive Officer as required by Section 302 of the Sarbanes-Oxley Act of 2002 |
31.2 | | Certification of Principal Financial Officer as required by Section 302 of the Sarbanes-Oxley Act of 2002 |
32.1 | | Certification of Principal Executive Officer as required by Section 906 of the Sarbanes-Oxley Act of 2002 |
32.2 | | Certification of Principal Financial Officer as required by Section 906 of the Sarbanes-Oxley Act of 2002 |
101 | | The following financial statements from Active Power's Annual Report on Form 10-K for the fiscal year ended December 31, 2015, formatted in XBRL: (i) Consolidated Balance Sheets, (ii) Consolidated Statement of Operations and Comprehensive Loss, (iii) Consolidated Statement of Cash Flows, and (iv) Notes to Consolidated Financial Statements. |
|
| |
* | Incorporated by reference to the indicated filing. |
+ | Portions of this exhibit have been omitted pursuant to a confidential treatment previously granted. |
++ | Confidential treatment has been requested with respect to certain portions of this exhibit.
|
† | Management contract or compensatory plan or arrangement. |
REPORT OF INDEPENDENT REGISTERED PUBLIC ACCOUNTING FIRM
Board of Directors and Shareholders
Active Power, Inc.
We have audited the accompanying consolidated balance sheets of Active Power, Inc. (a Delaware corporation) and subsidiaries as of December 31, 2015 and 2014, and the related consolidated statements of operations and comprehensive loss, stockholders’ equity, and cash flows for each of the three years in the period ended December 31, 2015. These financial statements are the responsibility of the Company’s management. Our responsibility is to express an opinion on these financial statements based on our audits.
We conducted our audits in accordance with the standards of the Public Company Accounting Oversight Board (United States). Those standards require that we plan and perform the audit to obtain reasonable assurance about whether the financial statements are free of material misstatement. We were not engaged to perform an audit of the Company’s internal control over financial reporting. Our audits included consideration of internal control over financial reporting as a basis for designing audit procedures that are appropriate in the circumstances, but not for the purpose of expressing an opinion on the effectiveness of the Company’s internal control over financial reporting. Accordingly, we express no such opinion. An audit also includes examining, on a test basis, evidence supporting the amounts and disclosures in the financial statements, assessing the accounting principles used and significant estimates made by management, as well as evaluating the overall financial statement presentation. We believe that our audits provide a reasonable basis for our opinion.
In our opinion, the consolidated financial statements referred to above present fairly, in all material respects, the financial position of Active Power, Inc. and subsidiaries as of December 31, 2015 and 2014, and the results of their operations and their cash flows for each of the three years in the period ended December 31, 2015, in conformity with accounting principles generally accepted in the United States of America.
|
| |
| /s/ Grant Thornton LLP |
Dallas, Texas | |
February 23, 2016 | |
Active Power, Inc.
Consolidated Balance Sheets
(in thousands, except par value)
|
| | | | | | | |
| December 31, 2015 | | December 31, 2014 |
ASSETS | | | |
Current assets: | | | |
Cash and cash equivalents | $ | 12,260 |
| | $ | 14,824 |
|
Restricted cash | 36 |
| | 40 |
|
Accounts receivable, net of allowance for doubtful accounts of $70 and $212 at December 31, 2015 and December 31, 2014, respectively | 8,849 |
| | 11,222 |
|
Inventories, net | 6,466 |
| | 6,845 |
|
Prepaid expenses and other | 792 |
| | 800 |
|
Total current assets | 28,403 |
| | 33,731 |
|
Property and equipment, net | 1,914 |
| | 2,076 |
|
Deposits and other | 278 |
| | 291 |
|
Total assets | $ | 30,595 |
| | $ | 36,098 |
|
LIABILITIES AND STOCKHOLDERS' EQUITY | |
| | |
|
Current liabilities: | |
| | |
|
Accounts payable | $ | 2,852 |
| | $ | 4,044 |
|
Accrued expenses | 4,494 |
| | 4,134 |
|
Deferred revenue | 3,576 |
| | 2,771 |
|
Revolving line of credit | 5,535 |
| | 5,535 |
|
Total current liabilities | 16,457 |
| | 16,484 |
|
Long-term liabilities | 583 |
| | 821 |
|
Commitments and contingencies |
|
| |
|
|
Stockholders' equity | |
| | |
|
Preferred stock - $0.001 par value; 2,000 shares authorized | — |
| | — |
|
Common stock - $0.001 par value; 40,000 shares authorized; 23,171 and 23,162 issued and 23,109 and 23,094 outstanding at December 31, 2015 and 2014, respectively | 23 |
| | 23 |
|
Treasury stock | (240 | ) | | (231 | ) |
Additional paid-in capital | 304,094 |
| | 302,667 |
|
Accumulated deficit | (290,454 | ) | | (283,995 | ) |
Other accumulated comprehensive income | 132 |
| | 329 |
|
Total stockholders' equity | 13,555 |
| | 18,793 |
|
Total liabilities and stockholders' equity | $ | 30,595 |
| | $ | 36,098 |
|
See accompanying notes.
43
Active Power, Inc.
Consolidated Statement of Operations and Comprehensive Loss
(in thousands, except per share amounts)
|
| | | | | | | | | | | |
| Year Ended December 31, |
| 2015 | | 2014 | | 2013 |
Revenues: | | | | | |
Product revenue | $ | 43,247 |
| | $ | 36,211 |
| | $ | 44,158 |
|
Service and other revenue | 14,174 |
| | 12,925 |
| | 17,541 |
|
Total revenue | 57,421 |
| | 49,136 |
| | 61,699 |
|
Cost of goods sold: | |
| | |
| | |
|
Cost of product revenue | 32,017 |
| | 29,182 |
| | 32,825 |
|
Cost of service and other revenue | 8,587 |
| | 7,302 |
| | 9,478 |
|
Total cost of goods sold | 40,604 |
| | 36,484 |
| | 42,303 |
|
Gross profit | 16,817 |
| | 12,652 |
| | 19,396 |
|
Operating expenses: | |
| | |
| | |
|
Research and development | 5,723 |
| | 6,689 |
| | 7,430 |
|
Selling and marketing | 10,589 |
| | 11,940 |
| | 12,032 |
|
General and administrative | 6,565 |
| | 6,043 |
| | 7,551 |
|
Total operating expenses | 22,877 |
| | 24,672 |
| | 27,013 |
|
Loss from Operations | (6,060 | ) | | (12,020 | ) | | (7,617 | ) |
Interest expense | (375 | ) | | (395 | ) | | (370 | ) |
Other expense, net | (24 | ) | | (160 | ) | | (364 | ) |
Loss before income taxes | (6,459 | ) | | (12,575 | ) | | (8,351 | ) |
Income tax expense | — |
| | (252 | ) | | — |
|
Net Loss | $ | (6,459 | ) | | $ | (12,827 | ) | | $ | (8,351 | ) |
Net Loss per share, basic and diluted | $ | (0.28 | ) | | $ | (0.57 | ) | | $ | (0.43 | ) |
Shares used in computing net loss per share, basic and diluted | 23,134 |
| | 22,494 |
| | 19,329 |
|
Comprehensive loss: | |
| | |
| | |
|
Net loss | $ | (6,459 | ) | | $ | (12,827 | ) | | $ | (8,351 | ) |
Translation gain (loss) on subsidiaries denominated in foreign currencies | (197 | ) | | (377 | ) | | 384 |
|
Comprehensive loss | $ | (6,656 | ) | | $ | (13,204 | ) | | $ | (7,967 | ) |
See accompanying notes.
44
Active Power, Inc.
Consolidated Statement of Stockholders' Equity
(in thousands, except per share amounts)
|
| | | | | | | | | | | | | | | | | | | | | | | | | | | | | |
| Common Stock | | Treasury Stock | | | | | | | | |
| Number of Shares | | Par Value | | Number of Shares | | At Cost | | Additional Paid-In Capital | | Accumulated Deficit | | Other Accumulated Comprehen- sive Income (Loss) | | Total Stockholders' Equity |
Balance at December 31, 2012 | 19,171 |
| | $ | 19 |
| | 33 |
| | $ | (144 | ) | | $ | 288,619 |
| | $ | (262,817 | ) | | $ | 322 |
| | $ | 25,999 |
|
Employee stock option exercises | 200 |
| | — |
| | — |
| | — |
| | 711 |
| | — |
| | — |
| | 711 |
|
Release of Restricted Stock | 81 |
| | — |
| | — |
| | — |
| | 4 |
| | — |
| | — |
| | 4 |
|
Shares held in treasury | — |
| | — |
| | 18 |
| | (71 | ) | | — |
| | — |
| | — |
| | (71 | ) |
Net translation gain on foreign subsidiaries | — |
| | — |
| | — |
| | — |
| | — |
| | — |
| | 384 |
| | 384 |
|
Stock-based compensation | |
| | |
| | |
| | |
| | 1,689 |
| | |
| | — |
| | 1,689 |
|
Issuance costs, shelf registration | — |
|
| — |
|
| — |
|
| — |
|
| (59 | ) |
| — |
|
| — |
|
| (59 | ) |
Net Loss | — |
| | — |
| | — |
| | — |
| | — |
| | (8,351 | ) | | — |
| | (8,351 | ) |
Balance at December 31, 2013 | 19,452 |
| | $ | 19 |
| | 51 |
| | $ | (215 | ) | | $ | 290,964 |
| | $ | (271,168 | ) | | $ | 706 |
| | $ | 20,306 |
|
Employee stock option exercises | 43 |
| | — |
| | — |
| | — |
| | 129 |
| | — |
| | — |
| | 129 |
|
Sale of common stock, less issuance costs | 3,651 |
|
| 4 |
|
| |
|
| |
|
| 10,434 |
|
| |
|
| |
|
| 10,438 |
|
Release of Restricted Stock | 16 |
| | — |
| | |
| | |
| |
|
| | — |
| | — |
| | — |
|
Shares held in treasury | — |
| | — |
| | 5 |
| | (16 | ) | | — |
| | — |
| | — |
| | (16 | ) |
Net translation loss on foreign subsidiaries | — |
| | — |
| | — |
| | — |
| | — |
| | — |
| | (377 | ) | | (377 | ) |
Stock-based compensation | — |
| | — |
| | — |
| | — |
| | 1,140 |
| | — |
| | — |
| | 1,140 |
|
Net Loss | — |
| | — |
| | — |
| | — |
| | — |
| | (12,827 | ) | | — |
| | (12,827 | ) |
Balance at December 31, 2014 | 23,162 |
| | $ | 23 |
| | 56 |
| | $ | (231 | ) | | $ | 302,667 |
| | $ | (283,995 | ) | | $ | 329 |
| | $ | 18,793 |
|
Release of Restricted Stock | 9 |
| | — |
| | |
| | |
| | | | — |
| | — |
| | — |
|
Shares held in treasury | — |
| | — |
| | 6 |
| | (9 | ) | | — |
| | — |
| | — |
| | (9 | ) |
Net translation loss on foreign subsidiaries | — |
| | — |
| | — |
| | — |
| | — |
| | — |
| | (197 | ) | | (197 | ) |
Stock-based compensation | — |
| | — |
| | — |
| | — |
| | 1,427 |
| | — |
| | — |
| | 1,427 |
|
Net Loss | — |
| | — |
| | — |
| | — |
| | — |
| | (6,459 | ) | | — |
| | (6,459 | ) |
Balance at December 31, 2015 | 23,171 |
| | $ | 23 |
| | 62 |
| | $ | (240 | ) | | $ | 304,094 |
| | $ | (290,454 | ) | | $ | 132 |
| | $ | 13,555 |
|
See accompanying notes.
45
Active Power, Inc.
Consolidated Statement of Cash Flows
(in thousands)
|
| | | | | | | | | | | |
| Year ended December 31, |
| 2015 | | 2014 | | 2013 |
Operating activities | | | | | |
Net Loss | $ | (6,459 | ) | | $ | (12,827 | ) | | $ | (8,351 | ) |
Adjustments to reconcile net loss to cash used in operating activities: | |
| | |
| | |
|
Depreciation expense | 997 |
| | 1,220 |
| | 1,084 |
|
Change to allowance for doubtful accounts | (142 | ) | | (101 | ) | | (175 | ) |
Loss on disposal of fixed assets | 7 |
| | 4 |
| | 30 |
|
Impairment on fixed assets | — |
| | 57 |
| | 69 |
|
Stock-based compensation | 1,427 |
| | 1,140 |
| | 1,700 |
|
Changes in operating assets and liabilities: | |
| | |
| | |
|
Restricted cash | 4 |
| | 480 |
| | (520 | ) |
Accounts receivable | 2,515 |
| | (2,046 | ) | | 8,962 |
|
Inventories | 283 |
| | 5,257 |
| | (1,796 | ) |
Prepaid expenses and other assets | 22 |
| | (116 | ) | | (99 | ) |
Accounts payable | (1,192 | ) | | 1,051 |
| | (1,043 | ) |
Accrued expenses | 360 |
| | (1,449 | ) | | 623 |
|
Deferred revenue | 805 |
| | 22 |
| | (1,819 | ) |
Long term liabilities | (238 | ) | | 80 |
| | 28 |
|
Net cash used in operating activities | (1,611 | ) | | (7,228 | ) | | (1,307 | ) |
Investing activities | |
| | |
| | |
|
Purchases of property and equipment | (779 | ) | | (343 | ) | | (996 | ) |
Proceeds from sale of fixed assets | — |
| | 19 |
| | 71 |
|
Net cash used in investing activities | (779 | ) | | (324 | ) | | (925 | ) |
Financing activities | |
| | |
| | |
|
Proceeds from public offering of common stock, net of issuance cost | — |
| | 10,438 |
| | — |
|
Proceeds from employee stock option exercises | — |
| | 129 |
| | 711 |
|
Issuance costs, shelf registration | — |
| | — |
| | (59 | ) |
Taxes paid related to the net share settlement of equity awards | (9 | ) | | (16 | ) | | (67 | ) |
Net cash (used in) provided by financing activities | (9 | ) | | 10,551 |
| | 585 |
|
Effects of exchange rates on cash | (165 | ) | | (436 | ) | | 384 |
|
Change in cash and cash equivalents | (2,564 | ) | | 2,563 |
| | (1,263 | ) |
Cash and cash equivalents, beginning of period | 14,824 |
| | 12,261 |
| | 13,524 |
|
Cash and cash equivalents, end of period | $ | 12,260 |
| | $ | 14,824 |
| | $ | 12,261 |
|
Supplemental Cash Flow Information: | |
| | |
| | |
|
Interest Paid | $ | 354 |
| | $ | 401 |
| | $ | 380 |
|
Income Tax Paid | $ | — |
| | $ | 252 |
| | $ | — |
|
See accompanying notes.
46
ACTIVE POWER, INC.
NOTES TO CONSOLIDATED FINANCIAL STATEMENTS
December 31, 2015
(in thousands, except share and per share amounts)
1. Summary of Significant Accounting Policies
Description of Business
Active Power, Inc. and its subsidiaries (collectively, “we”, “us”, “Active Power” or “Company”) design, manufacture, sell, and service flywheel-based uninterruptible power supply (“UPS”) products that use kinetic energy to provide short-term power as a cleaner alternative to conventional electro-chemical battery-based energy storage. We also design, manufacture, sell, and service modular infrastructure solutions (“MIS”) that integrate critical power components into a pre-packaged, purpose-built enclosure that may include our UPS products as a component. In 2015, 72% of our product revenue came from the sale of UPS systems and 28% from the sale of MIS products. Our products and solutions are based on our patented flywheel and power electronics technology and are designed to ensure continuity for data centers and other mission critical operations in the event of power disturbances.
Our products and solutions are designed to deliver continuous conditioned power during power disturbances such as voltage sags and surges, and to provide ride-through power in the event of a brief utility failure, supporting operations until utility power is restored or a longer term alternative power source, such as a diesel generator, is started. We sell our products globally through our direct sales force, manufacturer’s representatives, distributors, original equipment manufacturers (“OEM”), and IT channel partners in the Americas, in Europe, the Middle East, and Africa (“EMEA”), and in the Asia Pacific region (“APAC”).
We also offer services, including hardware and software maintenance, on all Active Power products, and other professional services such as assessment and implementation, for our customers’ infrastructure projects.
We were founded as a Texas corporation in 1992 and reincorporated in Delaware in 2000. Our headquarters are in Austin, Texas, with international offices in the United Kingdom, Germany, and China.
The accompanying consolidated financial statements have been prepared in accordance with accounting principles generally accepted in the United States of America (“US GAAP”) and include the accounts of the Company and its consolidated subsidiaries. All intercompany transactions and balances have been eliminated upon consolidation.
The accompanying consolidated financial statements have also been prepared on the assumption that the Company will continue to operate as a going concern. Accordingly, assets and liabilities are recorded on the basis that the Company will be able to realize its assets and discharge its liabilities in the normal course of business. The Company’s history of operating losses and use of cash, in the absence of other factors, may cause uncertainty as to its ability to continue as a going concern. We have reviewed the current and prospective sources of liquidity, significant conditions and events and forecast financial results and concluded that we have adequate resources to continue to operate as a going concern. Our business plan and our assumptions around the adequacy of our liquidity are based on estimates regarding expected revenues and future costs. However, our revenues may not meet our projections or our costs may exceed our estimates. Further, our estimates may change and future events or developments may also affect our estimates. Any of these factors may change our expectation of cash usage in 2016 or significantly affect our level of liquidity, which may require us to seek additional financing or take other measures to reduce our operating costs in order to continue operating. These financial statements do not include any adjustments that might result from the Company not being able to continue as a going concern.
Use of Estimates
The preparation of financial statements in conformity with US GAAP requires management to make estimates and assumptions that affect the amounts reported in the financial statements and accompanying notes. Actual results could differ from those estimates. Changes in the estimates or assumptions used by management could have a material impact upon reported amounts and our results of operations.
Revenue Recognition
We recognize revenue when four criteria are met: (i) persuasive evidence that an arrangement exists; (ii) delivery has occurred or services have been rendered; (iii) the sales price is fixed or determinable; and (iv) collectability is reasonably assured. In general, revenue is recognized when revenue-generating transactions fall into one of the following categories of revenue recognition:
| |
• | We recognize product revenue at the time of shipment for a significant portion of all products sold directly to customers and through distributors because title and risk of loss pass on delivery to the common carrier. Our customers and distributors do not have the right to return products. We may enter into bill-and-hold arrangements and when this occurs delivery may not be present, but other criteria are reviewed to determine proper timing of revenue recognition. |
| |
• | Unless performed under a maintenance contract, we recognize installation, service and maintenance revenue at the time the service is performed. |
| |
• | We recognize revenue associated with maintenance agreements over the life of the contracts using the straight-line method, which approximates the expected timing in which applicable services are performed. Amounts collected in advance of revenue recognition are recorded as a current liability in the deferred revenue line of the consolidated balance sheet or long-term liability based on the time from the balance sheet date to the future date of revenue recognition. |
| |
• | We recognize revenue on certain rental programs over the life of the rental agreement using the straight-line method. Amounts collected in advance of revenue recognition are recorded as a current or long-term liability based on the time from the balance sheet date to the future date of revenue recognition. |
When collectability is not reasonably assured, we defer revenue and will recognize revenue as payments are received.
Multiple element arrangements (“MEAs”) are arrangements to sell products to customers that frequently include multiple deliverables. Our most significant MEAs include the sale of one or more of our CleanSource® UPS or CleanSource PowerHouse products, combined with one or more of the following products or services: design services, project management, commissioning and installation services, spare parts or consumables, and maintenance agreements. Delivery of the various products or performance of services within the arrangement may or may not coincide. Certain services related to design and consulting may occur prior to product delivery. Commissioning and installation typically take place within six months of product delivery, depending upon customer requirements. Maintenance agreements, consumables, and repair, maintenance or consulting services are generally delivered over a period of one to five years.
When arrangements include multiple elements, we allocate revenue to each element based on the relative selling price and recognize revenue when the elements have standalone value and the four criteria for revenue recognition have been met. We establish the selling price of each element based on Vendor Specific Objective Evidence (“VSOE”) if available, Third Party Evidence (“TPE”) if VSOE is not available, or best estimate of selling price (“BESP”) if neither VSOE nor TPE is available. We generally determine selling price based on amounts charged separately for the delivered and undelivered elements to similar customers in standalone sales of the specific elements. When arrangements include a maintenance agreement, we recognize revenue related to the maintenance agreement at the relative selling price on a straight-line basis over the life of the agreement.
Any taxes imposed by governmental authorities on our revenue-producing transactions with customers are shown in our consolidated statements of operations on a net-basis; that is, excluded from our reported revenues.
Shipping and Handling Costs
We classify shipping and handling costs related to product sales as cost of revenue, and any payments from customers for shipping and handling are categorized in revenue. We classify shipping and handling costs associated with receiving production inventory as cost of product revenue. Any materials received or shipped which are related to our engineering, sales, marketing and administrative functions are classified as operating expenses.
Cash and Cash Equivalents
Investments with a contractual maturity of three months or less when purchased are classified as cash equivalents.
Fair Value of Financial Instruments
Fair value is measured based on an exit price, representing the amount that would be received to sell an asset or paid to satisfy a liability in an orderly transaction between market participants. Fair value is a market-based measurement that should be determined based on assumptions that market participants would use in pricing an asset or liability. As a basis for considering such assumptions, a fair value hierarchy is established, which categorizes the inputs used in measuring fair value as follows:
Level 1—Quoted prices in active markets for identical assets or liabilities.
Level 2—Significant observable inputs other than quoted prices in Level 1, such as quoted prices for similar assets and liabilities in active markets; quoted prices for identical or similar assets and liabilities in markets that are not active; or other inputs that are observable or can be corroborated by observable market data.
Level 3—One or more significant inputs that are unobservable and supported by little or no market data.
Highest priority is given for Level 1 input and lower propriety to Level 3 inputs. A financial instruments level is based on the lowest level of any input that is significant to the fair value measurement. No changes were made to our methodology.
Our Level 1 assets consist of cash equivalents, which are primarily invested in money-market funds. These assets are classified as Level 1 because they are valued using quoted prices in active markets and other relevant information generated by market transactions involving identical assets and liabilities. The fair value was $3.1 million as of December 31, 2015 and 2014.
For cash and cash equivalents, accounts receivable, accounts payable and our revolving line of credit, the carrying amount approximates fair value because of the relative short maturity of those instruments.
Allowance for Doubtful Accounts
We estimate an allowance for doubtful accounts based on factors related to the credit risk of each customer. Historically, credit losses have been minimal, primarily because the majority of our revenues were generated from large customers, such as Caterpillar, Inc. (“Caterpillar”) and Hewlett Packard Enterprise (“HPE”). We perform credit evaluations of new customers and when necessary we require deposits, prepayments or use of bank instruments such as trade letters of credit to mitigate our credit risk. We write off uncollectible trade receivables, and record any recoveries of previous write offs against the allowance. Our standard payment terms are net 30 days; however, we may have agreements with certain larger customers and certain distributors that allow for more extended terms at or above net 60 days.
The following table summarizes the annual changes in our allowance for doubtful accounts (in thousands):
|
| | | |
Balance at December 31, 2012 | $ | 488 |
|
Change in provision credited to expense, net | (139 | ) |
Write-off of uncollectible accounts, net of recoveries | (36 | ) |
Balance at December 31, 2013 | $ | 313 |
|
Change in provision credited to expense, net | (67 | ) |
Write-off of uncollectible accounts, net of recoveries | (34 | ) |
Balance at December 31, 2014 | $ | 212 |
|
Change in provision credited to expense, net | (142 | ) |
Write-off of uncollectible accounts | — |
|
Balance at December 31, 2015 | $ | 70 |
|
Inventories, net
Inventories are stated at the lower of cost or market, using the first-in-first-out method, and consist of the following at December 31 (in thousands, net of allowances of $0.8 million in both 2015 and 2014):
|
| | | | | | | |
| 2015 | | 2014 |
Raw materials | $ | 4,748 |
| | $ | 5,440 |
|
Work in progress | 1,425 |
| | 473 |
|
Finished goods | 293 |
| | 932 |
|
| $ | 6,466 |
| | $ | 6,845 |
|
Property and Equipment
Property and equipment is stated at cost and is depreciated using the straight-line method over the estimated useful lives of the assets, as follows (in years):
|
| |
Equipment | 2 - 10 |
Demonstration units | 3 - 5 |
Computers and purchased software | 2 - 3 |
Furnitures and fixtures | 2 - 5 |
Leasehold improvements are depreciated over the shorter of the life of the improvement or the remainder of the property lease term, including renewal options, generally three to five years. Repairs and maintenance is expensed as incurred.
Long-Lived Assets
Long-lived assets held and used by the Company are reviewed for impairment whenever events or changes in circumstances indicate that their net book value may not be recoverable. When such factors and circumstances exist, we compare the projected undiscounted future cash flows associated with the related asset or group of assets over their estimated useful lives against their respective carrying amounts. Impairment, if any, is based on the excess of the carrying amount over the fair value of those assets and is recorded in the period in which the determination was made.
Accrued Expenses
Accrued expenses consist of the following at December 31 (in thousands):
|
| | | | | | | |
| 2015 | | 2014 |
Compensation, severance and benefits | $ | 727 |
| | $ | 1,296 |
|
Management incentive bonus | 1,282 |
| | — |
|
Warranty liability | 531 |
| | 475 |
|
Taxes, other than income | 518 |
| | 1,080 |
|
Professional fees | 441 |
| | 463 |
|
Other | 995 |
| | 820 |
|
| $ | 4,494 |
| | $ | 4,134 |
|
Warranty Liability
Generally, the warranty period for our products is 12 months from the date of commissioning or 18 months from the date of shipment from Active Power, whichever period is shorter. Occasionally, we provide longer warranty periods to certain customers. The warranty period for products sold to our primary OEM customer, Caterpillar, is 12 months from the date of shipment to the end-user, or up to 36 months from shipment from Active Power, whichever period is shorter. This is dependent upon Caterpillar complying with our storage requirements for our products in order to preserve this warranty period beyond the standard 18-month
limit. We provide for the estimated cost of product warranties at the time revenue is recognized, and this accrual is included in accrued expenses and long-term liabilities on the accompanying consolidated balance sheet.
Changes in our warranty liability are as follows (in thousands):
|
| | | |
Balance at December 31, 2012 | $ | 755 |
|
Warranty expense | 589 |
|
Payments | (782 | ) |
Balance at December 31, 2013 | $ | 562 |
|
Warranty expense | 660 |
|
Payments | (695 | ) |
Balance at December 31, 2014 | $ | 527 |
|
Warranty expense | 580 |
|
Payments | (535 | ) |
Balance at December 31, 2015 | $ | 572 |
|
|
| | | | | | | |
| 2015 | | 2014 |
Warranty liability included in accrued expenses
| $ | 531 |
| | $ | 475 |
|
Long term warranty liability | 41 |
| | 52 |
|
| $ | 572 |
| | $ | 527 |
|
Long-Term Liabilities
Long-term liabilities consist of the following at December 31 (in thousands):
|
| | | | | | | |
| 2015 | | 2014 |
Deferred revenue | $ | 542 |
| | $ | 751 |
|
Warranty liability | 41 |
| | 52 |
|
Sublease deposits | — |
| | 18 |
|
| $ | 583 |
| | $ | 821 |
|
Stock-Based Compensation Expense
We account for our stock-based compensation using the Black Scholes option valuation model. Stock-based compensation cost is estimated at the grant date based on the fair-value of the award and is recognized as expense ratably over the requisite service period of the award, generally four years. We develop our estimates of expected life and forfeitures based on historical data. We estimate stock price volatility based on historical volatilities. The risk-free rates are based on the U.S. Treasury yield in effect at the time of grant. Details of our stock-based compensation include the following (in thousands):
|
| | | | | | | | | | | |
| 2015 | | 2014 | | 2013 |
Stock-based compensation expense by caption: |
| |
| |
|
Cost of product revenue | $ | 111 |
| | $ | 110 |
| | $ | 254 |
|
Cost of service and other revenue | 73 |
| | 111 |
| | 116 |
|
Research and development | 125 |
| | 207 |
| | 204 |
|
Selling and marketing | 402 |
| | 370 |
| | 587 |
|
General and administrative | 716 |
| | 342 |
| | 539 |
|
| $ | 1,427 |
| | $ | 1,140 |
| | $ | 1,700 |
|
Stock-based compensation expense by type of award: |
|
| |
|
| |
|
|
Stock options | $ | 1,366 |
| | $ | 1,068 |
| | $ | 1,488 |
|
Restricted stock awards | 61 |
| | 72 |
| | 212 |
|
| $ | 1,427 |
| | $ | 1,140 |
| | $ | 1,700 |
|
Assumptions used in the Black-Scholes model for our stock plans are presented below:
|
| | | | | | | | |
| 2015 | | 2014 | | 2013 |
Weighted average expected life in years | 6.25 years |
| | 6.27 years |
| | 6.35 years |
|
Weighted average expected volatility | 65 | % | | 75 | % | | 76 | % |
Volatility Range | 58%-71% |
| | 73%-76% |
| | 75%-76% |
|
Risk-free interest rate range | 1.89%-1.95% |
| | 1.96%-2.12% |
| | 1.13%-2.38% |
|
Weighted average forfeiture rate | 28.5 | % | | 29.7 | % | | 18.9 | % |
Income Taxes
We account for income taxes using the liability method of accounting for income taxes. Under the liability method, deferred taxes are determined based on the differences between the financial statement and tax basis of assets and liabilities using enacted tax rates in effect in the years in which the differences are expected to reverse. A valuation allowance is recorded to reduce the carrying amounts of deferred tax assets if it is more likely than not such assets will not be realized. Deferred income taxes reflect the net tax effects of temporary differences between the carrying amounts of assets and liabilities for financial reporting purposes and the amounts used for income tax purposes.
We recognize the financial statement benefit of a tax position that does not meet the more-likely-than-not threshold only after the statute of limitations expire of the relevant tax authority sustains the Company’s position following an audit. For tax positions meeting the more likely-than-not threshold, the amount recognized in the financial statements is the largest benefit that has a greater than 50 percent likelihood of being realized upon the ultimate settlement with the relevant tax authority. At December 31, 2015 and 2014, the Company had no material unrecognized tax benefits.
The Company recognizes interest and penalties related to uncertain tax positions in income tax expense. As of December 31, 2015 and 2014, the Company had no accrued or expensed interest or penalties related to uncertain tax positions.
Segment Reporting
The Company operates as a single operating segment. According to the FASB ASC Topic Disclosures about Segments of an Enterprise and Related Information , operating segments are defined as components of an enterprise for which separate financial information is evaluated regularly by the chief operating decision maker ("CODM") in deciding how to allocate resources and in assessing performance. The Company’s CODM is the Chief Executive Officer who evaluates the Company’s financial information and resources and assesses performance on a consolidated basis.
Concentration of Credit Risk
Financial instruments which potentially subject Active Power to concentrations of credit risk consist of cash and cash equivalents, investments and accounts receivable. Active Power’s cash and cash equivalents and investments are placed with high credit quality financial institutions and issuers. From time to time, we may have amounts on deposit with financial institutions that are in excess of the federally insured limit. We have not experienced any losses on deposits of cash and cash equivalents.
Active Power performs credit evaluations of its customers’ financial condition prior to entering into commercial transactions. We generally require letters of credit or prepayments from higher-risk customers as deemed necessary to ensure collection. Our allowance for doubtful accounts is estimated based on factors related to the credit risk of each customer. Individual receivables are written off after they have been deemed uncollectible. We also purchase several components from sole source or limited source suppliers.
Economic Dependence
We are significantly dependent on our relationships with HPE and Caterpillar. If these relationships are unsuccessful or discontinue, our business and revenue may suffer. The loss of, or a significant reduction in, orders from HPE or Caterpillar, or the failure to provide adequate service and support to the end-users of our products by HPE or Caterpillar, could significantly reduce our revenue. Our operating results in the foreseeable future will continue to depend on the sales made by a relatively small number of customers, including HPE and Caterpillar.
The following customers accounted for a significant percentage of our total revenue during each of the years ended December 31:
|
| | | | | | | | |
| 2015 | | 2014 | | 2013 |
Caterpillar | 25 | % | | 18 | % | | 14 | % |
HPE | 18 | % | | 1 | % | | 22 | % |
No other customer represented more than 10% of our revenues in any of the years reported. Caterpillar represented 17% and 18% of our outstanding accounts receivable at December 31, 2015 and 2014, respectively. Electronic Keyboards, Inc. and Piet Brouwer Elektrotechniek B.V. represented 24% and 12% of our outstanding receivables at December 31, 2015, respectively.
Advertising Costs
We expense advertising costs as incurred. These expenses were immaterial in 2015, 2014, and 2013, respectively.
Net Loss Per Share
The following table sets forth the computation of basic and diluted net loss per share (in thousands, except per share data) for the years ended December 31:
|
| | | | | | | | | | | |
| 2015 | | 2014 | | 2013 |
Net loss | $ | (6,459 | ) | | $ | (12,827 | ) | | $ | (8,351 | ) |
Basic and diluted: | |
| | |
| | |
|
Weighted-average shares of common stock outstanding used in computing basic and diluted net loss per share | 23,134 |
| | 22,494 |
| | 19,329 |
|
Basic and diluted net loss per share | $ | (0.28 | ) | | $ | (0.57 | ) | | $ | (0.43 | ) |
The calculation of diluted net loss per share excludes 3,461,737, 2,399,890, and 2,407,664 shares of common stock issuable upon exercise of employee stock options as of December 31, 2015, 2014, and 2013, respectively, and 7,121, 21,994, and 53,038 non-vested shares of restricted stock units issuable upon vesting as of December 31, 2015, 2014, and 2013, respectively, because their inclusion in the calculation would be anti-dilutive.
Recent Accounting Pronouncements
In November 2015, the Financial Accounting Standards Board (the "FASB") issued Accounting Standards Update ("ASU") No. 2015-17, ("ASU 2015-17"), Income Taxes (Topic 740): Balance Sheet Classification of Deferred Taxes. The amendments in this update simplify the presentation of deferred income taxes and require that deferred tax liabilities and assets be classified as noncurrent in a classified statement of financial position. This update applies to all entities that present a classified statement of financial position. These amendments may be applied either prospectively to all deferred tax liabilities and assets or retrospectively to all periods presented. If the guidance is applied prospectively, disclosure is made in the first interim and first annual period of change, the nature of and reason for the change in accounting principle and a statement that prior periods were
not retrospectively adjusted. If the guidance is applied retrospectively, disclosure is made in the first interim and first annual period of change, the nature of and reason for the change in accounting principle and quantitative information about the effects of the accounting change on prior periods. The amendments are effective for financial statements issued for annual periods beginning after December 15, 2016, and interim periods within those annual periods. We do not expect the adoption of this standard will have a material effect on our consolidated financial statements.
In July 2015, the FASB issued ASU No. 2015-11, (“ASU 2015-11”), “Inventory (Topic 330): Simplifying the Measurement of Inventory”. ASU 2015-11 requires an entity to measure in scope inventory at the lower of cost and net realizable value. The amendment does not apply to inventory that is measured using the last-in, first-out or the retail inventory method. For public entities, ASU 2015-11 is effective for fiscal years beginning after December 15, 2016, and interim periods within those fiscal years, and is to be applied prospectively. We do not expect the adoption of this standard will have a material effect on our consolidated financial statements.
In April 2015, the FASB issued ASU No. 2015-03, (“ASU 2015-03”), “Interest - Imputation of Interest (Subtopic 835-30): Simplifying the Presentation of Debt Issuance Costs”. ASU 2015-03 requires that debt issuance costs related to a recognized debt liability be presented in the balance sheet as a direct deduction from the carrying amount of that debt liability, consistent with debt discounts. For public entities, ASU 2015-03 is effective for fiscal years beginning after December 15, 2015, and interim periods within those fiscal years. Early adoption is permitted for financial statements that have not been previously issued. ASU 2015-03 is to be applied on a retrospective basis and represents a change in accounting principle. We do not expect the adoption of this standard will have a material effect on our consolidated financial statements.
In August 2014, the FASB issued ASU No. 2014-15, (“ASU 2014-15”), “Disclosure of Uncertainties About an Entity’s Ability to Continue as a Going Concern”. ASU 2014-15 requires management to perform interim and annual assessments of an entity’s ability to continue as a going concern within one year of the date the financial statements are issued and provides guidance on determining when and how to disclose going concern uncertainties in the financial statements. Certain disclosures will be required if conditions give rise to substantial doubt about an entity’s ability to continue as a going concern. ASU 2014-15 applies to all entities and is effective for annual and interim reporting periods ending after December 15, 2016, with early adoption permitted. The Company does not expect that the adoption of this standard will have a material effect on its financial statements.
In May 2014, the FASB issued ASU 2014-09, “Revenue from Contracts with Customers”, “Topic 606”. This ASU will supersede the revenue recognition requirements in Topic 605, Revenue Recognition, and most industry-specific guidance, and creates a Topic 606 Revenue from Contracts with Customers. The core principle of the guidance is that an entity should recognize revenue to depict the transfer of promised goods or services to customers in an amount that reflects the consideration to which the entity expects to be entitled in exchange for those goods or services. In August 2015, the FASB issued ASU 2015-14, Revenue
from Contracts with Customers (Topic 606): Deferral of the Effective Date", which defers the effective date of its new revenue recognition standard by one year. We will adopt this guidance January 1, 2018. We are evaluating the new guidelines to determine if they will have a significant impact on our consolidated results of operation, financial condition or cash flows.
2. Property and Equipment
Property and equipment consists of the following at December 31 (in thousands):
|
| | | | | | | |
| 2015 | | 2014 |
Equipment | $ | 9,040 |
| | $ | 9,122 |
|
Demonstration units | 1,657 |
| | 1,836 |
|
Computers and purchased software | 2,582 |
| | 3,321 |
|
Furnitures and fixtures | 367 |
| | 366 |
|
Leasehold improvements | 7,362 |
| | 7,225 |
|
Construction in progress | 192 |
| | 19 |
|
| 21,200 |
| | 21,889 |
|
Accumulated depreciation | (19,286 | ) | | (19,813 | ) |
| $ | 1,914 |
| | $ | 2,076 |
|
In 2015, we reclassified $0.1 million of inventory into demonstration units. In 2014, we reclassified $44,000 of inventory into demonstration units.
3. Stockholders’ Equity
Common Stock
Common stock reserved for future issuance at December 31, 2015 consisted of 6,333,714 shares of common stock reserved under our 2010 Stock Incentive Plan, of which 3,461,737 shares were subject to outstanding options and restricted shares and 2,871,977 shares were available for future grants of awards.
On May 28, 2014, our stockholders approved an amendment to the Company’s Restated Certificate of Incorporation to increase the number of authorized shares of common stock from 30 million shares to 40 million shares.
In March 2014, we sold approximately 3.7 million shares of common stock at a purchase price of $3.15 per share in a public underwritten offering made under a shelf registration statement that we had filed with the SEC and that had been declared effective in June 2013. This offering resulted in proceeds, net of expenses including underwriting discounts, commissions and fees of $0.8 million and professional service expenses of $0.2 million, of approximately $10.4 million. The proceeds from this offering were used by us to help fund our working capital requirements and for general corporate purposes.
In April 2015, our Board of Directors approved the addition of 3.0 million shares of our common stock to be issued in accordance with our 2010 Equity Incentive Plan, and such addition was subsequently approved by our stockholders. Options are subject to terms and conditions as determined by the Compensation Committee of our Board of Directors.
Stock Option Plan
Since its inception, we have authorized 8,682,296 shares of common stock for issuance under our 2000 and 2010 Stock Incentive Plans, however, we are only issuing new shares of common stock under our 2010 Stock Incentive Plan. The 2000 Stock Incentive Plan has no common stock remaining to issue. We grant options under these plans that vest over periods of up to four years. The term of each option is no more than ten years from the date of grant. Our policy is to issue new shares when required to issue shares upon option exercises. The total fair value of options vested in the year was $1.2 million, $1.8 million, and $1.4 million in 2015, 2014, and 2013 respectively.
A summary of common stock option activity is as follows:
|
| | | | | | | | | | | | |
| Number of Shares | | Weighted- Average Exercise Price | | Weighted- Average Contractual Life (in years) | | Aggregate Intrinsic Value (whole dollars) |
Outstanding at December 31, 2014 | 2,399,890 |
| | $ | 4.30 |
| | | | |
Granted | 1,294,200 |
| | 1.99 |
| | | | |
Exercised | — |
| | — |
| | | | |
Canceled | (232,353 | ) | | 5.35 |
| | | | |
Outstanding at December 31, 2015 | 3,461,737 |
| | $ | 3.36 |
| | 7.81 | | $ | — |
|
Vested and expected to vest at December 31, 2015 | 2,857,574 |
| | $ | 3.59 |
| | 7.58 | | $ | — |
|
Exercisable at December 31, 2015 | 1,405,295 |
| | $ | 4.80 |
| | 6.33 | | $ | — |
|
The weighted average grant date fair value per share of options granted during 2015, 2014, and 2013 was $1.25, $2.03, and $2.60, respectively. The total intrinsic value of options exercised (which is the amount by which the stock price exceeded the exercise price of the options at the date of exercise) during the years ended December 31, 2014 and 2013 was $14,000 and $0.1 million, respectively. There were no options exercised during the year ended December 31, 2015.
As of December 31, 2015, there was $2.7 million of total unrecognized compensation cost, related to non-vested stock options, that is expected to be recognized over a weighted-average vesting period of 2.5 years.
Restricted (non-vested) Shares
In 2013 and 2012, we issued approximately 6,000 and 248,000 restricted shares, respectively, to directors and employees of the Company. The restrictions lapse as the shares vest in equal quarterly installments over a four year period from the date of issuance. We recorded stock compensation expense related to restricted share units of $0.1 million in 2015. A summary of our restricted, non-vested, shares is as follows:
|
| | | | | | |
| Number of Shares | | Weighted- Average Grant Date Fair Value |
Outstanding at December 31, 2014 | 21,994 |
| | $ | 4.00 |
|
Granted | — |
| | — |
|
Vested | (13,528 | ) | | 4.00 |
|
Canceled | (1,345 | ) | | 4.00 |
|
Outstanding at December 31, 2015 | 7,121 |
| | $ | 4.01 |
|
As of December 31, 2015, there was $7,000 of total unrecognized compensation cost related to restricted shares that is expected to be recognized over a weighted-average vesting period of 0.1 years. The total fair value of restricted share units vested in 2015 and 2014 was $0.1 million and $0.1 million, respectively.
4. Revolving Credit Facility
Our Second Amended and Restated Loan and Security Agreement dated August 5, 2010 (as amended on March 5, 2012, August 15, 2012, and July 28, 2014, the “Loan Agreement”) with Silicon Valley Bank (“SVB”) gives us flexibility to help fund our business operations and manage our working capital requirements. The Loan Agreement provides for a secured revolving line of credit with a maturity date of August 5, 2017. We may borrow an aggregate amount of up to eighty percent (80%) of the facility amount of $18.8 million, or $15.0 million, subject to certain borrowing bases. We may also request that SVB issue letters of credit on our behalf, of up to $1.5 million, as a portion of the total facility amount. The facility allows us to borrow against our U.S., U.K. and German accounts receivables and also allows us to borrow against our eligible inventory and purchase orders. Purchase orders and eligible inventory are subject to a borrowing sublimit of $3.0 million and $4.0 million, respectively, and accounts receivable for UK and Germany have a $5.0 million sublimit. However, if we maintain our liquidity ratio at or above 2.50:1.00 for the immediately preceding two reconciliation periods the sublimits will be uncapped. The liquidity ratio is defined as unrestricted
cash, cash equivalents and marketable securities on which bank has a perfected security interest, plus the aggregate amount of eligible accounts receivable accounts divided by all obligations we owe to SVB. The finance charge is a per annum rate equal to Silicon Valley Bank's prime rate, subject to a minimum prime rate of 4.00%, plus (a) 0.50% for eligible accounts, inventory and purchase orders when we are Borrowing Base Eligible, or (b) 1.20% for eligible accounts when we are not Borrowing Base Eligible. We are "Borrowing Base Eligible" when our liquidity ratio is equal to or greater than 1.75:1.00 at all times for at least sixty consecutive days.
The revolving loans made to us under this loan facility are secured by a lien on substantially all of our assets, including the assets of Active Power Solutions Limited, our wholly-owned United Kingdom subsidiary, and the assets of Active Power (Germany) GmbH, our indirect wholly-owned German subsidiary. The only direct or indirect subsidiaries of Active Power, Inc. that are not guarantors under the Loan Agreement are Active Power China (Beijing) Co. Ltd. and immaterial subsidiaries that are not operating companies. There are no restrictions on the ability of any of the subsidiary guarantors to transfer funds to Active Power, Inc. in the form of loans, advances or dividends, except as provided by applicable law.
The Loan Agreement includes customary affirmative covenants for a credit facility of this size and type, including delivery of financial statements, compliance with laws, maintenance of insurance, and protection of intellectual property rights. Further, the Loan Agreement contains customary negative covenants for a credit facility of this size and type, including covenants that limit or restrict our ability, among other things, to dispose of assets, change our business, change our CEO or CFO without replacing such person within 120 days, have a change in control, make acquisitions, be acquired, incur indebtedness, grant liens, make investments, make distributions, repurchase stock, and enter into certain transactions with affiliates.
The Loan Agreement contains customary events of default that include, among other things, non-payment defaults, covenant defaults, material adverse change defaults, insolvency defaults, material judgment defaults and inaccuracy of representations and warranty defaults. The financial covenant requires us to maintain a liquidity ratio equal to or greater than 1.25:1.00. The occurrence of an event of default could result in the acceleration of obligations under the Loan Agreement, in which case we must repay all loans and related charges, fees and amounts then due and payable, and our subsidiary may be required to pay any such amounts under the Guarantee and Debenture. At the election of SVB, upon the occurrence and during the continuance of an event of default, finance charges or interest rates, as applicable, will increase an additional five percentage points (5.00%) per annum above the rate that is otherwise applicable thereto upon the occurrence of such event of default, and the collateral handling fees will increase by one-half percent (0.50%).
We believe we are in and expect to remain in compliance with the covenants and restrictions under the Loan Agreement as of the date of this report. If we fail to stay in compliance with our covenants or experience some other event of default, we may be forced to repay the outstanding borrowings under this credit facility.
During 2012, we borrowed $5.5 million under this credit facility based on our short term liquidity requirements, and have not borrowed any additional amounts after this initial borrowing. As of December 31, 2015, we had outstanding borrowings of $5.5 million under this loan facility. Based on the borrowing base formula subsequent to the amendment, the additional amount available for use at December 31, 2015 was approximately $5.9 million.
5. Income Taxes
The Company’s pretax loss for the three years ended December 31, 2015, 2014, and 2013 were allocated between domestic and foreign operations as follows:
|
| | | | | | | | | | | |
| Year Ended December 31, |
| 2015 | | 2014 | | 2013 |
Domestic | $ | (5,261 | ) | | $ | (15,909 | ) | | $ | (9,105 | ) |
Foreign | (1,198 | ) | | 3,334 |
| | 754 |
|
Total | $ | (6,459 | ) | | $ | (12,575 | ) | | $ | (8,351 | ) |
In September 2014, we settled a tax examination of our German subsidiary for years 2007 through 2011. In the settlement, we agreed to transfer pricing adjustments for the period under examination resulting in a reduction of loss carryovers and a deemed distribution subject to withholding taxes under German law. We recorded a provision for foreign income taxes of $0.3 million in the quarter ended September 30, 2014 related to the settlement of the German tax examination.
As of December 31, 2015, the Company had federal and state net operating loss carry-forwards of approximately $235.5 million and $277.3 million, respectively and research and development credit carry-forwards of approximately $4.1 million. The net operating loss and credit carry-forwards will expire beginning in 2018, if not utilized. Utilization of the federal and state net operating losses and credit carryforwards may be subject to a substantial annual limitation due to the “change of ownership” provisions of the Internal Revenue Code of 1986. The annual limitation may result in the expiration of net operating losses and credit carryforwards before utilization. The Company also has net operating loss carry-forwards related to international operations of approximately $11.7 million.
Deferred income taxes reflect the net tax effects of temporary differences between the carrying amounts of assets and liabilities for financial reporting purposes and the amounts used for income tax purposes. Significant components of the Company’s deferred taxes as of December 31 are as follows (in thousands):
|
| | | | | | | |
| 2015 | | 2014 |
Deferred tax assets: | | | |
Current deferred tax assets | | | |
Reserves and allowances | $ | 698 |
| | $ | 751 |
|
Deferred Rent | 45 |
| | 45 |
|
Deferred revenue | 269 |
| | 255 |
|
Valuation allowance for current deferred tax assets | (1,011 | ) | | (1,049 | ) |
Net current deferred tax assets | $ | 1 |
| | $ | 2 |
|
Noncurrent deferred tax assets | |
| | |
|
Acquired technology | 452 |
| | 571 |
|
Capital expenses | 1,688 |
| | 1,652 |
|
Stock compensation | 695 |
| | 594 |
|
Net operating loss and tax credit carryforwards | 84,436 |
| | 84,047 |
|
Valuation allowance for noncurrent deferred tax assets | (87,108 | ) | | (86,687 | ) |
Net noncurrent deferred tax assets | $ | 163 |
| | $ | 177 |
|
Deferred tax liabilities: | |
| | |
|
Current deferred tax liabilities | |
| | |
|
Prepaid expenses | (164 | ) | | (179 | ) |
Total current deferred tax liabilities | $ | (164 | ) | | $ | (179 | ) |
Total net deferred taxes | $ | — |
| | $ | — |
|
The Company has established a valuation allowance equal to the net deferred tax asset due to uncertainties regarding the realization of deferred tax assets based on the Company’s lack of earnings history. The valuation allowance increased by approximately $0.4 million during 2015. The Company’s deferred tax asset related to NOL carryforwards is net of $2.9 million of unrealized excess tax benefits related to stock based compensation. The impact of the excess tax benefit will be recognized in additional paid-in-capital upon utilization of the Company’s NOL and tax credits carryforward.
The Company’s provision for income taxes differs from the expected tax expense (benefit) amount computed by applying the statutory federal income tax rate of 34% to income before taxes due to the following:
|
| | | | | | | | |
| Year Ended December 31, |
| 2015 | | 2014 | | 2013 |
Federal statutory rate | (34.0 | )% | | (34.0 | )% | | (34.0 | )% |
State taxes, net of federal benefit | (0.8 | ) | | (1.0 | ) | | (13.5 | ) |
R&D credits | (2.2 | ) | | (1.8 | ) | | (5.6 | ) |
Stock compensation | 6.0 |
| | 3.8 |
| | 6.2 |
|
Effect of current foreign operations | 20.5 |
| | 5.5 |
| | (20.5 | ) |
Expiration and adjustment of net operating losses | 2.4 |
| | 26.7 |
| | — |
|
Foreign tax audit settlement | — |
| | 2.0 |
| | — |
|
Loss carryforward adjustments due to tax audit methodologies | — |
| | 9.1 |
| | — |
|
Permanent items and other | 2.2 |
| | 0.3 |
| | (1.9 | ) |
Change in valuation allowance | 5.9 |
| | (8.6 | ) | | 69.3 |
|
| — | % | | 2.0 | % | | — | % |
The Company recognized no material adjustment in the liability for unrecognized income tax benefits. The reconciliation of the Company’s unrecognized tax benefits at the beginning and end of the year is as follows:
|
| | | |
Balance at December 31, 2013 | $ | 1,990 |
|
Additions based on tax positions related to the current year | 257 |
|
Additions for tax positions of prior years | 24 |
|
Balance at December 31, 2014 | $ | 2,271 |
|
Additions based on tax positions related to the current year | 80 |
|
Additions for tax positions of prior years | — |
|
Balance at December 31, 2015 | $ | 2,351 |
|
Due to the existence of the valuation allowance, future changes in our unrecognized tax benefits will not materially impact the Company’s effective tax rate. The Company's assessment of its unrecognized tax benefits is subject to change as a function of the Company's financial statement audit.
The Company recognizes interest and penalties related to uncertain tax positions in income tax expense. As of December 31, 2015, the Company had no accrued interest or penalties related to uncertain tax positions.
The tax years 2010 through 2015 remain open to examination by the major taxing jurisdictions to which the Company is subject.
6. Commitments
We lease our office, manufacturing and engineering facilities and our foreign sales offices under operating lease agreements. These facilities’ leases are non-cancelable and obligate us to pay taxes and maintenance costs. In addition, we lease certain equipment such as copiers and phone systems under non-cancelable leases. Our leases expire at various dates through 2021. Rent expense for leases with escalating or de-escalating rent payments are recorded on a straight-line basis over the period of the lease. Net deferred rent on the consolidated balance sheet as of December 31, 2015 and 2014 was $0.1 million and $0.1 million, respectively. Rent expense was $1.5 million, $1.5 million, and $1.7 million for the years ended December 31, 2015, 2014, and 2013, respectively.
Future minimum payments under these leases at December 31, 2015 are as follows (in thousands):
|
| | | |
| Rental payments |
2016 | $ | 1,243 |
|
2017 | 1,201 |
|
2018 | 1,191 |
|
2019 | 1,174 |
|
2020 | 1,152 |
|
Thereafter | 1,163 |
|
Total future minimum lease payments | $ | 7,124 |
|
We enter into certain commitments to purchase inventory and other items in the course of normal operations. At December 31, 2015, the total of these commitments was $3.6 million, of which $3.6 million and $12,000 will mature in 2016 and 2017, respectively.
We have entered into Severance Benefits Agreements with our Chief Executive Officer (“CEO”) and Chief Financial Officer (“CFO”) and with each of our other executive officers. These agreements generally provide that, if within 12 months following a change in control the executive officer’s employment is terminated for reasons other than for cause (as defined in the agreement) or by the executive for good reason, including a significant reduction in the role and/or responsibility of the executive within 12 months of the change in corporate control, then all outstanding stock options or restricted shares held by the executive would vest as of the date of the termination and certain severance payments would be payable. In the case of our CEO and CFO, in the event of termination by the Company for reasons other than for cause or by him for good reason, he would be entitled to a severance payment equal to 12 months of salary and be entitled to receive health benefits for 12 additional months after termination. In the case of our VP of Sales, in the event of a termination by the Company for reasons other than for cause or by the officer for good reason, he would be entitled to a severance payment equivalent to six months of salary and be entitled to receive health benefits for six additional months after termination.
7. Contingencies
The Company may be involved, either as plaintiff or defendant, in a variety of ongoing claims, demands, suits, investigations, tax matters and proceedings that arise from time to time in the ordinary course of its business. The Company evaluated all potentially significant litigation, government investigations, claims or assessments in which the Company is involved and does not believe that any of these matters, individually or in the aggregate, will result in losses that are materially in excess of amounts already recognized, if any.
The Company records an accrual with respect to a claim, suit, investigation or proceeding when it is reasonably probable that a liability has been incurred and the amount of the loss can be reasonably estimated. Any recorded liabilities, including any changes to such liabilities for the year ended December 31, 2015, were not material to the Consolidated Financial Statements.
The following is a summary of the more significant legal matters involving the Company.
SEC Inquiry
The Company announced in error in April 2013 that it had entered into a strategic distribution agreement with Digital China Information Service Company ("Digital China"). The actual party to this agreement was Qiyuan Network System Limited ("Qiyuan"). A Company employee in China had misrepresented to management that Qiyuan was a subsidiary of Digital China. Qiyuan had no affiliation with Digital China. By letter dated September 30, 2013, the SEC Division of Enforcement notified us that it is conducting an investigation regarding us, including matters relating to our public statements regarding Digital China and our distribution relationships in China. We have been and intend to continue cooperating fully with the SEC. As of the date of this filing, we believe we have provided all requested material to the SEC.
8. Employee Benefit Plan
We maintain a 401(k) Plan that covers substantially all full-time employees. Company contributions to the plan are determined at the discretion of the Board of Directors. We did not contribute to this plan in 2015, 2014, or 2013.
9. Geographic Information
Revenues for the year ended December 31 were as follows (in thousands):
|
| | | | | | | | | | | |
| 2015 | | 2014 | | 2013 |
Americas | $ | 43,068 |
| | $ | 31,495 |
| | $ | 50,365 |
|
Europe, Middle East and Africa | 12,434 |
| | 13,998 |
| | 6,941 |
|
Asia | 1,919 |
| | 3,643 |
| | 4,393 |
|
Total | $ | 57,421 |
| | $ | 49,136 |
| | $ | 61,699 |
|
Revenues from foreign countries above represented shipments to customers located in 43 countries during 2015. We often ship to areas that are outside of the jurisdiction in which revenue is recognized. Substantially all of our property, plant and equipment are located in the United States. Net assets of operations in foreign countries (excluding intercompany receivables and payables eliminated in consolidation) were $3.6 million at December 31, 2015 and are located in the UK, Germany, and China.
10. Guarantees
In certain geographical regions, particularly Europe, we are sometimes required to issue performance guarantees to our customers as a condition of sale. These guarantees usually provide financial protection to our customers in the event that we fail to fulfill our delivery or warranty obligations. We secure these guarantees with standby letters of credit through our bank. At December 31, 2015 we had a $6,000 deposit guarantee for our building lease in Germany, which renews every six months through the term of the lease agreement and a $30,000 performance guarantee to a customer that was secured with a letter of credit, which expires in June 2017. At December 31, 2014, we had a $6,000 deposit guarantee for our building lease in Germany, which renews every six months through the term of the lease agreement and a $34,000 performance guarantee to a customer that was secured with a letter of credit, which expires in June 2017. There is no foreseeable risk that we will not be able to meet the performance obligations. Our restricted cash, as shown on the balance sheet, is related to these guarantees.
11. Selected Quarterly Consolidated Financial Data (unaudited)
The following tables present selected unaudited consolidated statement of operations information for each of the quarters in the years ended December 31, 2015 and 2014 (in thousands, except per share data):
|
| | | | | | | | | | | | | | | | |
| | For the Quarter Ended |
Year Ended December 31, 2015 | | December 31 | | September 30 | | June 30 | | March 31 |
Selected consolidated statement of operations information: | | | | | | | | |
Total revenue | | $ | 12,525 |
| | $ | 14,912 |
| | $ | 16,855 |
| | $ | 13,129 |
|
Total cost of goods sold | | $ | 9,437 |
| | $ | 10,988 |
| | $ | 11,357 |
| | $ | 8,822 |
|
Gross profit | | $ | 3,088 |
| | $ | 3,924 |
| | $ | 5,498 |
| | $ | 4,307 |
|
Operating expenses | | $ | 5,876 |
| | $ | 5,552 |
| | $ | 5,669 |
| | $ | 5,780 |
|
Operating loss | | $ | (2,788 | ) | | $ | (1,628 | ) | | $ | (171 | ) | | $ | (1,473 | ) |
Net loss | | $ | (2,906 | ) | | $ | (1,736 | ) | | $ | (258 | ) | | $ | (1,559 | ) |
Basic and diluted net loss per share | | $ | (0.13 | ) | | $ | (0.08 | ) | | $ | (0.01 | ) | | $ | (0.07 | ) |
| | | | | | | | |
Selected consolidated balance sheet information: | | |
| | |
| | |
| | |
|
Current assets | | $ | 28,403 |
| | $ | 33,091 |
| | $ | 35,149 |
| | $ | 32,323 |
|
Total assets | | $ | 30,595 |
| | $ | 35,435 |
| | $ | 37,355 |
| | $ | 34,499 |
|
Current liabilities | | $ | 16,457 |
| | $ | 18,662 |
| | $ | 19,104 |
| | $ | 16,345 |
|
Working capital | | $ | 11,946 |
| | $ | 14,429 |
| | $ | 16,045 |
| | $ | 15,978 |
|
Long term obligations | | $ | 583 |
| | $ | 630 |
| | $ | 670 |
| | $ | 760 |
|
Stockholders' equity | | $ | 13,555 |
| | $ | 16,143 |
| | $ | 17,581 |
| | $ | 17,394 |
|
|
| | | | | | | | | | | | | | | | |
| | For the Quarter Ended |
Year Ended December 31, 2014 | | December 31 | | September 30 | | June 30 | | March 31 |
Selected consolidated statement of operations information: | | | | | | | | |
Total revenue | | $ | 15,352 |
| | $ | 12,692 |
| | $ | 10,154 |
| | $ | 10,938 |
|
Total cost of goods sold | | $ | 11,303 |
| | $ | 8,932 |
| | $ | 8,239 |
| | $ | 8,010 |
|
Gross profit | | $ | 4,049 |
| | $ | 3,760 |
| | $ | 1,915 |
| | $ | 2,928 |
|
Operating expenses | | $ | 6,015 |
| | $ | 5,862 |
| | $ | 6,221 |
| | $ | 6,574 |
|
Operating profit (loss) | | $ | (1,966 | ) | | $ | (2,102 | ) | | $ | (4,306 | ) | | $ | (3,646 | ) |
Net income (loss) | | $ | (2,044 | ) | | $ | (2,496 | ) | | $ | (4,413 | ) | | $ | (3,874 | ) |
Basic and diluted new income (loss) per share | | $ | (0.09 | ) | | $ | (0.11 | ) | | $ | (0.19 | ) | | $ | (0.19 | ) |
| | | | | | | | |
Selected consolidated balance sheet information: | | |
| | |
| | |
| | |
|
Current assets | | $ | 33,731 |
| | $ | 34,711 |
| | $ | 36,427 |
| | $ | 42,070 |
|
Total assets | | $ | 36,098 |
| | $ | 37,341 |
| | $ | 39,350 |
| | $ | 45,164 |
|
Current liabilities | | $ | 16,484 |
| | $ | 15,720 |
| | $ | 15,529 |
| | $ | 17,069 |
|
Working capital | | $ | 17,247 |
| | $ | 18,991 |
| | $ | 20,898 |
| | $ | 25,001 |
|
Long term obligations | | $ | 821 |
| | $ | 852 |
| | $ | 697 |
| | $ | 746 |
|
Stockholders' equity | | $ | 18,793 |
| | $ | 20,769 |
| | $ | 23,124 |
| | $ | 27,349 |
|
Exhibit
AMENDMENT TO AGREEMENT
HP Agreement No.: [ * ] Amendment No. 1
Supplier: Active Power Inc.
This Amendment to the above referenced Agreement (“Agreement”) is made by and between Hewlett-Packard Company (“HP”) and the above referenced Supplier (“Supplier”).
WHEREAS, HP and Supplier have previously entered into the aforesaid Agreement;
WHEREAS, the purpose of this Amendment is to amend the Agreement as indicated below;
NOW, THEREFORE, for good and valuable consideration, the receipt and sufficiency of which are hereby acknowledged, HP and Supplier hereby agree as follows:
1.The effective date of this Amendment is January 1, 2014 (“Amendment Effective Date”).
| |
2. | Capitalized terms used herein, unless otherwise defined, will have the meanings given in the Agreement. |
| |
3. | This Amendment is subject to the Agreement, and in the event of any conflict between a provision of the Agreement and a provision within this Amendment, then the provision of the Agreement will govern, unless this Amendment expressly states otherwise with specific reference to those provisions in this Amendment that will supersede conflicting provisions in the Agreement. |
| |
4. | This Amendment may be executed in original, faxed, or emailed counterparts, and each counterpart will be considered an original, but all of which together will constitute one and the same instrument. |
| |
5. | The section number on page 5 of the Agreement is changed from “1. Definitions” to “18. Definitions”. |
6. The following additional definitions are added to Section 18 (Definitions) of the Agreement.
“Accumulation Period” – means the period from the [ * ] to the [ * ].
“Batch Maturity Date” – means the [ * ].
“Invoice Batch” – means the [ * ].
“Invoice Qualification Date” - means the latest of: (1) the [ * ], or (2) the [ * ].
“Payment Initiation Date” - means the [ * ] falling on or after the [ * ].
| |
7. | Section 2 (Payment) of the Agreement is deleted in its entirety and replaced with the following language: |
2. Payment. [ * ].
| |
Amend No. 1 to Active Power HPPA [ * ] | Page 1 of 4 |
____________________________________
* Certain information on this page has been omitted and filed separately with the Commission. Confidential treatment has been requested with respect to the omitted portion.
Early payment discount (if any) will be calculated from the Invoice Qualification Date. Payment will be in U.S. currency unless the Parties otherwise agree in writing. Upon HP’s request and at Supplier’s sole expense, Supplier will implement an electronic invoicing process to submit invoices electronically to HP or HP’s third-party service provider in the electronic format specified by HP or such third party service provider. Supplier acknowledges and agrees that use of such process may entail disclosure of information to the service provider about the purchasing relationship between HP and the Supplier, provided that such service provider is bound by confidentiality obligations as to Supplier’s information substantially similar to those provided under these terms.
8. The web link in Section 4.3 (Supplier Compliance Warranties) is changed:
From: https://h20168.www2.hp.com/supplierhandbook/FMF87604.pdf
To: https://h20168.www2.hp.com/supplierextranet/index.do
| |
9. | Module for Notices of the Agreement (page 38) is deleted in its entirety and replaced with a new Module for Notices contained in this Amendment as Attachment 1. |
| |
10. | Except as expressly amended by this Amendment, all other terms and conditions of the Agreement, including any amendments thereto, shall remain in full force and effect. |
IN WITNESS WHEREOF, the authorized representatives of each party, intending to be legally bound hereby, have executed this Amendment as of the Amendment Effective Date. Each of the signatories below certifies that he or she is possessed of all rights and authority to execute this Amendment. Both parties covenant that they will not challenge the legitimacy, terms or enforceability of this Amendment based on the identity or authority of either of the signatories.
Active Power Inc. Hewlett-Packard Company
/s/ Mark A. Ascolese /s/ Colin Todd
Authorized Representative Authorized Representative
January 7, 2014 January 10, 2014
Date Date
Mark A. Ascolese Colin Todd
Printed Name Printed Name
President and CEO Vice President EG Global Supply Management
Printed Title Printed Title
| |
Amend No. 1 to Active Power HPPA [ * ] | Page 2 of 4 |
____________________________________
* Certain information on this page has been omitted and filed separately with the Commission. Confidential treatment has been requested with respect to the omitted portion.
ATTACHMENT 1 to AMENDMENT NO. 1
Module For
HARDWARE PRODUCT PURCHASE AGREEMENT NO. [ * ]
Notices
This Module contains additional provisions related to Notices and forms part of the Hardware Product Purchase Agreement.
Any notice under this Agreement may be delivered by hand, overnight courier, first class pre‑paid letter, facsimile or electronic mail transmission, and will be deemed to have been received: (a) by hand delivery, at the time of delivery; (b) by overnight courier, on the second Business Day after delivery to the carrier; (c) by first class mail, four (4) Business Days after day of mailing or, for international notice, seven (7) Business Days; and (d) by facsimile, immediately upon confirmation of transmission generated by sender’s facsimile machine; or, (e) by electronic mail, immediately upon transmission unless returned as undelivered or returned undeliverable; provided however, for notice of termination or default, a copy must also be sent pre-paid by first class mail, overnight courier, or hand delivered by the end of the next Business Day.
|
| | |
For HP: | | For Supplier |
| | |
Name: [ * ] | | Name: Mark A. Ascolese |
| | |
Title: Director GSM Storage and Infrastructure Procurement | | Title: President & CEO |
| | |
Address: 11445 Compaq Center Drive Houston, Texas 77070-1433 USA | | Address: 2128 West Braker Lane, BK 12 Austin, Texas 78758 |
| | |
Phone Number: [ * ] | | Phone Number: +1 512-836-9245 |
| | |
Fax Number: [ * ] | | Fax Number: +1 512-836-4511 |
| | |
Email: [ * ] | | Email: mascolese@activepower.com |
| |
Amend No. 1 to Active Power HPPA [ * ] | Page 3 of 4 |
____________________________________
* Certain information on this page has been omitted and filed separately with the Commission. Confidential treatment has been requested with respect to the omitted portion.
|
| |
Name: General Counsel | Name: TBD |
| |
Title: Hewlett-Packard Company | Title: |
| |
Address: 3000 Hanover Street | Address: |
Palo Alto, California 94304 | |
| Phone Number: |
| |
| Fax Number: |
| |
| Email: |
| |
Amend No. 1 to Active Power HPPA [ * ] | Page 4 of 4 |
____________________________________
* Certain information on this page has been omitted and filed separately with the Commission. Confidential treatment has been requested with respect to the omitted portion.
Exhibit
AMENDMENT 2 TO HARDWARE PRODUCT PURCHASE AGREEMENT
This is Amendment 2 ("Amendment 2") to the Hardware Product Purchase Agreement with an Effective Date of March 15, 2010 between Active Power, Inc. ("Supplier") and Hewlett Packard Company ("HP") (hereinafter "Agreement").
WHEREAS, HP and Supplier have previously entered into the Agreement;
WHEREAS, the HP and Supplier would like to amend the Agreement as set forth below;
NOW, THEREFORE, for good and valuable consideration, the receipt and sufficiency of which are hereby acknowledged, HP and Supplier hereby agree as follows:
I. The effective date of this Amendment 2 is April 1, 2015 ("Amendment 2 Effective Date").
2. Capitalized terms used herein, unless otherwise defined, will have the meanings set forth in the Agreement.
3. This Amendment 2 is subject to the Agreement, and in the event of any conflict between a provision of the Agreement and a provision of this Amendment 2, then the provision of the Agreement will govern, unless this Amendment expressly states otherwise with specific reference to those provisions in this Amendment that will supersede conflicting provisions in the Agreement.
4. This Amendment 2 may be executed in original, faxed, or emailed counterparts, and each counterpart will be considered an original, but all of which together will constitute one and the same instrument.
5. Section 17.3 ("Assignment'') of the Agreement is deleted in its entirety and replaced with the following:
17.3 Assignment. Neither this Agreement nor any right or duty under this Agreement or any Accepted Order may be transferred, assigned or delegated by each Party, by operation of law or otherwise, without the prior written consent of the other Party, and any attempted transfer, assignment or delegation without such consent will be void and without effect. Notwithstanding the above, HP may assign this Agreement to any affiliate or successor-in-interest including without limitation any HP Split-Up Entity. "HP Split-Up Entity" means any entity (current and future, and respective successors in interest) that results from HP's contemplated separation of its personal computer and printing businesses from its enterprise businesses as publicly announced by HP on October 6, 2014.
6. The attached Exhibit 2 is added as an exhibit and SOW to the Product Customization Module of the Agreement. For clarification, the Product Customization Module of the Agreement only applies to the Customized Products specifically listed in Exhibits l and 2 to the Product Customization Module.
7. The Product Description, Product Specifications and Pricing Module of the Agreement is deleted in its entirety and replaced with the attached Product Description and Product Specifications Pricing Module.
8. Except as expressly amended by this Amendment, all other terms and conditions of the Agreement, including any amendments thereto, shall remain in full force and effect.
Hewlett Packard Company HP and Active Power
Amend No. 2 to Active Power HPPA [ * ]
______________________
* Certain information on this page has been omitted and filed separately with the Commission. Confidential treatment has been requested with respect to the omitted portion.
IN WITNESS WHEREOF, the authorized representatives of each party. intending to be legally bound hereby. have executed this Amendment 2 as of the Amendment 2 Effective Date. Each of the signatories below certifies that he or she is possessed of all rights and authority to execute this Amendment 2.
_______________________________________________________________________________________________
|
| | |
Active Power, Inc.
| | Hewlett-Packard Company
|
/s/ Mark A. Ascolese | | /s/ Colin Todd |
Authorized Representative
| | Authorized Representative |
April 20, 2015 | | 4/22/2015 |
Date | | Date |
Mark A. Ascolese | | Colin Todd |
Printed Name | | Printed Name |
President and CEO | | Vice President EG Global Supply Management |
Printed Title | | Printed Title |
Hewlett Packard Company HP and Active Power
Amend No. 2 to Active Power HPPA [ * ]
______________________
* Certain information on this page has been omitted and filed separately with the Commission. Confidential treatment has been requested with respect to the omitted portion.
Exhibit 2
To tbe Product Customization Module
The following arc Customized Products:
|
| |
Part Number: | Description: |
[ * two-page table omitted] |
Hewlett Packard Company HP and Active Power
Amend No. 2 to Active Power HPPA [ * ]
______________________
* Certain information on this page has been omitted and filed separately with the Commission. Confidential treatment has been requested with respect to the omitted portion.
Product Description and Product Specifications Module
This Module contains additional provisions related to Product description(s) and Product Specifications.
I. Additional Products and any changes to HP part numbers and Product Specifications may be documented by the Parties and set forth in: (1) an amendment to this Module, or (2) in a written notification (email) or an electronic Request For Quote process that: (i) identifies the Product; and (ii) at HP's option, identifies this Agreement.
2. Product will conform to the Product Specifications listed in Table I below.
3. In addition, Supplier warrants that its manufacture and provision of any [ * ] and/or Product that contains a [ * ], if any, complies with the HP Specifications pertaining to [ * ] identified on the HP Supplier Handbook located at https://h20168.www2.hp.com/supplierextranet/index.do.
Table 1: Product Description and Product Specifications
|
| |
Part Number: | Description: |
[ * three-page table omitted] |
Hewlett Packard Company HP and Active Power
Amend No. 2 to Active Power HPPA [ * ]
______________________
* Certain information on this page has been omitted and filed separately with the Commission. Confidential treatment has been requested with respect to the omitted portion.
Exhibit
SUBSIDIARIES OF THE REGISTRANT
|
| |
Name of Subsidiary | Country of Incorporation |
| |
Active Power (Switzerland) AG | Switzerland |
| |
Active Power Solutions Limited | United Kingdom |
| |
Active Power (Germany) GmbH | Germany |
| |
Active Power (Hong Kong) Limited | Hong Kong |
| |
Active Power (Beijing) Co. Limited | China |
Exhibit
Consent of Independent Registered Public Accounting Firm
We have issued our report dated February 23, 2016, with respect to the consolidated financial statements included in the Annual Report of Active Power, Inc. on Form 10-K for the year ended December 31, 2015. We consent to the incorporation by reference of said report in the Registration Statements of Active Power, Inc. on Forms S-3 (File No. 333-188242 and File No. 333-181054) and on Forms S-8 (File No. 333-43248, File No. 333-56122, File No. 333-104725, File No. 333-115039, File No. 333-123587, File No. 333-132792, File No. 333-144782, File No. 333-150481, File No. 333-157662, File No. 333-165217, File No. 333-167005, File No. 333-181948 and File No. 333-203750).
/s/ GRANT THORNTON LLP
Dallas, Texas
February 23, 2016
Exhibit
Exhibit 31.1
CERTIFICATION
PURSUANT TO 17 CFR 240.13a -14
PROMULGATED UNDER
SECTION 302 OF THE SARBANES-OXLEY ACT OF 2002
I, Mark A. Ascolese, certify that:
| |
1. | I have reviewed this report on Form 10-K of Active Power, Inc.; |
| |
2. | Based on my knowledge, this report does not contain any untrue statement of a material fact or omit to state a material fact necessary to make the statements made, in light of the circumstances under which such statements were made, not misleading with respect to the period covered by this report; |
| |
3. | Based on my knowledge, the financial statements, and other financial information included in this report, fairly present in all material respects the financial condition, results of operations and cash flows of the registrant as of, and for, the periods presented in this report; |
| |
4. | The registrant’s other certifying officer(s) and I are responsible for establishing and maintaining disclosure controls and procedures (as defined in Exchange Act Rules 13a-15(e) and 15d-15(e)) and internal control over financial reporting (as defined in Exchange Act Rules 13a-15(f) and 15d-15(f)) for the registrant and have: |
| |
(a) | designed such disclosure controls and procedures, or caused such disclosure controls and procedures to be designed under our supervision, to ensure that material information relating to the registrant, including its consolidated subsidiaries, is made known to us by others within those entities, particularly during the period in which this report is being prepared; |
| |
(b) | designed such internal control over financial reporting, or caused such internal control over financial reporting to be designed under our supervision, to provide reasonable assurance regarding the reliability of financial reporting and the preparation of financial statements for external purposes in accordance with generally accepted accounting principles; |
| |
(c) | evaluated the effectiveness of the registrant’s disclosure controls and procedures and presented in this report our conclusions about the effectiveness of the disclosure controls and procedures, as of the end of the period covered by this report based on such evaluation; and |
| |
(d) | disclosed in this report any change in the registrant’s internal control over financial reporting that occurred during the registrant’s most recent fiscal quarter (the registrant’s fourth fiscal quarter in the case of an annual report) that has materially affected, or is reasonably likely to materially affect, the registrant’s internal control over financial reporting; and |
| |
5. | The registrant’s other certifying officer(s) and I have disclosed, based on our most recent evaluation of internal control over financial reporting, to the registrant’s auditors and the audit committee of the registrant’s board of directors (or persons performing the equivalent functions): |
| |
(a) | all significant deficiencies and material weaknesses in the design or operation of internal control over financial reporting which are reasonably likely to adversely affect the registrant’s ability to record, process, summarize and report financial information; and |
| |
(b) | any fraud, whether or not material, that involves management or other employees who have a significant role in the registrant’s internal control over financial reporting. |
Date: February 23, 2016
|
|
/s/ MARK A. ASCOLESE |
Mark A. Ascolese |
President and Chief Executive Officer |
Exhibit
Exhibit 31.2
CERTIFICATION
PURSUANT TO 17 CFR 240.13a -14
PROMULGATED UNDER
SECTION 302 OF THE SARBANES-OXLEY ACT OF 2002
I, James A. Powers, certify that:
| |
1. | I have reviewed this report on Form 10-K of Active Power, Inc.; |
| |
2. | Based on my knowledge, this report does not contain any untrue statement of a material fact or omit to state a material fact necessary to make the statements made, in light of the circumstances under which such statements were made, not misleading with respect to the period covered by this report; |
| |
3. | Based on my knowledge, the financial statements, and other financial information included in this report, fairly present in all material respects the financial condition, results of operations and cash flows of the registrant as of, and for, the periods presented in this report; |
| |
4. | The registrant’s other certifying officer(s) and I are responsible for establishing and maintaining disclosure controls and procedures (as defined in Exchange Act Rules 13a-15(e) and 15d-15(e)) and internal control over financial reporting (as defined in Exchange Act Rules 13a-15(f) and 15d-15(f)) for the registrant and have: |
| |
(a) | designed such disclosure controls and procedures, or caused such disclosure controls and procedures to be designed under our supervision, to ensure that material information relating to the registrant, including its consolidated subsidiaries, is made known to us by others within those entities, particularly during the period in which this report is being prepared; |
| |
(b) | designed such internal control over financial reporting, or caused such internal control over financial reporting to be designed under our supervision, to provide reasonable assurance regarding the reliability of financial reporting and the preparation of financial statements for external purposes in accordance with generally accepted accounting principles; |
| |
(c) | evaluated the effectiveness of the registrant’s disclosure controls and procedures and presented in this report our conclusions about the effectiveness of the disclosure controls and procedures, as of the end of the period covered by this report based on such evaluation; and |
| |
(d) | disclosed in this report any change in the registrant’s internal control over financial reporting that occurred during the registrant’s most recent fiscal quarter (the registrant’s fourth fiscal quarter in the case of an annual report) that has materially affected, or is reasonably likely to materially affect, the registrant’s internal control over financial reporting; and |
| |
5. | The registrant’s other certifying officer(s) and I have disclosed, based on our most recent evaluation of internal control over financial reporting, to the registrant’s auditors and the audit committee of the registrant’s board of directors (or persons performing the equivalent functions): |
| |
(a) | all significant deficiencies and material weaknesses in the design or operation of internal control over financial reporting which are reasonably likely to adversely affect the registrant’s ability to record, process, summarize and report financial information; and |
| |
(b) | any fraud, whether or not material, that involves management or other employees who have a significant role in the registrant’s internal control over financial reporting. |
Date: February 23, 2016
|
|
/s/ JAMES A. POWERS |
James A. Powers Vice President of Finance, Chief Financial Officer |
Exhibit
Exhibit 32.1
CERTIFICATION PURSUANT TO
18 U.S.C. SECTION 1350,
AS ADOPTED PURSUANT TO
SECTION 906 OF THE SARBANES-OXLEY ACT OF 2002
In connection with the Annual Report of Active Power, Inc. (the “Company”) on Form 10-K for the period ending December 31, 2014 as filed with the Securities and Exchange Commission on the date hereof (the “ Report ”), I, Mark A. Ascolese, President and Chief Executive Officer of the Company, hereby certify, pursuant to 18 U.S.C. Section 1350, as adopted pursuant to Section 906 of the Sarbanes-Oxley Act of 2002, that:
| |
1. | The Report fully complies with the requirements of section 13(a) or 15(d) of the Securities Exchange Act of 1934; and |
| |
2. | The information contained in the Report fairly presents, in all material respects, the financial condition and results of operations of the Company. |
Date: February 23, 2016
|
|
/s/ MARK A. ASCOLESE |
Mark A. Ascolese President and Chief Executive Officer |
Exhibit
Exhibit 32.2
CERTIFICATION PURSUANT TO
18 U.S.C. SECTION 1350,
AS ADOPTED PURSUANT TO
SECTION 906 OF THE SARBANES-OXLEY ACT OF 2002
In connection with the Annual Report of Active Power, Inc. (the “Company”) on Form 10-K for the period ending December 31, 2014 as filed with the Securities and Exchange Commission on the date hereof (the “ Report ”), I, James A. Powers, Vice President of Finance, Chief Financial Officer of the Company, hereby certify, pursuant to 18 U.S.C. Section 1350, as adopted pursuant to Section 906 of the Sarbanes-Oxley Act of 2002, that:
| |
1. | The Report fully complies with the requirements of section 13(a) or 15(d) of the Securities Exchange Act of 1934; and |
| |
2. | The information contained in the Report fairly presents, in all material respects, the financial condition and results of operations of the Company. |
Date: February 23, 2016
|
|
/S/ JAMES A. POWERS |
James A. Powers Vice President of Finance, Chief Financial Officer |